「クリーンルームクラス10000とは」と検索している方へ向けて、この記事ではクリーンルームとは何か、その役割や構造、設計のポイントをはじめ、クリーンルームクラスの違いや用途に応じた作り方までわかりやすく解説します。
特にクリーンルームクラス1000やクラス10000の違い、湿度管理や入室手順、適切な服装、さらにはエアシャワーやグレーチングといった設備の役割、ISOによるクリーンルーム規格にも触れ、基礎から応用までを網羅。クリーンルームライトや掃除機といった環境維持に欠かせない用具についても紹介し、効率的なクリーンルーム設計と運用をサポートする内容となっています。
- クリーンルームクラス10000の定義と粒子基準
- クラス10000が適用される製品や工程の具体例
- クラス10000と他クラス(例:クラス1000)の違い
- クラス10000に必要な設備や構造の特徴
クリーンルームクラス10000とはその基礎知識
クリーンルームは、空気中の微細なホコリや細菌を極限まで排除し、製品の品質や安全性を確保するために設けられた特殊な環境です。半導体や医薬品の製造現場ではもちろん、カメラやレンズといった光学機器においても、微粒子によるわずかな汚染が致命的な影響を及ぼすため、その重要性は極めて高いものとなっています。
本記事では、クリーンルームの基本的な役割から、その清浄度のクラス分類、規格の違い、さらにはカメラ製造への適用例や方式の選定までをわかりやすく解説していきます。
クリーンルームとは何か?その役割と特徴
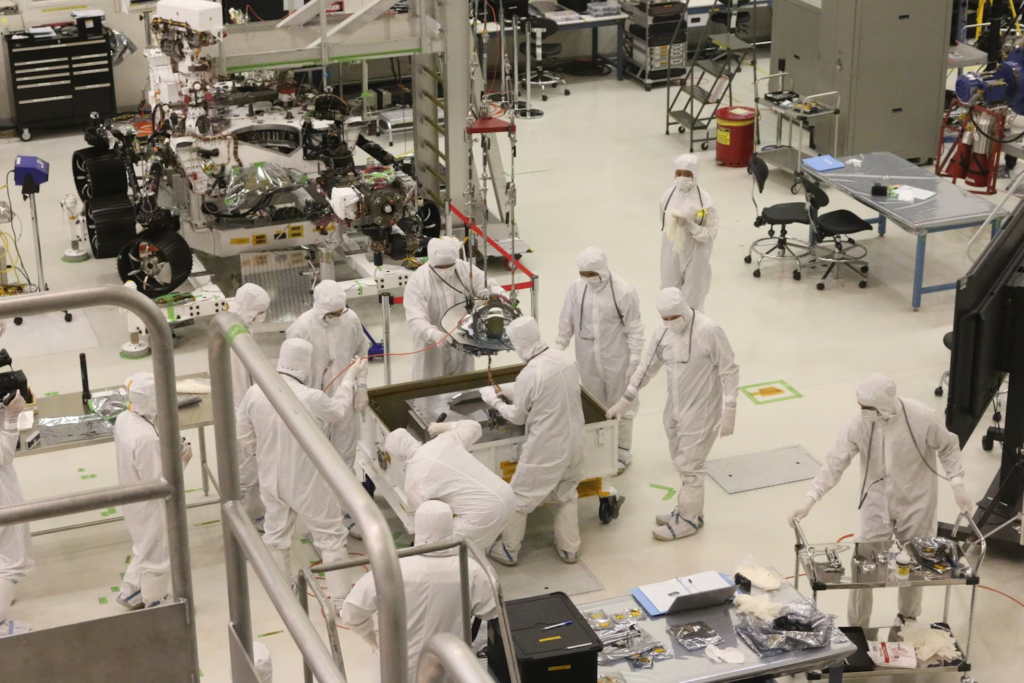
現在、クリーンルームとは、空気中にある小さなホコリや細菌などをしっかりコントロールする特別な部屋のことを指します。特に、細かい作業が求められる電子部品や薬の製造には欠かせない場所です。
この説明だけだと少しイメージしづらいかもしれませんが、クリーンルームは空気の中のゴミの量を数値で測って、それが一定以下になるように管理されています。空気の流れやフィルターを使って、ホコリや菌が入らないようにして、常に清潔な状態を保っています。
例えば、スマートフォンに使われる半導体の製造や、注射薬などの清潔さが必要な薬の入れ物を作る工程などが、クリーンルームの中で行われます。こうした作業では、製品の品質や安全を守るために、クリーンルームがとても重要な役割を果たしているのです。
また、カメラやレンズなどの光学機器の製造でも、クリーンルームは欠かせません。なぜなら、異物や微粒子がレンズやセンサーに付着すると、画質に大きな影響を与えるからです。例えば、製造過程でレンズの表面や内部に微細なチリが入り込むと、それが画像に黒点やぼやけとして現れる可能性があります。センサー上に付着した微粒子は、画像の一部を完全に無効化することもあり、製品の品質に重大な問題を引き起こします。
高精細な画像が求められるカメラ製品では、極めて小さな異物でさえも製品不良の原因になります。そのため、光学機器の製造現場では、異物混入を未然に防ぐことが必須条件となっており、クリーンルーム環境の整備は当然の措置とされています。
クリーンルームによって安定した空気環境を維持し、微粒子の発生を極限まで抑えることで、ようやく品質の高いカメラ製品が安定的に生産できるのです。
クリーンルームクラス(Class)の分類と基準
このため、クリーンルームは清浄度に応じて複数のクラスに分けられています。これを「クリーンルームクラス」と呼び、空気1立方フィート(約28.3リットル)中に存在する粒子の数によって分類されます。粒子数が少ないほど清浄度が高いとされ、その数値によってクラスの名称が決まる仕組みです。
例えば、クラス100は非常に高い清浄度を持ち、0.5μm以上の粒子が空気中に100個以下(約28.3リットルあたり)しか存在しないレベルを意味します。一方、クラス10000はその名の通り、同じ大きさの粒子が最大10000個まで許容される基準となっています。
このクラスは、厳密な清浄度は必要としないが、一定の管理が求められる多くの製造現場で採用されています。
各クリーンルームクラスの定義(FED-STD-209E)
