製品やプロセスのリスク管理において、FMEA(Failure Mode and Effects Analysis)は欠かせない手法です。しかし、「FMEA やり方」を検索しても、DFMEAやPFMEAの違いや具体的な手順が曖昧で、戸惑う方も多いでしょう。
本記事では、「FMEAとは」の基本から「DFMEA やり方」「PFMEA やり方」などの具体的な手法、さらには「FMEAの5段階とは?」といった重要ポイントまで丁寧に解説します。
また、「FMEA 意味ない」と感じさせないために、実際の「DFMEA 例」や「工程FMEA 故障モード一覧表」など、実務で役立つ内容も取り上げます。
さらに、「FMEA 分析」や「FMEA 点数」をどう活用すべきか、「FMEAフォーマット」の選び方や「FMEAは誰が作るのですか?」といった疑問にもお答えします。
最後に、「FTAとFMEAのどちらがよいですか?」という比較にも触れ、あなたの課題に最適な手法を選ぶためのヒントをお届けします。
初心者でもわかりやすく実践しやすい解説を心がけた本記事を、ぜひ参考にしてください。
- FMEAの基本的な概念と目的について理解できる
- DFMEAとPFMEAの違いや活用方法を理解できる
- FMEAの具体的な手順と実践方法を理解できる
- リスク評価の重要性とスコアリング方法を理解できる
FMEA やり方を徹底解説!初心者でもわかる基本
FMEA(Failure Mode and Effects Analysis)は、製品やプロセスの設計段階から潜在的な問題やリスクを洗い出し、それらがもたらす影響を評価して未然に対策を講じるための手法です。
この分析は、品質や安全性を向上させるだけでなく、修正や回収コストの削減にもつながります。FMEAには、設計段階で用いるDFMEAと製造工程に特化したPFMEAがあり、それぞれ異なる観点からリスクを管理します。
例えば、カメラの設計では、DFMEAがシャッターの耐久性や部品選定の問題を特定し、PFMEAが組立工程でのヒューマンエラーや機械不良を防止します。これらを適切に組み合わせることで、製品の信頼性と工程の安定性を高め、顧客満足度を向上させることが可能です。
FMEAは、設計者、品質管理者、製造担当者などチーム全体で取り組むべき手法であり、多角的な視点が成功の鍵となります。
FMEAとは何か?目的とメリットを解説
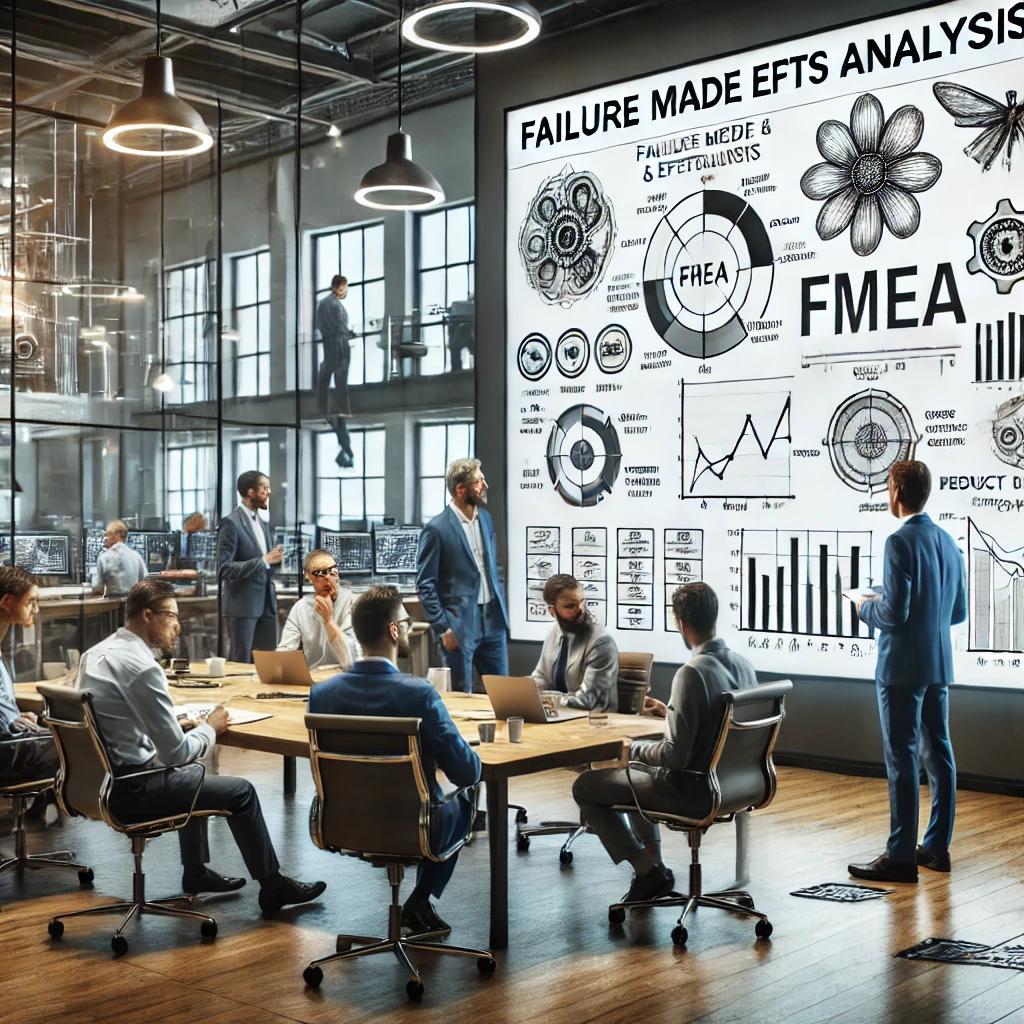
FMEA(Failure Mode and Effects Analysis)は、製品やプロセスに潜む潜在的な問題やリスクを特定し、それがもたらす影響を評価する手法です。設計や製造において品質や安全性を向上させる目的で使用されます。この手法は、主に以下の目的とメリットがあります。
目的としては、主に以下の2つがあります。
- 潜在的なリスクの予測と回避:問題が実際に発生する前にリスクを洗い出し、対策を講じます。
- コスト削減:不具合の早期発見により、修正や回収にかかる費用を大幅に削減します。
一方で、メリットには次のようなものがあります。
- 製品やプロセスの信頼性向上:問題の発生頻度を下げることで、顧客満足度が向上します。
- チームのコミュニケーション向上:関係者間でリスクを共有し、解決策を協議するため、部門間の連携が強化されます。
FMEAは、製造業やサービス業などさまざまな分野で活用されています。
DFMEA と PFMEAの違いを知ろう
DFMEA(Design Failure Mode and Effects Analysis)とPFMEA(Process Failure Mode and Effects Analysis)は、FMEAを適用する場面の違いによって分けられます。それぞれの特徴を以下にまとめます。
