PPAP(生産部品承認プロセス)は、自動車業界において部品の品質を保証し、製造プロセスの信頼性を高めるための重要な基準です。
特にIATF16949の枠組みの中で採用されており、PPAPの18項目や提出レベルに基づき、詳細な品質確認が求められます。
PPAPとは、自動車業界の品質向上を目指して導入されたプロセスであり、顧客の要求事項を満たすために設計、製造、検査のすべてを網羅的に管理します。
このプロセスを通じて、設計図や工程フロー、試験結果などの書類を整備し、PPAP提出レベルごとに顧客に承認を受ける仕組みです。
この記事では、PPAPとは何か、品質管理における役割やIATF16949における位置づけ、さらにはPPAPに必要な書類の具体例などを詳しく解説します。
自動車部品の品質保証や信頼性向上に欠かせないPPAPの全体像を、わかりやすくお伝えします。
- PPAPの基本概念と自動車業界における役割
- PPAPの18項目と提出レベルに基づく品質管理の流れ
- IATF16949におけるPPAPの位置づけと重要性
- PPAPに必要な書類と具体的な準備方法
- PPAP製造を徹底解説!基本から押さえたいポイント
- PPAP製造の成功の秘訣と実践方法
- 提出レベルで異なるPPAPの対応方法とは?
- PPAPの18項目を詳細解説!完全ガイド
- 1. 設計図書 (Design Records)
- 2. 設計変更認可 (Authorized Engineering Change Documents)
- 3. 顧客の設計承認 (Customer Engineering Approval)
- 4. 設計FMEA (Design Failure Mode and Effects Analysis)
- 5. 工程フロー図 (Process Flow Diagram)
- 6. 工程FMEA (Process Failure Mode and Effects Analysis)
- 7. コントロールプラン (Control Plan)
- 8. 測定システム解析 (Measurement System Analysis Studies – MSA)
- 9. 寸法検査結果 (Dimensional Results)
- 10. 材料記録および性能テスト結果
- 11. 初期工程調査 (Initial Process Studies)
- 12. 試験所の資格の証明書 (Qualified Laboratory Documentation)
- 13. 外観承認レポート (Appearance Approval Report – AAR)
- 14. 製造サンプル (Sample Production Parts)
- 15. マスターサンプル (Master Sample)
- 16. 検査具 (Checking Aids)
- 17. 顧客固有要求事項 (Customer-Specific Requirements)
- 18. 部品提出保証書 (Part Submission Warrant – PSW)
- PPAPの18項目を車載カメラで実践する重要性
- PPAPの工程と審査プロセスをスムーズに進める方法
- PPAP製造で品質と信頼性を高めるための要点
PPAP製造を徹底解説!基本から押さえたいポイント
PPAP(生産部品承認プロセス)は、製造業、特に自動車業界で部品や製品の品質を保証するための重要な基準です。
このプロセスは、新しい部品や製造工程が顧客の要求を満たしていることを確認し、安全性や信頼性を確保する役割を果たします。PPAPの歴史は1980年代にさかのぼり、米国の自動車業界で品質管理を標準化する目的でAIAGによって導入されました。
現在では、IATF16949の枠組みの中でグローバルに採用されており、トヨタやホンダなどのメーカーが独自の品質基準とともに使用しています。
特に車載カメラのような高度な技術製品では、PPAPを通じて設計、製造、品質管理の全プロセスを徹底的に検証し、高性能かつ信頼性の高い製品を市場に提供することが可能となります。
本記事では、PPAPの全体像、具体的なプロセス、そして自動車業界や車載カメラにおけるその重要性について詳しく解説します。
PPAPとは製造業で求められるプロセスとは?