以下は、米国連邦規格(FED-STD-209E)における代表的なクリーンルームクラスの定義です。
- クラス1:0.5μm以上の粒子が空気1立方フィート(約28.3L)中に1個以下
- クラス10:0.5μm以上の粒子が10個以下
- クラス100:0.5μm以上の粒子が100個以下
- クラス1,000:0.5μm以上の粒子が1,000個以下
- クラス10,000:0.5μm以上の粒子が10,000個以下
- クラス100,000:0.5μm以上の粒子が100,000個以下
クラスの数字が大きくなるほど、空気中に存在する粒子の数が多く許容されるため、清浄度のレベルは下がっていきます。
ISO規格との違いとISOクラスの対応
さらに、このクリーンルームクラスの分類は、主に米国連邦規格(FED-STD-209E)に基づいていますが、現在では国際的にはISO(国際標準化機構)の規格「ISO 14644-1」が広く使われています。
ISO規格では、空気1立方メートル(=1000L)あたりの粒子数で清浄度を定義しており、より細分化された9つのクラス(ISOクラス1~9)があります。
以下の表は、ISO 14644-1に基づく各クラスの粒径別上限粒子数です。
<ISO 14644-1による清浄度クラスの定義(代表値)>
ISOクラス | ≥0.1μm | ≥0.2μm | ≥0.3μm | ≥0.5μm | ≥1.0μm | ≥5.0μm |
---|---|---|---|---|---|---|
ISO 1 | 10 | 2 | – | – | – | – |
ISO 2 | 100 | 24 | 10 | 4 | – | – |
ISO 3 | 1,000 | 237 | 102 | 35 | 8 | – |
ISO 4 | 10,000 | 2,370 | 1,020 | 352 | 83 | – |
ISO 5 | 100,000 | 23,700 | 10,200 | 3,520 | 832 | 29 |
ISO 6 | – | – | – | 35,200 | 8,320 | 293 |
ISO 7 | – | – | – | 352,000 | 83,200 | 2,930 |
ISO 8 | – | – | – | 3,520,000 | 832,000 | 29,300 |
ISO 9 | – | – | – | 35,200,000 | 8,320,000 | 293,000 |
※単位:個/m³
この表は、クリーンルームの使用目的や製品仕様に応じて適切な環境を設計するうえで重要な指標となります。
<クリーンルームクラス比較表(FED規格とISO規格の対応)>
FEDクラス | ISOクラス | 粒子サイズ(0.5μm)基準粒子数/立方m(1000L) |
---|---|---|
クラス1 | ISOクラス3 | 約35個以下 |
クラス10 | ISOクラス4 | 約352個以下 |
クラス100 | ISOクラス5 | 約3,520個以下 |
クラス1,000 | ISOクラス6 | 約35,200個以下 |
クラス10,000 | ISOクラス7 | 約352,000個以下 |
クラス100,000 | ISOクラス8 | 約3,520,000個以下 |
このように、クリーンルームのクラスは用途や必要な清浄度に応じて使い分けられており、製造する製品の特性によって最適なクラスの選定が求められます。ISOクラスを理解しておくことで、グローバルな品質管理体制にも柔軟に対応することができ、設計・導入の際の指標として非常に有効です。
クラス100000はカメラ組立に十分か?
クリーンルームクラス100000は、空気1立方フィート(約28.3L)あたりに0.5μm以上の粒子が最大100,000個まで許容されるレベルの清浄度です。このレベルは、一般的な電子機器の組立や一部の工業製品の製造に用いられますが、高精細な光学機器であるカメラの製造に適しているかどうかは慎重に判断する必要があります。
たとえば、現代のデジタルカメラやスマートフォンに使われるイメージセンサー(CMOS)は非常に小さく、1ピクセルあたりのサイズは一般的に約1.0μm〜1.5μm程度です。高画素化が進んでいるセンサーでは、0.8μm以下のピクセルピッチも珍しくありません。