- DFMEAは、製品や部品の設計段階で使用します。設計上の問題を見つけ出し、製品の機能や安全性を確保するための分析が目的です。
- 例:部品の材質選定のミスが耐久性に影響する場合。
- PFMEAは、製造工程の分析に用います。プロセス内で発生する可能性のある問題を特定し、製造中の不具合を防止することが目的です。
- 例:組み立て工程で発生するヒューマンエラーや機械の故障リスク。
これらの違いを理解することで、適切なタイミングで適切な手法を選択できるようになります。
DFMEAとPFMEAの比較表
項目 | DFMEA (設計FMEA) | PFMEA (工程FMEA) | 備考 |
---|---|---|---|
分析対象 | 製品や部品の設計 | 製造工程や作業プロセス | DFMEAの内容を元に、PFMEAで製造工程への影響を考慮することが可能。 |
主な目的 | 設計段階での潜在的な問題の特定と予防 | 製造工程での潜在的な問題の特定と予防 | 両者を組み合わせると、製品全体のリスク管理が効果的に行える。 |
適用時期 | 設計初期段階、試作前 | 製造開始前、新工程導入時 | DFMEAを先行させ、PFMEAでフォローアップすると効果的。 |
対象者 | 設計者、開発エンジニア | 製造エンジニア、品質管理チーム | チーム間の連携が重要。特に工程変更時にはDFMEAの情報を活用する。 |
分析手法 | 機能ごとに故障モードを分析 | 工程ごとに潜在的な失敗モードを分析 | 分析手法のフレームワークは類似しているが、視点が異なる。 |
例 | 強度不足、誤差範囲外の寸法 | 加工不良、組立ミス | DFMEAで設計のリスクを洗い出し、そのリスクが工程に与える影響をPFMEAで検討する。 |
スコアリング | 重大性、発生確率、検出可能性 | 重大性、発生確率、検出可能性 | スコアリング方法は共通で、結果を比較することで全体的な優先順位を付けられる。 |
アウトプット | 設計仕様の変更、改善提案 | 工程手順の変更、工程改善計画 | DFMEAのアウトプットがPFMEAのインプットになる場合が多い。 |
注意点 | 設計変更のコストや影響を考慮する | 工程改善のコストや実現可能性を考慮する | DFMEAでの見落としがあると、PFMEAでの対策が困難になる場合がある。 |
ソフトウェアの活用 | CAD連携ツール、設計支援ツール | 生産管理ソフト、工程管理ツール | 両者で一貫したデータ管理を行うと、分析の効率が向上する。 |
組み合わせ方法 | – | – | DFMEAで設計リスクを洗い出した後、そのリスクを元にPFMEAで製造リスクを具体化する。 |
DFMEAの内容をPFMEAに盛り込む方法
DFMEAの結果は、PFMEAでの分析に直接役立ちます。以下の方法でPFMEAに反映させます。
- 設計リスクを製造リスクに翻訳する
DFMEAで洗い出した設計上のリスク(例えば、寸法誤差が大きい部品)は、製造工程における加工や組立の問題としてPFMEAに取り入れる。 - 設計仕様を工程での重要管理項目にする
DFMEAで重要とされた設計仕様(例えば、強度や精度)は、PFMEAにおいて「重要管理項目」として工程内でのチェック対象に設定する。 - 設計変更が工程に与える影響を評価する
DFMEAで提案された設計変更が製造工程に与える影響(例えば、新しい材料の加工性)はPFMEAで評価し、必要な改善策を検討する。 - リスク管理の一貫性を保つ
DFMEAとPFMEAの分析結果を一つのデータベースで管理することで、設計から製造までのリスク管理を統合的に行える。