PPAP(生産部品承認プロセス:読み方 ピーパップ)は、製造業において新しい部品や工程を導入する際、製品が顧客の要求を満たしていることを確認するための重要なプロセスです。特に自動車業界を含む品質基準が厳しい業界で、製品の信頼性と一貫性を確保するために活用されています。
PPAPでは、設計図や工程フロー、品質管理の手順など複数の資料を提出し、顧客からの承認を受けることで、生産工程が適切であることを証明します。このプロセスを実施することで、不良品の発生リスクを低減し、製造品質を一定に保つことができます。
車載カメラ製造においても、PPAPを適用することで、高度な安全性と性能を持つ製品を市場に提供することが可能となります。
自動車業界でのPPAPの重要性とは?
自動車業界では、部品やシステムの信頼性が安全性に直結するため、PPAP(生産部品承認プロセス)は極めて重要な役割を担っています。
PPAPを導入することで、新しい部品やプロセスが厳格な基準を満たしているかを包括的に検証し、製品の欠陥を未然に防ぐことができます。
特に車載カメラにおいては、その重要性が一層高まります。車載カメラは先進運転支援システム(ADAS)や自動運転技術の中核を担う部品であり、車両の周囲を正確に検知し、リアルタイムで情報を提供する必要があります。これにより、事故のリスクを減らし、ドライバーや歩行者の安全性を向上させる役割を果たしています。
車載カメラのような精密部品に対するPPAPの具体的な重要性は次の通りです:
- 視認性能の保証:車載カメラは、物体検知やレーン認識などの重要なタスクを担います。PPAPを通じて、カメラ部品の光学性能やセンサーの精度が厳密に評価されるため、誤認識や誤作動を防ぐことができます。
- 耐久性の検証:自動車は厳しい温度変化や振動が発生する環境下で使用されます。PPAPにより、車載カメラがこれらの過酷な条件でも正確に動作する耐久性を備えていることが確認されます。
- 信頼性の一貫性:量産においても初期設計時と同様の高品質を維持することが求められます。PPAPでは、製造プロセスが一貫性を保てるかどうかが確認されるため、信頼性のある車載カメラの供給が可能になります。
PPAPを適切に実施することで、車載カメラの品質はもちろん、自動車全体の安全性と信頼性が向上します。また、製造段階での不具合を削減できるため、製品の市場投入までの期間を短縮し、顧客満足度の向上にも寄与します。
このように、車載カメラを含む重要部品の信頼性を確保するPPAPは、自動車業界全体の品質向上に欠かせないプロセスです。
PPAPの歴史とその進化を知る
PPAP(生産部品承認プロセス)の歴史は、自動車業界の品質管理手法の進化と密接に関わっています。1980年代後半から1990年代初頭にかけて、自動車業界全体で製品品質を向上させる必要性が高まりました。この背景には、グローバル市場での競争激化と、顧客の安全性に対する要求が厳しくなったことがあります。
PPAPは、アメリカの自動車業界で使用されていた品質管理手法を標準化するため、AIAG(自動車産業行動グループ)によって初めて定義されました。
その目的は、製品開発プロセスを明確にし、部品や材料の品質が顧客の要求を満たしていることを確認することでした。
当初は、米国のビッグスリー(GM、フォード、クライスラー)によって使用されていましたが、その後、ISO/TS 16949(現IATF 16949)の採用に伴い、グローバルな自動車メーカーやサプライヤーにも広がりました。
特に、トヨタやホンダなどの日本のメーカーも独自の品質基準と合わせてPPAPを採用し、品質保証体制を強化しています。
車載カメラのような高度な技術製品が増える中で、PPAPも進化を遂げています。特に、今日ではAI技術や自動運転技術の発展により、より複雑な部品にも対応可能なフレームワークとして活用されています。
このような背景を理解することで、PPAPが単なるプロセスではなく、品質向上のための重要なツールであることがわかります。
PPAPの歴史を学ぶことで、その役割や意義を深く理解でき、現在の品質保証プロセスへの応用にも役立てることができます。
PPAPの全体像
PPAPは、自動車業界で部品や製品の信頼性を確保するための重要なプロセスです。PPAPは、「計画」「設計・開発」「製造プロセスの検証」「顧客承認」「生産立ち上げ」の5つの主要ステップで構成され、それぞれの段階で特定の資料が必要になります。