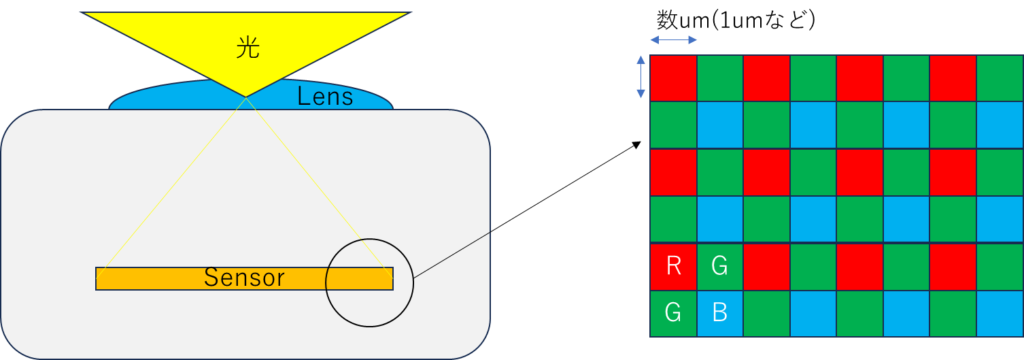
このような極小のセンサー表面に0.5μm以上の異物が付着すると、1ピクセルまたはそれ以上の画素を完全に覆ってしまう可能性があります。結果として、撮影画像に「黒点」や「シミ」のような欠陥が生じ、製品クレームや歩留まりの低下につながるのです。
また、カメラのレンズも非常に精密な光学部品であり、異物が1つでも内部に入り込むと、光の屈折や反射に悪影響を及ぼし、画質が著しく低下するリスクがあります。特に高解像度のレンズは、光学的な誤差を極限まで抑えるよう設計されているため、数μmレベルの異物でも製品不良の原因になりえます。
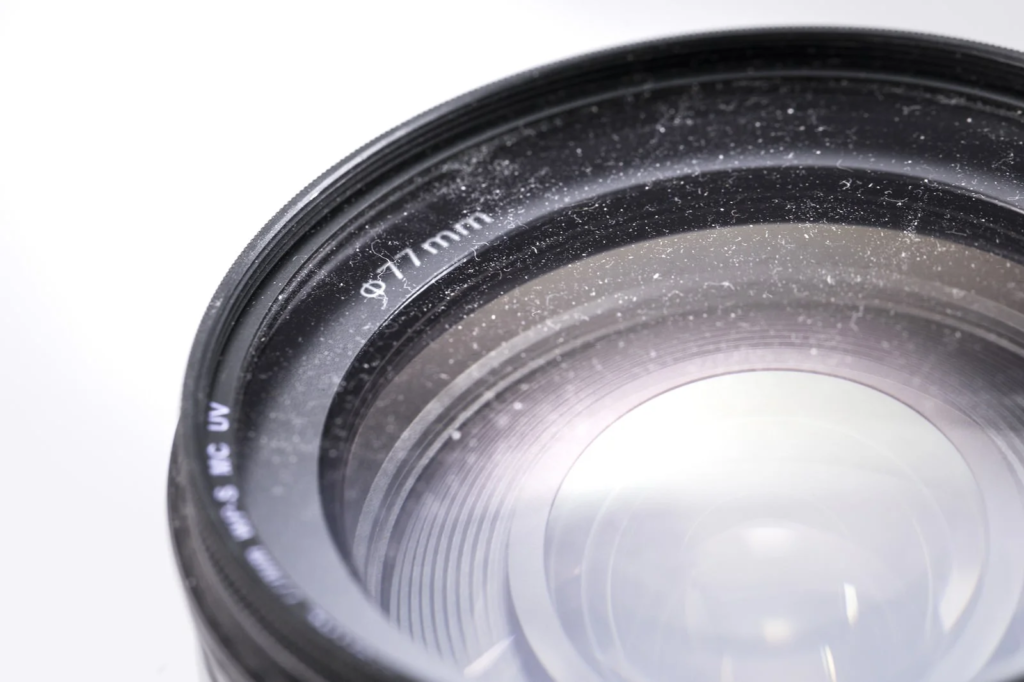
このような背景から、多くのカメラ製造ラインではクラス10000(0.5μm粒子が28.3L中に最大10,000個)やクラス1000(1,000個)以上の清浄度が求められることが一般的です。クラス100000はカメラ製造の前工程やパッケージングなどには使用されることもありますが、センサーやレンズの組立・調整といった繊細な工程には不十分であるといえるでしょう。
結論として、クラス100000のクリーンルームはカメラ組立において完全には適さない場合が多く、クラス10000またはそれ以上の清浄度が必要とされる場面が多く存在します。製品の品質要件や求められる画質レベルに応じて、適切なクラスの選定が極めて重要です。
クリーンルームクラス1000との違いとは?
言ってしまえば、クラス1000はクラス10000よりも10倍厳しい基準を持つクリーンルームです。クラス1000では、空気中に含まれる微粒子の数がさらに厳しく制限されており、極めて高い清浄度が必要とされます。
例えば、同じ空間で扱う製品でも、クラス1000はより微細な作業や微粒子による影響を極力排除したい工程に適しており、代表的な例としては半導体製造や精密機器の加工が挙げられます。特に、ナノレベルの構造を扱う作業では、わずかなチリでも大きな障害となるため、クラス1000の清浄環境が不可欠です。
一方で、クラス10000はそこまでの厳密な清浄度は求められない工程、例えば電子部品の組立や医療機器の部分組立など、比較的広範な用途に適しています。このクラスでも一定の粒子管理はされていますが、微細な加工を行う現場ほどの高精度は必要とされません。
このため、コストや設備の複雑さ、日常的な管理の手間なども考慮に入れながら、製品や作業内容の特性に応じた適切なクラスを選定することが重要です。適切なクラス設定により、品質と効率のバランスを保つことが可能になります。
クリーンルーム規格 ISOとの関係性
ここで、国際的な基準であるISO規格にも触れておきましょう。クリーンルームのISO規格の中でも「ISO 14644-1」は最も広く知られており、設計や運用における基本的な指針となっています。
この規格では、空気中に存在する粒子の大きさごとに上限値を定め、それに基づいてクリーンルームをISOクラス1から9までの9段階に分類しています。クラスの数字が小さいほど空気中の粒子数が少なく、高い清浄度が保たれていることを意味します。
ISO 14644シリーズの他の規格
- ISO 14644-2:モニタリングの仕様
- 清浄度を維持するために必要な定期モニタリング方法や検証基準を定めています。
- 長期運用における品質管理のために不可欠な指針です。
- ISO 14644-3:試験方法
- クリーンルームの性能試験方法について規定しており、HEPAフィルターの漏れ試験や気流の可視化などが含まれます。
- ISO 14644-4:設計と建設
- クリーンルームのレイアウトやゾーニング、空調システムの構築方法など、設計・施工に関する要件を示しています。
- ISO 14644-5:運用
- 日常運用、作業者の入退室、服装、清掃手順など、実際の使用に関する管理項目を定めています。
- ISO 14644-6:技術的パラメーター
- 設備や構造に影響する様々な要素について、データの測定や分析に基づいた運用基準を提供しています。