選び方のポイント
- 製品の設計が安定していない場合は、DFMEAを優先する。
- 新しい製造工程の立ち上げ時や既存工程の見直しが必要な場合は、PFMEAを実施する。
- 製品開発全体をカバーするには、DFMEAを先に実施し、続けてPFMEAで工程リスクを管理する。
このように、DFMEAとPFMEAの違いを理解しつつ、適切に組み合わせることで、製品の品質と工程の安定性を高めることができます。
初心者必見!FMEAの作業手順とは
FMEAの作業手順を具体例として「カメラの設計」に適用し、わかりやすく解説します。これにより、各プロセスがどのように実践されるのかを理解できます。
1. 分析対象を明確化する
具体例(カメラの設計):
カメラ全体ではなく、今回は「シャッター機構」に焦点を当てます。対象範囲を狭めることで、分析の精度を高められます。シャッターの開閉速度や耐久性など、製品性能に直結する部分を分析対象として設定します。
2. 潜在的な問題を洗い出す
具体例(カメラの設計):
シャッター機構の潜在的な問題を洗い出します。
- シャッターが開かない
- 開閉速度が設計通りにならない
- 部品が摩耗して寿命が短くなる
- 高湿度環境で動作が不安定になる
これらの「故障モード」をリストアップします。
3. 影響を評価する
具体例(カメラの設計):
故障モードが発生した場合の影響を評価します。例えば:
- シャッターが開かない:写真が撮れず、顧客の信頼が損なわれる
- 開閉速度が遅い:動きの速い被写体が撮影できず、製品の競争力が低下する
- 部品の摩耗:製品寿命が短くなり、修理コストが増加する
これらの影響を、重大性(Severity)、発生確率(Occurrence)、検出可能性(Detection)で数値化します。
4. 原因を特定する
具体例(カメラの設計):
それぞれの故障モードに対して、発生原因を特定します。例えば:
- シャッターが開かない → モーターのトルク不足が原因
- 開閉速度が遅い → 部品の材質選定ミスによる摩擦増加
- 部品が摩耗する → 潤滑不足または使用頻度の誤算
これらの原因を具体的に掘り下げることで、より実効性の高い対策を講じる準備が整います。
5. 対策を決定し実施する
具体例(カメラの設計):
特定された原因に基づいて、具体的な対策を決定します。例えば:
- モーターのトルク不足 → 高トルクモーターに変更
- 部品の材質選定ミス → 摩擦係数の低い材質に再設計
- 潤滑不足 → 自動潤滑機能を追加
これらの対策を実行し、その効果をテストで確認します。必要に応じてFMEAを更新し、継続的な改善を行います。
カメラの設計にFMEAを適用することで、製品品質を高める具体的な手法が明確になります。このように分析対象を具体化し、潜在的な問題から解決策までを一貫して検討することで、FMEAを効果的に活用できます。
FMEAは誰が担当すべき?役割と責任を解説
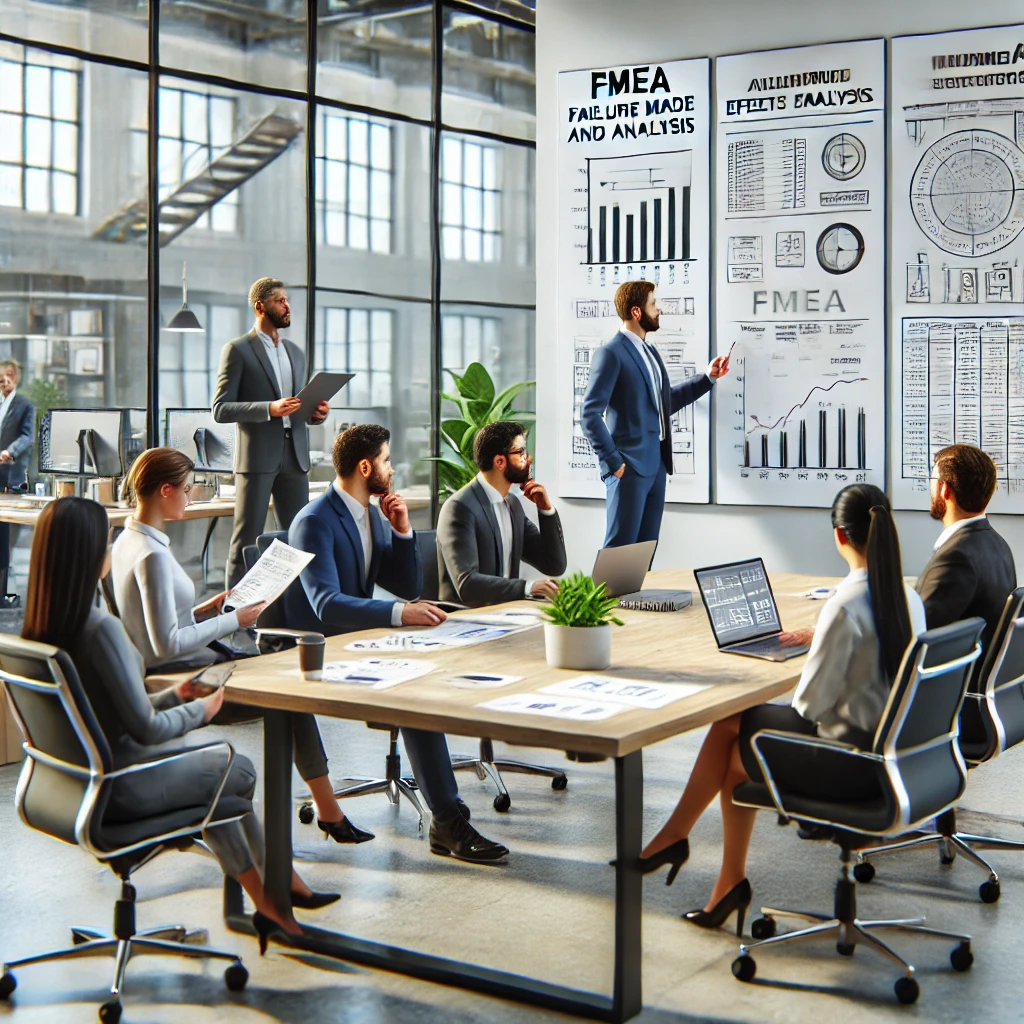
FMEAは、個人ではなくチームで進めるべき分析手法です。それぞれの役割と責任を以下に整理します。
- プロジェクトリーダー
分析を主導し、進行状況を管理します。全体のスケジュール調整も担当します。 - 設計者やエンジニア
製品や工程に関する専門知識を提供し、潜在的な問題を洗い出します。 - 品質管理担当者
リスク評価における数値化や、改善案の実効性を評価します。 - 製造担当者
工程の現場視点で、発生しうるリスクを共有します。
FMEAは、これらの多角的な視点を結集して進めることで、より精度の高い分析が可能になります。
FMEA やり方を具体例でわかりやすく説明!