以下では、車載カメラがADAS(先進運転支援システム)に関連する場合を例に、具体的な進め方と必要資料について説明します。
※PPAPにおいて必要となる各資料は後述します。
1. 計画
この段階では、車載カメラがADASで果たす役割を定義し、要件を明確にします。例えば、レーンキーピングアシストや障害物検知に必要な視野角、解像度、応答速度などが挙げられます。この情報をもとに、適切な設計と製造プロセスを計画します。
必要なPPAP資料例:
- デザイン記録(設計図面や仕様書)
- 設計FMEA(潜在的な欠陥を分析するための文書)
2. 設計・開発
この段階では、車載カメラのプロトタイプを開発し、試験を実施します。性能評価試験を通じて、設計要件が満たされていることを確認します。例えば、カメラのレンズやセンサーが設計通りに動作するか、各部品の統合が適切であるかを検証します。
必要なPPAP資料例:
- 測定システム分析(MSA)
- 初期製品試験結果(物理的・機能的な性能テスト結果)
3. 製造プロセスの検証
プロトタイプが完成した後、量産を見据えた製造工程の試験が行われます。ここでは、カメラが厳しい環境(振動、温度変化、湿度など)でも性能を発揮できるかを確認します。また、製造設備や工程の安定性も評価されます。
必要なPPAP資料例:
- 工程フロー図
- 工程FMEA(製造段階での潜在的リスクの評価)
- 管理計画書(Control Plan)
4. 顧客承認
製造工程が確立し、試験結果が問題ないことを確認したら、顧客による承認を求めます。この段階では、ADASシステムメーカーや自動車メーカーに試験データや製造記録を提出し、仕様通りの性能が達成されていることを証明します。
必要なPPAP資料例:
- サンプル製品とその検査結果
- 顧客特有の要求事項(CSR)
5. 生産立ち上げ
顧客承認を受けた後、実際の量産を開始します。初期の量産品を対象に品質の一貫性や安定性を確認し、不具合がないかをチェックします。また、長期的な品質維持のための体制を整備します。
必要なPPAP資料例:
- 初期流動管理データ(生産初期の品質データ)
- 包括的な外観・機能チェックリスト
- PSW
PPAPを適切に実施することで、車載カメラのように高い精度と安全性が求められる製品の品質を確保できます。また、各段階で適切な資料を準備することで、潜在的な問題を早期に発見し、効率的な生産を実現します。
品質保証におけるPPAPの役割とは?
品質保証において、PPAP(生産部品承認プロセス)は、製品が設計仕様や顧客の期待を満たすことを保証する重要な検証手段です。
PPAPは、設計通りの部品が正確に作られ、量産時でもその品質が一貫して維持されることを確認します。
具体例
特に車載カメラのような高精度部品では、PPAPは品質保証の要となります。ADAS(先進運転支援システム)や自動運転システムでは、車載カメラが撮影した画像データが車両の制御に直結するため、以下のような項目が品質保証上の重要課題となります。
- 焦点距離の精度検証: 車載カメラが適切な焦点距離を維持できることをPPAPを通じて確認し、道路標識や車線の検出精度を保証します。
- 動作温度範囲の確認: 自動車の厳しい環境(極寒や高温)でもカメラが正常動作するかを試験します。これにより、あらゆる環境下でのADAS性能が担保されます。
- 製造ばらつきの管理: カメラセンサーやレンズの製造プロセスにおけるばらつきを最小限に抑えることで、不良率を低下させるとともにコスト削減を実現します。
PPAPの品質保証におけるメリット
- 不良品の市場流出を防止: 生産前に製品品質を徹底的に検証するため、市場での不具合発生を未然に防ぎます。
- 顧客満足度の向上: 高品質な製品を提供することで、顧客の信頼を確保し、リピートビジネスにつながります。
- 継続的な改善の促進: PPAPに含まれる工程FMEAや測定システム分析(MSA)を活用することで、製造プロセスの弱点を把握し、継続的な改善を実現します。
品質保証におけるPPAPの役割の拡大
PPAPは、単なる製品検証の手段にとどまりません。適切に実行することで、企業が競争優位性を築き、長期的な市場での成功を収めるための基盤となります。
例えば、PPAPで構築されたデータは、車載カメラの次世代モデルの設計や製造にも役立ち、製品開発の効率化と品質向上を同時に達成します。