- ISO 14644-7:シークレットゾーン(バリアシステム)
- アイソレーターやミニエンクロージャーといった特殊な隔離環境に関する指針です。
- ISO 14644-8:化学的汚染制御
- 空気中の化学物質(揮発性有機化合物など)の制御と測定に関するガイドラインです。
- ISO 14644-9:表面の清浄度(粒子)
- 空気中だけでなく、表面に残る粒子汚染を測定し評価するための基準です。
- ISO 14644-10:表面の清浄度(化学的)
- 表面に付着する化学物質の清浄度を評価するためのガイドラインです。
その他の関連規格
- ISO 13485(医療機器の品質マネジメント)
- 医療機器製造においては、清浄度管理の一環としてISO 13485の要件を満たす必要があります。
- クリーンルームの運用にも直接的な影響があります。
- GMP(Good Manufacturing Practice:適正製造基準)
- 医薬品や化粧品分野で適用される規制で、クリーンルーム管理に関する具体的な運用基準が含まれています。
- 特に空調管理、交差汚染防止、作業者教育などが重視されます。
- FED-STD-209E(旧米国連邦規格)
- すでに廃止されていますが、現在も一部の業界では使用されることがあり、ISO 14644と比較される際に参照されます。
このように、ISO 14644-1はクリーンルーム規格の中心ではあるものの、それを補完・拡張する関連規格が多数存在します。製品の種類や業界の規制に応じて適切な規格を把握・運用することが、品質管理と国際基準対応の鍵となります。
クリーンルーム方式の種類と選び方
クリーンルームの運用において、「どのように空気を循環させるか」という“方式”の選定は、清浄度の維持と効率的な管理に直結します。主に用いられるのは「乱流方式」「層流方式」、およびこれらを組み合わせた「混合方式(ハイブリッド)」の3つです。それぞれの特徴と、用途に適した選び方を以下にまとめます。
1. 層流方式(Laminar Flow)
空気が天井や壁から一方向に直線的に流れる構造です。粒子が空間に滞留しにくく、非常に高い清浄度を維持しやすい点が最大の特徴です。主にクラス100〜1000といった高清浄度のクリーンルームで用いられます。
特徴:
- 空気の流れが一方向に一定
- 粒子の拡散を抑制
- HEPAフィルターを天井全面に配置
適した用途:
- 半導体製造
- バイオ医薬品の充填
- 光学機器(カメラやレンズなど)の組立
カメラ製品との関係: カメラのレンズやセンサーは微細な異物でも画質に重大な影響を及ぼすため、異物の堆積リスクが最も低い層流方式が最適とされます。微粒子の滞留を最小限に抑えられることが、歩留まり向上とクレーム低減に直結します。
2. 乱流方式(Turbulent Flow)
空気が室内に広がるようにランダムに拡散し、全体を包み込むように循環する方式です。層流方式ほど高い清浄度は期待できませんが、設計・運用コストが低く、広い空間で均一な空気環境を保ちやすいのが利点です。
特徴:
- 空気の流れが不規則で多方向
- 部屋全体に空気を満遍なく循環
- 初期コスト・管理コストが比較的低い
適した用途:
- 電子部品の組立
- 医療機器の組立
- 試験研究室や一般的な製造環境
3. 混合方式(ハイブリッド方式)
層流と乱流の長所を組み合わせた方式で、作業エリアの周囲では層流を確保しつつ、周辺は乱流で空気を循環させる構造です。コストパフォーマンスと清浄度のバランスに優れており、近年では多くの製造現場で採用されています。
特徴:
- 部分的に層流を確保しつつ全体を乱流で補完
- 設計の自由度が高く、柔軟なレイアウトが可能
適した用途:
- 複数工程を同空間で行う製造現場
- 製造ラインの一部で高清浄度を要する場合
<クリーンルーム方式の比較表>
方式 | 特徴 | 清浄度適用範囲 | 初期コスト | カメラ製造適性 |
---|---|---|---|---|
層流方式 | 一方向に空気が流れ、粒子が滞留しにくい | クラス100〜1000 | 高 | ◎ |