DFMEA(Design Failure Mode and Effects Analysis)は、製品設計の段階で潜在的な問題を洗い出し、それらが引き起こす影響を分析して未然にリスクを低減する手法です。
本記事では、DFMEAやPFMEAの手順をステップごとに解説し、具体例を交えながら、初めての方でも実践しやすいように紹介します。
例えば、カメラ設計の場合、シャッターやレンズの耐久性、精度不足などのリスクを事前に特定し、それに応じた改善策を講じることで、高品質な製品を実現します。
このプロセスは、顧客満足度の向上や設計段階でのコスト削減にも寄与します。DFMEAを効率よく進めるためのポイントや、結果を最大化する方法をこの記事で詳しく説明します。
DFMEA やり方をステップごとに解説
DFMEA(Design Failure Mode and Effects Analysis)のやり方は、以下のステップで進めると効果的です。
- 分析対象を明確化する
製品設計のどの部分を対象とするかを特定します。対象が曖昧だと、リスクの見落としにつながる可能性があります。 - 機能と故障モードを洗い出す
製品の機能ごとに、「どのような故障が発生するか」をリストアップします。例えば、「強度不足で破損する」などが挙げられます。 - 影響を評価する
故障モードが発生した場合の影響を、顧客や安全性の観点から分析します。重大性や発生確率、検出可能性をスコア化して優先順位を付けます。 - 原因を分析する
故障モードが発生する根本原因を追求します。設計上のミスや材料選定の不適切さが原因になることが多いです。 - 対策を検討し実行する
リスクを低減するための設計変更や補強案を検討します。優先度の高いリスクから対応するのが基本です。 - 結果をフォローアップする
対策が適切に実行され、問題が解決されたかを確認します。必要に応じて再評価を行います。
このステップを丁寧に行うことで、DFMEAの効果を最大化できます。
DFMEA 例を使った実践的な理解
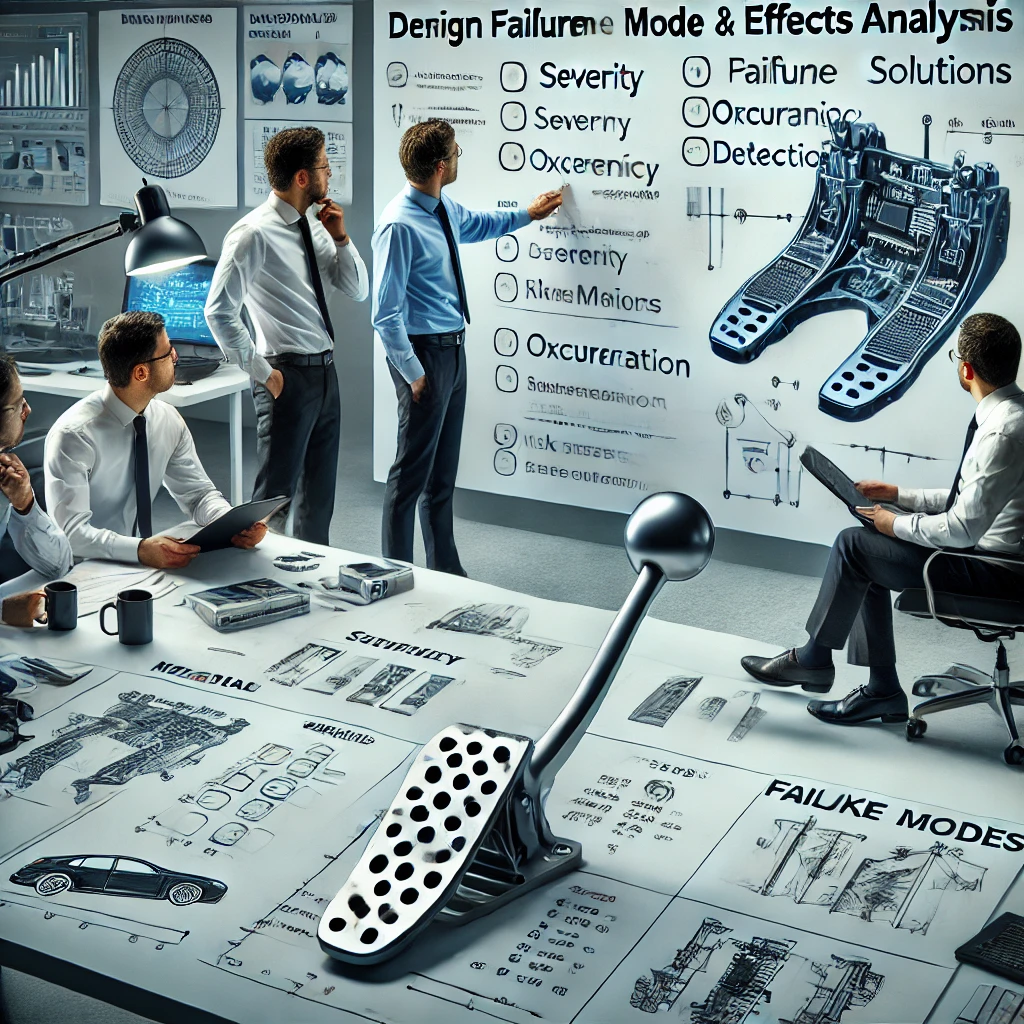
DFMEAを実践的に理解するためには、具体的な例を挙げることが重要です。以下は自動車部品を例にした分析です。
対象部品:ブレーキペダル
- 機能の特定
ブレーキペダルの主な機能は、ドライバーの操作力をブレーキシステムに伝えることです。 - 故障モードの特定
- ペダルの折損
- 操作力が正常に伝達されない
- ペダルが戻らない
- 影響の評価
- 重大性:ペダル折損は重大な事故につながるため、スコアは高い。
- 発生確率:材質や設計によるが、適切な設計で低減可能。
- 検出可能性:製造工程での検査が必要。
- 原因の特定
- 不適切な材料選定
- 設計強度の不足
- 製造工程での欠陥
- 対策の検討
- 高強度の材料を採用する。
- 強度計算の見直しを行う。
- 製造工程での検査を強化する。
このような具体例を通じて、DFMEAの活用方法を理解できます。
PFMEA やり方の基本と応用テクニック
PFMEA(Process Failure Mode and Effects Analysis)は、製造プロセスに焦点を当てた分析手法です。以下にやり方の基本と応用テクニックを紹介します。
基本のやり方
- 工程の洗い出し
製造プロセス全体をフローチャート化し、各工程を明確にします。 - 潜在的な問題の特定
各工程ごとに、発生し得る問題(故障モード)をリストアップします。例えば、溶接工程での接合不良などです。 - リスクの評価
故障モードごとに、影響の重大性、発生確率、検出可能性を評価し、リスク優先度を設定します。 - 対策の立案
リスクを低減するための工程改善や機械の調整を提案します。 - フォローアップ
改善後の結果を確認し、リスクが低減されたかを評価します。
応用テクニック
- クロスファンクショナルチームの活用
各部門から専門知識を持つメンバーを集め、多角的に分析することでリスクの見落としを防ぎます。 - 継続的なモニタリング
一度完了したPFMEAを定期的に見直し、新たなリスクやプロセス変更に対応します。
これにより、PFMEAをより効果的に活用できます。
PFMEA 具体例
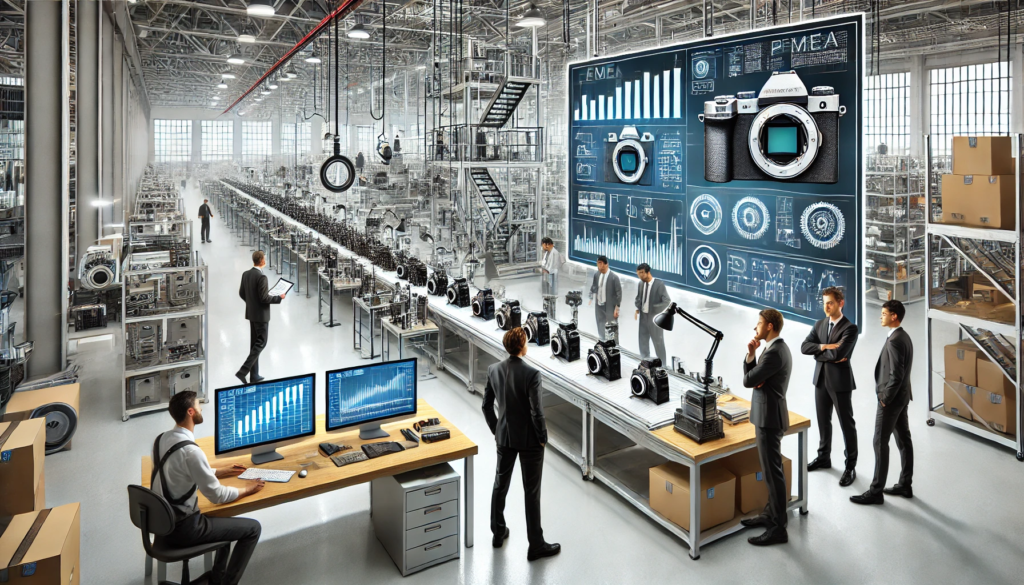