PPAPを正確に実行し、顧客が求める品質基準を満たすことは、製品の信頼性を確保するだけでなく、ブランド価値を高める重要なステップです。
そのため、品質保証活動においてPPAPを徹底することは、製品の成功と顧客満足のカギを握ると言えます。
IATF16949におけるPPAPの位置づけ
IATF16949は、自動車業界における国際的な品質管理規格であり、その中でPPAP(生産部品承認プロセス)は重要な役割を担っています。この規格では、「顧客要求を最優先とし、品質を確保する」ことが強く求められています。
IATF16949と顧客要求の関係
IATF16949は、製品やプロセスが顧客の仕様や基準を確実に満たすことを目的としています。そのため、PPAPは単なる品質確認の手法ではなく、顧客要求を反映し、それを製品設計や製造プロセスに組み込むためのツールとして位置づけられています。
例えば、車載カメラの製造においては、顧客が指定する視認性能や耐久性に関する要求事項を正確に満たす必要があります。これを達成するために、PPAPを通じて以下の確認が行われます。
- 設計図や仕様書が顧客の要求通りであることの確認
- 試作段階で顧客が求める性能基準をクリアすることの検証
- 量産における一貫した品質保証のための製造プロセスの安定化
PPAPを通じた顧客要求への対応
PPAPは、IATF16949において顧客要求に応えるための具体的な手法として以下を実現します。
- 要求事項の文書化と明確化:PPAPの提出書類(18項目)を通じて、顧客が求める基準や条件を詳細に文書化します。これにより、双方の認識のズレを防ぎます。
- 顧客承認プロセスの統合:顧客の承認を受けるまでの過程がPPAPに含まれており、これにより製品が顧客の期待に沿ったものであることが確認されます。例えば、車載カメラの場合、解像度や動作温度範囲のテスト結果を顧客に提示し、フィードバックを反映します。
- トラブルの事前回避:PPAPでは、量産開始前に製品やプロセスのリスクを特定し、改善する仕組みが構築されています。これにより、不良品の発生や納期遅延といった顧客に影響を与える問題を最小限に抑えます。
具体例
車載カメラ製造でのPPAP活用では、以下のようなステップが顧客要求に対応するために行われます:
- 顧客要求仕様の取り込み:カメラの解像度、夜間性能、視野角など、顧客が求める性能指標を設計段階で明確にし、すべての工程でこれを基準とします。
- プロセス検証での実証:例えば、車載カメラが-40℃から+85℃の温度範囲で動作することを保証するため、PPAPの工程能力検証(18項目の一部)を実施し、顧客に提示します。
- 顧客への定期的な進捗報告:試作段階から量産まで、品質データや試験結果を定期的に顧客に報告し、承認を得るプロセスを含めることで、信頼関係を強化します。
顧客要求を最優先にするIATF16949のメリット
PPAPをIATF16949の枠組みで適切に実行することにより、以下のメリットが得られます。
- 顧客との信頼関係の構築:透明性のある品質管理を実施することで、顧客は安心して製品を採用できます。
- リスクの低減:顧客の基準に適合した製品を事前に確認するため、納品後のクレームや不具合を防ぎます。
- 市場競争力の向上:顧客の期待を上回る品質とサービスを提供することで、競合他社との差別化が可能となります。
IATF16949におけるPPAPの位置づけは、「顧客要求を第一に考えた品質管理」を実現するための基盤です。特に車載カメラのような安全性が重視される製品では、顧客の要望を細部まで理解し、それを具体的なプロセスで実現することが、品質保証と信頼性向上の鍵となります。
関連記事:IATF16949とISO9001の違いをまとめた初心者・中級者向け解説
PPAP製造の成功の秘訣と実践方法
PPAP(生産部品承認プロセス)は、製造業において製品が顧客要求を満たし、高い品質を持つことを証明するためのプロセスです。
その重要性は、自動車業界や車載カメラのような精密部品の製造において特に際立っています。PPAPは設計承認から最終審査までの一連の工程を含み、製品の信頼性を確保しつつ、不具合の発生リスクを最小限に抑えます。
顧客固有の要求や提出レベルに応じた柔軟な対応、適切な事前準備、そしてチーム間の連携がPPAP成功の鍵です。
本記事では、PPAPの提出レベルごとの対応方法や工程をスムーズに進める秘訣を具体例を交えながら解説します。
提出レベルで異なるPPAPの対応方法とは?