乱流方式 | 空気が全体に拡散、コスト低め | クラス10000〜 | 中 | △ |
混合方式 | 必要箇所に層流を導入、柔軟な設計可能 | クラス1000〜10000 | 中〜高 | ○ |
このように、それぞれの方式は目的や製品特性に応じた選択が求められます。カメラ製品のように異物の影響が致命的な分野では、層流方式が推奨されますが、作業工程やコストとの兼ね合いで混合方式を導入するケースもあります。目的に応じて最適な方式を選ぶことが、高品質な製品を安定的に生産する鍵となります。
クリーンルームクラス10000とは?その設計と運用
クリーンルームは、微細なホコリや粒子の影響を最小限に抑え、製品の品質と安全を確保するために設計された特別な作業空間です。その環境を保つためには、構造・設備・運用ルールすべてに高い精度と管理が求められます。
本記事では、クリーンルームの構造や清浄度維持のための設備、常設型と簡易型の違い、入室時の服装や手順、さらに照明や掃除機の選び方まで、現場で役立つ具体的な知識を幅広く解説します。導入・運用の前にぜひ押さえておきたい内容です。
クリーンルームの構造と設計ポイント
クリーンルームの構造は、空気中の微粒子や汚染物質の侵入を防ぎ、高い清浄度を維持するために非常に重要です。壁材、天井、床といった構造要素は、粒子を発生しにくく、かつ付着しにくい特殊な素材で構成されており、清掃やメンテナンスのしやすさも考慮されています。これにより、長期的かつ安定的に清浄環境を維持することが可能となります。設計段階でこうした素材や構造を厳選することが、クリーンルームの性能を左右する大きなポイントとなります。
清浄度を高めるための重要なポイントと設備
以下の各要素は、クリーンルームの清浄度を高め、運用中も安定して維持するために必要不可欠な構成要素です。
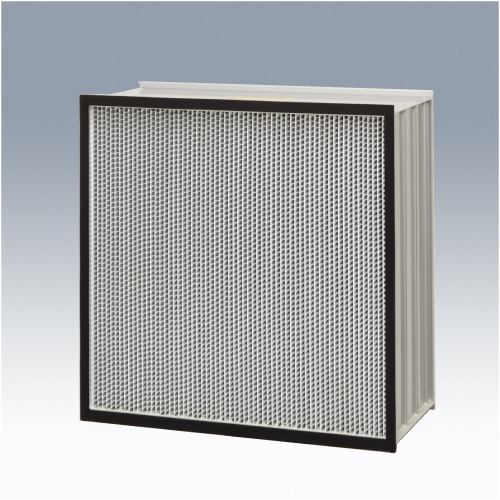
- HEPA/ULPAフィルターの導入
- 役割:空気中の微粒子を高精度で除去し、室内への侵入を防止。
- 重要性:清浄度維持の中核であり、性能低下は室内の粒子濃度上昇に直結する。特にISOクラス5以下ではULPAフィルターが求められる。
- 気流の制御(層流方式/乱流方式)
- 役割:空気を効率的に循環させ、粒子の拡散を防ぐ。
- 重要性:用途に応じた選定が不可欠。層流は高清浄度、乱流は広範囲に適する。
- プレルームとエアシャワーの設置
- 役割:作業員や物品の表面から粒子を除去し、室内への異物侵入を防止。
- 重要性:外部由来の汚染リスクを大幅に減らす、最終防衛ラインとして機能する。
- 防塵性の高い内装材の選定
- 役割:微粒子の発生や付着を抑制。
- 重要性:素材選定により発塵源を根本から排除でき、洗浄にも耐えられる必要がある。
- 陽圧設計
- 役割:室内の気圧を高め、外気の流入を防止。
- 重要性:気圧差で清浄区域の保護を実現。設計ミスがあれば外部汚染が侵入する恐れがある。
- 温湿度と静電気の管理
- 役割:粒子の浮遊性と静電気による粒子吸着を防ぐ。
- 重要性:作業者の快適性と静電対策を両立するためにも適切な制御が必要。
- 気密性の高い構造とパーティション(二重ドア構造含む)
- 役割:外部からの空気の侵入を防ぐ。
- 重要性:二重ドア(エアロック)構造により、外部との気圧差を保ち、ドアの開閉による粒子侵入を抑制。気密性が不足すると全体の清浄度に悪影響を及ぼす。
設計時に重視すべきポイントとその解説
- ゾーニングの明確化:クリーンルーム内を清浄度の異なるエリアに分け、それぞれの用途に応じた管理を行うことで、コストと効率の最適化が可能になります。高清浄エリアには高性能フィルターや層流方式を、一般清浄エリアには乱流方式や標準的な素材を使用するなど、用途に応じた最適な配分が重要です。
- メンテナンス性の確保:フィルター交換や清掃、設備の点検がスムーズに行えるよう、設計段階から配慮する必要があります。天井裏のアクセスパネル設置、可動式配線ルート、視認性の高いインジケーターなどを採用することで、日常の運用効率が向上します。