PFMEA(Process Failure Mode and Effects Analysis)は、製造工程で発生する可能性のある問題を予測し、事前に対策を講じる手法です。ここでは、カメラの製造プロセスにおける具体例を交えて、PFMEAの基本的なやり方と応用テクニックを解説します。
1. 工程の洗い出し
具体例(カメラの製造):
カメラの製造工程には、組み立て、検査、塗装、パーツの取り付け、などがあります。これらをフローチャートとして可視化し、どの工程で何が行われるのかを明確にします。例えば、カメラのボディとレンズの組み立て工程を洗い出し、その順番を確認します。
この工程の洗い出しが最初のステップであり、製造の流れを理解するための基盤となります。
2. 潜在的な問題の特定
具体例(カメラの製造):
各工程ごとに発生する可能性のある故障モード(問題)をリストアップします。カメラの製造工程で考えられる問題として、次のようなものがあります。
- 組み立て工程: ボディとレンズの接続部分が緩む。
- 検査工程: カメラの画像センサーに不具合があり、撮影時に画像がぼやける。
- 塗装工程: カメラの外装に傷や塗装のムラが発生する。
- パーツ取り付け工程: 部品が誤って取り付けられる(例: バッテリーが正しく取り付けられていない)。
これらの潜在的な問題(故障モード)をリストアップすることが重要です。
3. リスクの評価
具体例(カメラの製造):
リスクを評価するために、各故障モードについて、影響の重大性、発生確率、検出可能性を評価します。カメラ製造の例では次のように評価します。
- ボディとレンズの接続部分が緩む:
- 重大性(Severity): 8(カメラ使用中にズレが生じ、顧客の不満を引き起こす)
- 発生確率(Occurrence): 4(接続部分に不具合が発生する可能性が高い)
- 検出可能性(Detection): 5(出荷前の検査で簡単に発見できる)
このように各項目をスコア化し、リスク優先度を計算します。優先度が高い項目は優先的に対策を講じます。
4. 対策の立案
具体例(カメラの製造):
リスクを低減するために、改善策を提案します。例えば、次のような対策が考えられます。
- ボディとレンズの接続部分が緩む問題 → 接続部分にロック機構を追加し、手動での緩みを防止。
- 画像センサーの不具合 → センサーの検査工程を強化し、出荷前に多角的なチェックを行う。
- 塗装ムラの問題 → 塗装前の表面処理工程を改良し、塗装機の温度や湿度管理を徹底。
- 部品取り付けミス → 自動化された機械での部品取り付けを導入し、人為的ミスを減らす。
これらの対策を具体的に実行し、リスクを低減させる方法を明確にします。
5. フォローアップ
具体例(カメラの製造):
対策が実行された後は、改善が有効であったかを確認するため、工程をモニタリングします。例えば、新しい組み立てラインでのボディとレンズの接続確認作業を定期的にチェックし、再発防止策が適切に機能しているかを確認します。
また、製造ラインの変更後や新しい部品が導入された際に再評価を行い、新たなリスクが生じていないかを確認します。
応用テクニック
クロスファンクショナルチームの活用
具体例(カメラの製造):
カメラの製造には設計、製造、品質管理、調達など多くの部門が関与します。これらの部門の専門家が集まってチームを組み、PFMEAを行うことで、リスクの見落としを防ぎます。例えば、製造担当者が組み立て工程で発生する問題について、設計担当者と一緒に対策を検討することで、より多角的な視点で問題解決が進みます。
継続的なモニタリング
具体例(カメラの製造):
一度実施したPFMEAは終わりではなく、製造が進むにつれて定期的に見直し、新たなリスクに対応します。例えば、カメラの製造プロセスに新しい部品が導入された場合、その部品に関連するリスクを再評価し、PFMEAをアップデートします。
これらの基本的なやり方と応用テクニックを組み合わせることで、PFMEAをより効果的に活用し、カメラの製造工程で発生するリスクを最小限に抑えることができます。
FMEAにおける重大性(Severity)、発生確率(Occurrence)、検出可能性(Detection)のスケール解説