PPAP(生産部品承認プロセス)では、顧客の要求や部品の重要度に応じて、提出レベルが1から5まで設定されています。それぞれの提出レベルで必要な情報や資料の範囲が異なり、適切なレベルで対応することが品質承認プロセスをスムーズに進めるために重要です。
以下では、各提出レベルの詳細と、どの資料が必要になるかを具体的に解説します。
提出レベル1: 製品提出書(PSW)のみ
このレベルでは、最低限の情報である**製品提出書(Part Submission Warrant: PSW)**のみが要求されます。これは、製品が顧客の仕様を満たしていることを宣言する基本的な書類です。
- 必要な資料:
- PSW(製品提出書)
- 主な適用例:
製品変更の影響が非常に軽微な場合や、リスクが低い場合。
提出レベル2: PSW + 部分的な補足資料
レベル2では、PSWに加えて、顧客が指定した補足資料の提出が必要です。この資料は、製品の重要な側面を確認するためのものに限定されます。
- 必要な資料:
- PSW
- 顧客が要求する資料(例: 材料試験結果、簡易的な設計図など)
- 主な適用例:部分的な設計変更が行われた場合や、比較的重要度が低い部品。
提出レベル3: PSW + 主要な補足資料
レベル3では、PSWに加えて、主要なPPAP文書が求められます。これには設計やプロセスに関する基本情報が含まれます。車載カメラの製造プロセスでは、カメラモジュールの主要設計図や試験データが該当します。
- 必要な資料:
- PSW
- 設計図(Drawings)
- 材料証明書(Material Certifications)
- 試験結果(Test Results)
- 主な適用例:新規部品の開発時や、既存部品の重要な仕様変更。
提出レベル4: 顧客が指定した全資料
レベル4は、顧客が特に指定した文書をすべて提出する必要があります。このレベルでは、提出範囲が柔軟であり、顧客の具体的な要求に応じて内容が異なります。
- 必要な資料:
- PSW
- 顧客が指定するすべての資料(例: 設計図、測定データ、プロセスフロー図など)
- 主な適用例:顧客との共同開発案件や、特殊な要求仕様を持つ部品。
提出レベル5: 顧客による全資料の現地確認
レベル5では、すべてのPPAP文書を顧客に直接提示し、顧客が現地で確認します。このレベルは非常に厳格で、特に車載カメラのように安全性が最優先される部品で適用されます。現地でのレビューは、製造ラインや品質管理プロセスの視察も含まれることがあります。
- 必要な資料:
- PSW
- 設計図
- 測定結果
- プロセスフロー図(Process Flow Diagram)
- 制御計画書(Control Plan)
- 生産試験結果(Production Test Results)
- PPAPの全18項目(後述)
- 主な適用:高リスク製品や、初めての取引先での新規部品供給時。
車載カメラにおける提出レベル選択
車載カメラのような高度な安全技術が求められる部品では、通常レベル3以上の提出が求められます。特にADAS(先進運転支援システム)に組み込まれるカメラの場合、厳格な性能要件を満たすため、レベル5が適用されることが多いです。
顧客の要求や製品のリスクを正確に把握し、適切な提出レベルで対応することで、品質承認プロセスをスムーズに進めることが可能です。
※PSWの参考記事:PSW 自動車の基本知識と品質保証の重要ポイント
PPAPの18項目を詳細解説!完全ガイド
PPAP(生産部品承認プロセス)には、製品とプロセスの品質を保証するために、18の項目が設定されています。これらの項目は、部品が顧客の要求を満たし、量産時にも一貫した品質を維持できることを証明するためのものです。