- 人と物の動線の分離:作業者の移動と製品・材料の流れを明確に分離し、交差汚染のリスクを最小限に抑える設計が重要です。人用には更衣室・エアシャワー・専用廊下を、物品用にはパスボックスやエアロック付き搬入ルートを設けるのが理想です。
- 照明の選定と配置:クリーンルーム内の照明は、作業性と清掃性の両立が求められます。LED照明の採用により発熱を抑え、天井埋込型にすることでホコリのたまりやすい凹凸を排除します。色温度や照度も用途に応じて適正値を設定することが推奨されます。
- 清掃性を意識した設計:床や壁の接合部に曲面やコーキング処理を施し、清掃の死角をなくすことで、日常のメンテナンスが容易になります。備品の移動性、清掃用具の収納スペースの確保など、運用後の清掃効率も含めて設計することが重要です。
これらの構造的要素や設備、設計の工夫を総合的に取り入れることで、クリーンルームは高い性能を発揮し、製造工程の信頼性や製品の品質向上に大きく貢献します。とくに異物混入のリスクを厳しく管理しなければならない産業においては、こうした高度な設計が求められるのです。
クリーンルームの作り方と必要設備
まず、クリーンルームの作り方には、大きく分けて「常設型」と「簡易型」の2種類があります。どちらを選択するかは、使用する目的や期間、作業内容の性質によって異なります。
例えば、展示会や実験などで短期間のみ使用する場合であれば、コストや設置期間の面で有利な簡易型でも十分対応可能です。しかし、製造工程で日常的に使用したり、長期間運用する予定がある場合には、耐久性と清浄度の安定性に優れた常設型が適しています。
常設型は構造がしっかりしており、空気の流れやフィルター設置の自由度も高いため、より高度な管理が可能となります。
常設型クリーンルームに必要な主な設備と役割
- 空調システム(AHU:Air Handling Unit):温湿度管理と粒子除去を同時に行い、安定した室内環境を実現します。クリーン度の高い現場では必須です。
- HEPA/ULPAフィルター:微粒子の侵入を防ぐための高性能フィルター。クラスによって使い分け、ISOクラス5以下ではULPAの使用も。
- エアシャワー・パスボックス:人や物品に付着したチリを取り除き、外部からの異物混入を防ぎます。
- 二重ドア構造(エアロック):圧力差を維持しながら、人の出入りによる汚染リスクを最小限に抑える構造です。
- 恒久的内装材(パネル・床材など):防塵性、耐薬品性に優れ、清掃しやすく、耐久性も高い素材が使用されます。
- モニタリングシステム:室内の粒子濃度・気圧・温湿度をリアルタイムで監視し、異常を即時検知します。
簡易型クリーンルームに必要な主な設備と役割
- 簡易ブース(ビニールカーテン・アルミフレーム):設置と撤去が容易で、コストを抑えられます。展示会や短期使用に適しています。
- ファンフィルターユニット(FFU):HEPAフィルター付きの送風機で、清浄空気を局所的に供給します。常設型ほどの精度はありません。
- ポータブル陽圧機器:部屋全体を陽圧化し、外気の侵入を防止します。シンプルな構造で操作も簡単です。
- 簡易温湿度センサー:必要最小限の環境測定が可能です。データロガー型の持ち運び可能な機器が多く使われます。
- 床マット・粘着シート:靴底のホコリを除去し、クリーンルーム内への粒子持ち込みを抑えます。
<常設型と簡易型の比較表>
比較項目 | 常設型クリーンルーム | 簡易型クリーンルーム |
---|---|---|
運用期間 | 長期(常時使用) | 短期(イベント・試作など) |
構造 | パネル・高気密構造 | ビニール・簡易構造 |
清浄度対応 | ISOクラス1〜8対応可 | ISOクラス7〜9が主流 |
主な設備 | AHU・HEPA・エアシャワーなど | FFU・ビニールカーテン・陽圧装置など |
初期費用 | 高い(数百万円〜) | 安価(数十万円〜) |
拡張性 | 高い(自由設計可) | 限定的(モジュール式) |
モニタリング | 自動制御システム付き | 手動または簡易機器 |
このように、クリーンルームの方式と設備選定は、目的やコスト、求められる性能に応じて最適な組み合わせを検討することが重要です。特に精密機器や医薬品の製造など、高い清浄度が求められる用途では、常設型の導入が不可欠となります。逆に、短期使用や限定的な用途では簡易型が効率的な選択肢となります。