FMEAの評価項目である「重大性」「発生確率」「検出可能性」について、1~10のスケールをそれぞれ詳しく説明します。このスケールは、リスク評価をより具体的にするために使われます。
1. 重大性(Severity)のスケール
重大性は、問題が発生した場合に与える影響の大きさを表します。
スコア | 説明 | 例 |
---|---|---|
1 | 影響は軽微で、顧客やシステムにほとんど影響を与えない。 | 製品の外観に小さな擦り傷。 |
2-3 | 影響が小さいが、気づく人はいる可能性がある。 | ボタンの押し心地が不安定。 |
4-6 | 製品の一部の機能が低下するが、安全性には影響しない。 | カメラのシャッター速度が遅れる。 |
7-8 | 製品の主要な機能に重大な影響を与えるが、危険性はない。 | カメラの自動フォーカスが機能しない。 |
9 | 安全性や重要な性能に大きな影響を及ぼし、顧客の不満が高い。 | カメラが動作しなくなる。 |
10 | 安全性に致命的な影響を与える。法律違反や人命に関わる可能性がある。 | 電子機器が火災を引き起こす。 |
2. 発生確率(Occurrence)のスケール
発生確率は、問題がどれくらいの頻度で発生するかを表します。
スコア | 説明 | 例 |
---|---|---|
1 | 発生する可能性はほぼない(非常に稀)。 | 高度な品質管理下で生産される。 |
2-3 | 非常に稀だが、特定の条件下で発生する可能性がある。 | 環境温度が極端な場合にのみ発生。 |
4-5 | 発生する可能性は中程度。製造条件が悪化すると頻度が上がる。 | 材料のロットによりばらつきが出る。 |
6-7 | 発生頻度が高い。製造プロセスや部品選定に問題がある可能性が高い。 | 定期的に部品の故障が見られる。 |
8-9 | 発生する可能性が非常に高い。システムや工程の重大な不具合。 | 製造装置の不具合で高い頻度で発生。 |
10 | 問題が必ず発生する状況。何も対策をしなければ回避できない。 | 未検証の工程や設計変更をそのまま採用。 |
3. 検出可能性(Detection)のスケール
検出可能性は、問題が発生した際にどれだけ早く検出できるかを表します。
スコア | 説明 | 例 |
---|---|---|
1 | 問題はほぼ確実に検出可能。 | 高精度のAI検査装置を使用。 |
2-3 | 検出は簡単だが、まれに見逃す場合がある。 | 検査員が目視確認する工程。 |
4-5 | 問題が検出される可能性は中程度。検査の仕組みが改善の余地あり。 | 不完全な機械検査で見逃しが発生。 |
6-7 | 問題の検出は難しい。検査が不十分または手間がかかる。 | 手動検査に依存している。 |
8-9 | 問題の検出がほぼ不可能。検出システムの設計が大きく不足している。 | 組み立て後の内部故障。 |
10 | 問題の検出が不可能。発生後に顧客や最終工程で初めて気づくレベル。 | 外観や動作で一切判別できない。 |
スコアの掛け合わせと改善対応
3つのスコア(Severity × Occurrence × Detection)を掛け合わせることでリスク優先度指数(RPN: Risk Priority Number)を算出します。
例: カメラのレンズ部品の故障
- 重大性(Severity): 8(焦点が合わないとカメラの主要機能が失われる)
- 発生確率(Occurrence): 6(レンズの取り付け精度にばらつきがある)
- 検出可能性(Detection): 7(検査工程が目視のみで見逃しが多い)
RPN = 8 × 6 × 7 = 336
この場合、RPNが非常に高いため、すぐに改善対応が必要です。具体的には以下の対応が考えられます。
- 重大性に対応: レンズ設計を見直し、取り付けが容易で正確になるよう変更。
- 発生確率に対応: 製造プロセスを改善し、組み立て工程のばらつきを減少。
- 検出可能性に対応: 自動検査装置を導入し、精度を向上。
RPNが高い項目を優先的に改善することで、製品やプロセスの信頼性を向上させることができます。このスケールを正しく使い、適切な対策を実施しましょう。
※重大性は改善できるものではないため、決まったら点数は下がりません。発生確率と検出可能性の点数を下げてRPNの値を100以下になるように対策を進めてください。
使いやすいFMEAフォーマットの選び方