クリーンルーム服装と入室手順の基本
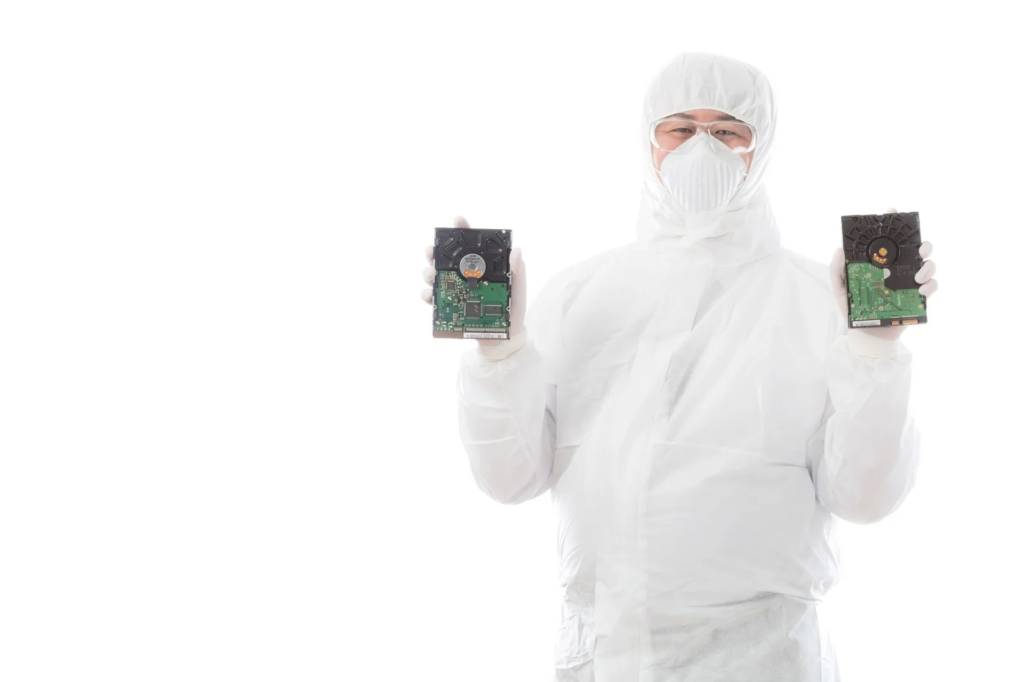
クリーンルームにおける最大の汚染源は、作業者自身の体や衣類から発生する微粒子です。これらは非常に小さく、肉眼では見えませんが、製品の品質や安全性に大きな影響を及ぼします。そのため、適切な服装と正しい入室手順の徹底は、清浄度維持のために不可欠です。
クリーンルームでの服装の基本構成と役割
各アイテムには明確な目的があり、すべてを正しく着用することで初めて効果を発揮します。
- クリーンスーツ(つなぎ型または上下型)
・体全体を覆うことで衣類や皮膚からの微粒子発生を防止。
・ポリエステル系の低発塵素材が用いられ、静電気対策も施されている。 - ヘアキャップ(頭髪カバー)
・髪の毛の落下やフケの飛散を防ぐ。
・耳までしっかり覆えるタイプが望ましい。 - フェイスマスク
・呼気に含まれる飛沫・皮膚片の拡散を防ぐ。
・不織布製で鼻やあごまで密着させる。 - 手袋(ニトリルやラテックス製)
・皮膚から出る油分や角質の汚染を防ぐ。
・着用時に破損がないか、必ず確認する。 - クリーンシューズ(専用靴)
・外履きからの塵・汚れを持ち込まないための専用履き物。
・滑りにくく、洗浄しやすい素材が使用されている。 - インナーや靴下類
・コットン素材など低発塵の衣類を着用し、静電気の発生を抑える。
・派手な衣類や毛羽立ちやすい繊維は避ける。
クリーンルーム入室手順
入室には厳格なルールがあり、すべての手順を順守することで清浄度が確保されます。
STEP 1:更衣室での私物整理と洗手
・私物や装飾品をすべて外し、ロッカーに収納。
・ハンドソープでしっかり手洗い、必要に応じてアルコール消毒。
STEP 2:インナー着用と下衣装の確認
・低発塵インナーを着用。
・毛羽立ちやすい素材の衣類は避ける。
STEP 3:クリーンウェア装着
・順番は「ヘアキャップ → マスク → 上着 → 下着(ズボン) → 手袋 → クリーンシューズ」。
・シワや隙間ができないよう丁寧に装着。
STEP 4:エアシャワー通過
・指定された姿勢で約10〜20秒、全身に風を浴びて表面の異物を除去。
・動かずに回転するか、軽く回るように指示される場合もある。
STEP 5:入室
・静かに扉を開閉し、できるだけ動作を最小限に。
・ドアの開閉中は他者の出入りと重ならないよう注意する。
STEP 6:入室後の行動管理
・不用意な動き・接触を避ける。
・清掃が必要な場合は指定された手順と用具を使用する。
このように、クリーンルームの服装や入室手順には、それぞれ明確な目的があります。特に、クリーンスーツやエアシャワーの役割を正しく理解し、すべての手順を丁寧に実施することが、異物混入の防止と製品品質の確保につながります。
クリーンルーム湿度管理と空気清浄の要点
ただし、清浄度だけでなく湿度の管理も忘れてはいけません。湿度が高すぎるとカビが発生しやすくなり、製品や設備に悪影響を与える可能性があります。一方で、湿度が低すぎると静電気が発生しやすくなり、電子機器や精密機器の故障や品質劣化を引き起こすおそれがあります。
このため、クリーンルームでは一般的に40~60%の範囲に湿度を維持することが望ましいとされており、この環境を保つことで作業の安定性と安全性が確保されます。さらに、作業者の快適性も考慮され、長時間の作業にも適した条件が整えられるよう工夫されています。
空気清浄については、HEPAフィルターや空調設備によって、常に外部からの汚染物質を効率的に除去する必要があります。これにより、室内の環境が安定し、製品の品質を維持するうえでの信頼性が高まります。あわせて、清浄な空気環境は作業者の健康を守る点でも非常に重要です。
エアシャワーやグレーチングの役割
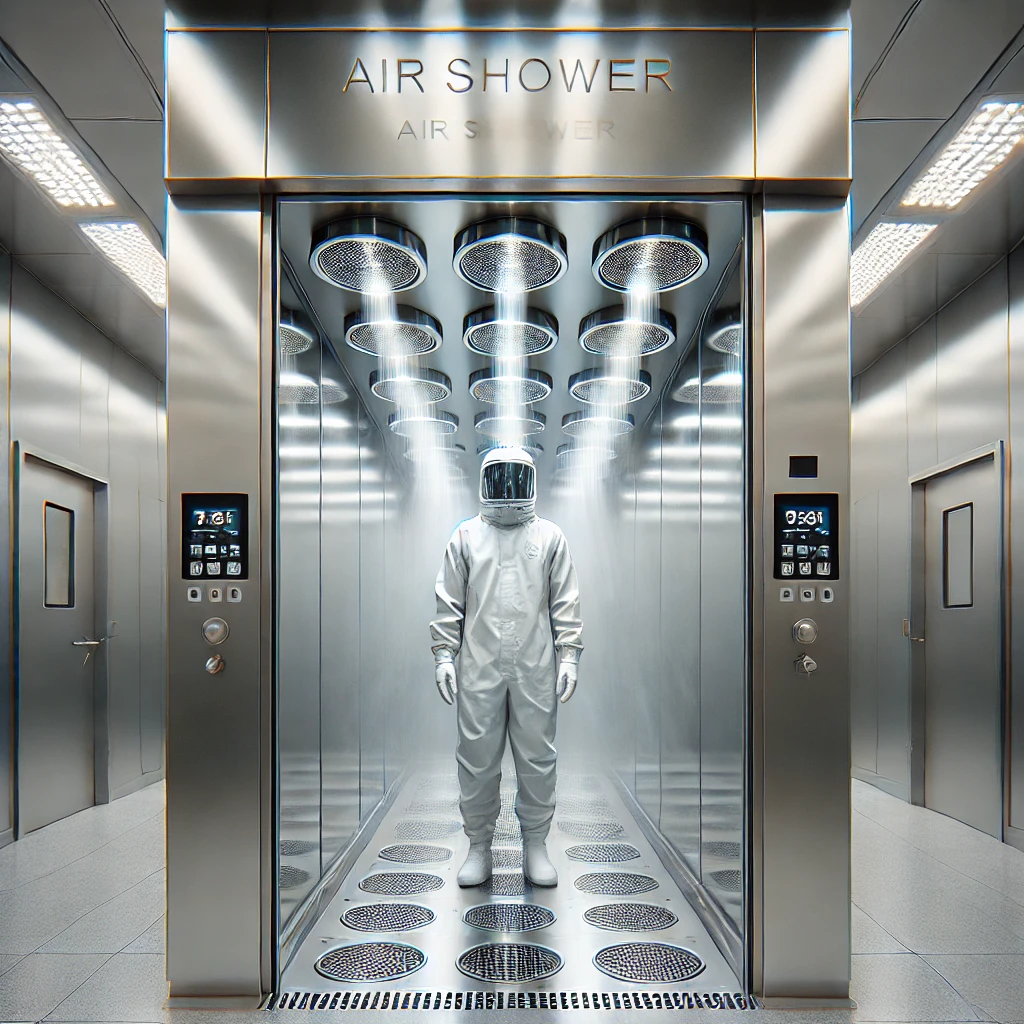
ここでは、クリーンルームへの入室時に使用する代表的な設備について、より詳しく解説します。
まず、エアシャワーは人や物品に付着した塵やホコリを高圧の空気で吹き飛ばす装置であり、作業者や搬入物が室内に入る前に強制的に微粒子を除去します。これにより、クリーンルーム内への異物の侵入を防ぎ、清浄度の維持に大きく貢献します。特に髪の毛、衣類の繊維、表面のホコリなど、目に見えにくい汚染物の除去に有効です。
一方、グレーチングは床面に格子状に設置され、靴底の汚れをその下に落とす構造を持ちます。これにより、足元からの粒子の持ち込みを最小限に抑えることができ、さらに空気の流れを下部まで効率よく届けることで、室内の気流バランスを整える効果も期待されます。
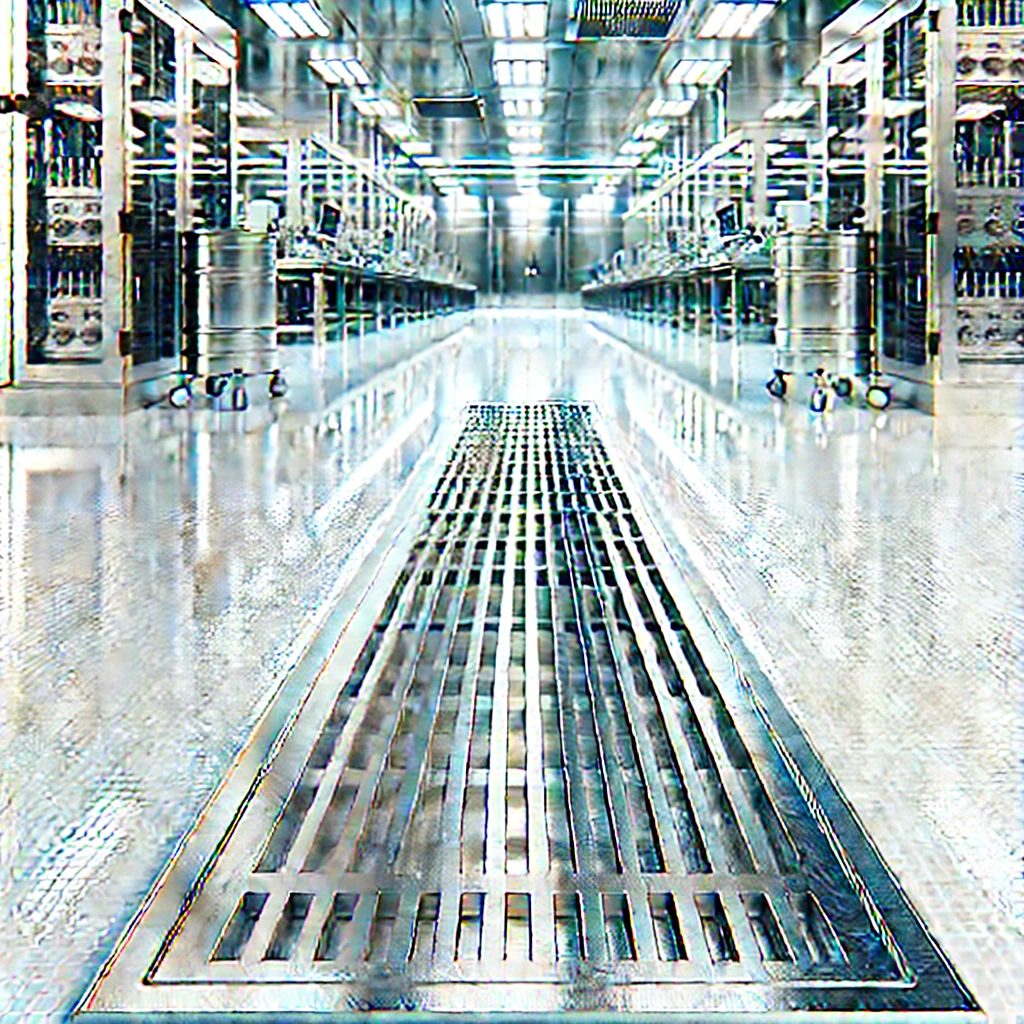
【重要なポイント】
- エアシャワーは適切な風速と使用時間が設定されていなければ効果を発揮できません。最低でも15~20秒間のエアシャワー滞在が推奨されます。
- グレーチングは常に清掃状態を保つ必要があります。蓄積されたゴミやホコリは逆に汚染源となり得ます。
- 両設備は定期的な点検・メンテナンスを行うことで、安定した性能を発揮し続けます。
【注意すべき点】
- グレーチングの上を通過する際、振動やわずかな揺れが発生します。特に台車で製品を搬送する場合、安定性が損なわれる恐れがあるため、精密機器(例:カメラやレンズ)の移動には十分な配慮が必要です。
- 振動吸収マットを併用する
- 台車の緩衝機能を確認する
- グレーチングの設置場所を避ける搬送ルートの設計などが有効です。
- 作業者がグレーチングの隙間に靴のヒールや車輪が引っかかることもあるため、靴底の形状や台車の車輪サイズにも注意が必要です。
これらの設備は、見た目にはシンプルでも、クリーンルームの清浄環境を守る上で非常に重要な役割を果たしており、その適切な設計・運用が製品の品質と信頼性を左右する要素となります。
クリーンルームライトと掃除機の選び方
例えば、クリーンルーム用ライトは発塵しにくい素材と構造で作られており、明るさも一定の基準を満たす必要があります。照明器具の発塵や静電気の発生を防ぐ設計になっており、これによって室内の空気清浄度が安定します。また、視認性の高い照明を使うことで、作業者の疲労を軽減し、作業効率の向上にもつながります。
掃除機についても、家庭用の一般的なものではなく、HEPAフィルターやULPAフィルターを搭載した専用タイプが求められます。これにより、清掃作業中に細かい粒子が再び空気中に放出されるのを防ぎ、清浄度を高いレベルで維持することが可能です。また、清掃ノズルやホース部分も帯電防止処理がされており、静電気による粒子の吸着を防ぐ工夫が施されています。
このように、日常的な清掃や照明においても、クリーンルームでは通常とは異なる厳格な基準が設けられており、細かい配慮が求められるのが大きな特徴です。作業環境を常に最適な状態に保つためには、こうした設備選定にも十分な注意と理解が必要です。
クリーンルームクラス10000とはどのような環境かを理解するための総括
本記事のまとめを以下に列記します。
- クリーンルームクラス10000は、0.5μm以上の粒子が1立方フィート中に最大10,000個まで許容される環境
- 電子部品や医療機器などの一般的な組立工程に多く採用されている
- FED-STD-209Eの規格に基づく基準で、現在はISO規格とも併用されている
- ISO規格ではおおむねISOクラス7に相当する清浄度レベル
- 半導体やバイオ分野ほどの厳密な清浄度は求められない現場に適している
- 空調管理や気圧制御によって外気の侵入を防ぐ設計が求められる
- HEPAフィルターによって空気中の粒子除去を行う
- 乱流方式の空気循環が多く採用されている
- 層流方式との併用で清浄度を高める混合型の導入例もある
- エアシャワーや二重ドア構造で作業者・物品由来の汚染を抑制する
- カメラやレンズなど光学機器の最終工程には不十分な場合もある
- イメージセンサーなど微細な構造を扱う工程ではクラス1000以上が必要
- クラス100000に比べて10倍高い清浄度を持つ中間グレードとして位置づけられる
- コストと清浄度のバランスがよく、汎用的な用途に向いている
- クリーンルーム運用時には清掃やメンテナンスの頻度・方法も管理要件に含まれる
コメント