FMEAフォーマットを選ぶ際には、以下のポイントを考慮すると使いやすいものが見つかります。
- シンプルな構造
初心者や関係者全員が理解しやすいフォーマットを選びます。具体例として、Excelやテンプレートソフトがあります。 - 必要な項目が網羅されている
重要な項目(故障モード、影響、原因、リスク優先度など)が漏れなく含まれていることが重要です。 - 編集のしやすさ
フォーマットが柔軟で、プロジェクトごとにカスタマイズ可能なものを選びましょう。 - チームで共有しやすい
クラウド対応のソフトウェアやオンラインツールを使用すると、関係者間での情報共有がスムーズです。
使いやすいフォーマットを選ぶことで、FMEA作業が効率的に進みます。
以下は、カメラ設計を例にしたFMEAフォーマットのサンプルです。設計段階におけるカメラ部品の故障モードを洗い出し、リスクを評価し、対策を立案するためのフォーマットです。
FMEAフォーマット(カメラ設計例)
項目 | 内容 |
---|---|
プロジェクト名 | デジタルカメラ新製品設計 |
分析対象 | レンズユニット、センサー、電源回路 |
作成日 | YYYY/MM/DD |
作成者 | 開発チーム |
設計要素 | 機能 | 故障モード | 影響 | 重大性 (S) | 原因 | 発生確率 (O) | 現行管理方法 | 検出可能性 (D) | リスク優先度 (RPN) | 対策案 | 担当者 | 期限 |
---|---|---|---|---|---|---|---|---|---|---|---|---|
レンズユニット | 画像の正確なフォーカスを維持 | 焦点がずれる | 画像がぼやけて顧客満足度が低下。 | 8 | 固定部品の設計が不適切 | 7 | 試作品の動作試験 | 6 | 336 | 固定部品の材質を強化する | A氏 | 1週間後 |
イメージセンサー | 光信号を電気信号に変換 | ノイズが発生 | 画像品質が低下し、商品価値が損なわれる。 | 9 | 電磁干渉の遮断が不十分 | 6 | 試験設備でのノイズ測定 | 5 | 270 | ノイズフィルターの追加設計 | B氏 | 2週間後 |
電源回路 | 安定した電源供給 | 電源供給が停止 | カメラが動作しなくなり、重大な顧客クレームにつながる。 | 10 | 配線設計の誤り | 5 | 部品の電気試験 | 4 | 200 | 配線設計を再確認し、冗長化する | C氏 | 3日後 |
シャッター機構 | 正確なシャッター速度を実現 | シャッターが作動しない | 撮影が不可能となり、顧客満足度の低下や返品が発生する。 | 9 | 部品の摩耗や不良 | 5 | 耐久試験 | 3 | 135 | 高耐久性部品への変更 | D氏 | 10日後 |
フォーマットの説明
- 設計要素:
- カメラ設計の対象となる部品やユニット(例:レンズ、センサー、電源回路など)。
- 機能:
- 設計要素が果たすべき役割。
- 故障モード:
- その部品やユニットがどのように故障するか。
- 影響:
- 故障が発生した場合の結果や顧客への影響。
- 重大性 (S):
- 故障が与える影響の深刻度を1~10で評価。
- 原因:
- 故障の根本的な要因。
- 発生確率 (O):
- 故障がどの程度発生しやすいかを1~10で評価。
- 現行管理方法:
- 現在行われている管理方法や検査。
- 検出可能性 (D):
- 故障を発見できる可能性を1~10で評価。
- リスク優先度 (RPN):
- S × O × Dの値。数値が高いほど優先度が高い。
- 対策案:
- RPNを低減するための具体的な改善案。
- 担当者と期限:
- 対策を担当するメンバーと実施期限。
- このフォーマットを使用することで、カメラ設計の潜在的な問題を洗い出し、リスクの高い箇所から優先的に対策を講じることができます。
- 実際の設計チーム内での共有や、改善プロセスのフォローアップに役立ててください。
FTAとFMEAの比較表
以下の比較表では、FTA(Fault Tree Analysis)とFMEA(Failure Mode and Effects Analysis)を、カメラ設計における具体例を交えながら整理しています。それぞれの特徴や利点を理解し、適切な選択をするための参考にしてください。
項目 | FTA (Fault Tree Analysis) | FMEA (Failure Mode and Effects Analysis) |
---|---|---|
手法のアプローチ | トップダウン型:最終的な故障から原因を逆方向に追求する。 | ボトムアップ型:部品や工程ごとに潜在的な問題を洗い出す。 |
分析の目的 | 特定の問題や故障の原因を体系的に特定する。 | 製品やプロセスの潜在的な問題を予防する。 |
活用場面 | 航空宇宙や原子力など、システム全体の安全性が重視される場面。 | 製造業や設計工程、特に新製品の開発や製造ラインの設計時。 |
利点 | – 因果関係が明確に分かる。 | – 問題の予防に特化し、具体的な対策が立てやすい。 |
欠点 | – 分析に時間がかかり、細部が見落とされる可能性がある。 | – 因果関係の全体像を把握するのが難しい場合がある。 |
例:カメラ設計 | – カメラの電源が入らない問題の原因を追求する。 | – レンズのズレや組み立て不良を防ぐための設計改善を検討する。 |
具体例:適用方法 | 1. トップイベント(例:カメラが動作しない)を設定。 | 1. 各部品(例:センサー、シャッター機構)の潜在的な故障を洗い出す。 |
2. イベントツリーを描き、原因(例:配線の不良、基板故障)を追求。 | 2. 故障が与える影響(例:撮影画像がぼやける)を評価。 | |
3. 最も深刻な原因を特定し、重点的に対策を講じる。 | 3. リスクスコアを算出し、優先順位を付けた改善案を実行する。 | |
複雑なリスク管理 | システム全体の安全性が重視される場合に適している。 | 製造・設計工程での予防的アプローチが求められる場合に適している。 |
ツールの組み合わせ | カメラのシステム全体の安全性を分析した後に、詳細部分はFMEAで補完する。 | 各部品や工程の分析を終えた後、全体的な安全性評価にはFTAを使用する。 |
カメラ設計での具体的な活用例
FTAを使った具体例
課題: カメラが電源を入れても動作しない。
分析の流れ:
- トップイベント「カメラが動作しない」を設定。
- 原因を追求(例: バッテリーの接続不良、基板上の電源回路の故障、ファームウェアのバグ)。
- 各原因の重要度を評価し、最優先で対応すべき箇所を特定。
FMEAを使った具体例
課題: カメラのレンズ部品がズレやすい。
分析の流れ:
- レンズユニットの各構造部品を洗い出し、故障モードを特定(例: レンズホルダーの設計不良、固定部品の強度不足)。
- 影響の重大性、発生確率、検出可能性を評価(RPNを算出)。
- スコアが高い箇所から優先的に設計変更(例: 固定部品の材質を変更、組み立て精度を向上する設備を導入)。
FTAとFMEAの選択ポイント
- システム全体を俯瞰し、重大な故障の根本原因を探る場合: FTAが有効。
- 個別の部品や工程を詳細に分析し、リスクを予防したい場合: FMEAを活用。
- 両方を併用することで、システム全体と詳細部分の両面でリスク管理が可能。たとえば、カメラ全体の安全性をFTAで評価し、レンズやセンサーなどの個別部品はFMEAで分析するなど。
これらの手法をうまく組み合わせることで、設計段階から品質と安全性を高めることができます。
FMEA やり方を理解するための総括ポイント
本記事のまとめを以下に列記します。
- FMEAは製品やプロセスの潜在リスクを洗い出し、対策を講じる手法
- DFMEAは設計段階での問題予測に特化している
- PFMEAは製造工程の問題予測と防止を目的とする
- DFMEAとPFMEAを組み合わせることで品質管理が強化される
- 分析対象を明確にすることがFMEAの第一歩
- 故障モードを洗い出し、リスクをスコア化する
- RPNを算出し、優先度の高いリスクに対応する
- DFMEAでは設計の強度不足や材料選定を重点的に評価する
- PFMEAでは工程ミスや設備不良に焦点を当てる
- チームで分析を行い、多角的な視点を取り入れる
- スコアリングには重大性、発生確率、検出可能性を用いる
- DFMEAの結果をPFMEAに活用し、リスクを統合管理する
- 定期的なモニタリングで新たなリスクを見直す
- FMEAはコスト削減と顧客満足度向上につながる
- 適切なフォーマットを選ぶことで効率的に分析が進む
コメント