ここでは、車載カメラ(特にADAS向け)を例に、各項目の具体的な内容と重要性を詳しく説明します。
1. 設計図書 (Design Records)
詳細説明:設計図書は、製品の設計に関する詳細な情報が記載された文書で、製品の正確な製造と品質保証の基盤となる重要な要素です。
この資料には、設計図面、CADデータ、技術仕様書が含まれます。また、製品に使用される材料の組成や環境負荷物質に関する情報も記載されます。特に自動車業界では、環境基準への適合を示すため、材料情報をIMDS(International Material Data System)を通じて提供することが一般的です。
これにより、リサイクルや環境保護の観点から、製品が適切な材料で構成されていることが確認されます。
設計図書の役割は、製品が設計通りに製造されることを保証し、設計に基づくトレーサビリティを確保することです。これにより、製造中や使用後に問題が発生した場合の原因追跡が容易になります。
車載カメラの具体例:ADAS(先進運転支援システム)用車載カメラでは、以下の要素が設計図書に含まれます:
- 焦点距離:カメラのレンズが特定の距離で正確に焦点を合わせることができる設計要件を示します。例えば、10~100mの距離で対象物を認識するための焦点設定が記載されています。
- 視野角:カメラがカバーする横方向や縦方向の視野範囲。例として、ADASでは120度の広視野角が一般的ですが、死角のない視認性を確保するための技術仕様が詳細に記載されます。
- 筐体材質:カメラを保護する外装部分の材質が記載されています。例えば、-40℃から85℃の温度範囲で動作するために、耐熱性や耐衝撃性に優れたポリカーボネートが指定されます。
- 環境性能:耐久性や耐候性試験の結果に基づく基準が記載されます。塩水噴霧試験や紫外線曝露試験をクリアしたことが報告されます。
加えて、IMDSレポートに基づき、カメラの構成部品(レンズ、センサー、回路基板など)で使用される材料が、RoHSやELV指令などの環境規制を満たしていることを示す情報も含まれます。
強化ポイント
- 設計図書は、顧客要求に応じた具体的な設計要件を反映させ、品質基準を明確化するための重要な資料です。これにより、製造段階での齟齬を防ぎ、最終製品の信頼性向上に寄与します。
- 車載カメラのような安全性が重視される製品では、設計図書に記載された要件をもとに、性能試験や環境適合性試験が実施されます。
- IMDSレポートを活用することで、製品の材料構成が世界的な環境基準に適合していることを証明し、グローバルな市場展開を円滑にします。
設計図書は単なる図面以上の役割を果たし、製品の品質と信頼性を支える基盤です。
2. 設計変更認可 (Authorized Engineering Change Documents)
詳細説明:設計変更認可は、製品の設計が変更された際に、その変更が顧客の承認を受けたことを証明する文書です。設計変更は通常、性能向上、コスト削減、生産効率向上、または顧客からの特別な要求に基づいて行われます。
PPAPプロセスでは、設計変更が製品の品質や性能にどのように影響するかを評価し、その変更内容と結果を文書化して顧客に提出する必要があります。
この文書は、設計変更が最終製品の適合性や性能にどのような影響を与えるかを顧客と共有し、承認を得ることで、品質基準を確保しつつ製品の改良を進めるための重要なステップとなります。
さらに、文書により変更履歴が明確に記録され、トレーサビリティが確保されます。
車載カメラの具体例:ADAS(先進運転支援システム)用車載カメラでは、次のような設計変更が発生する場合があります:
- レンズ設計の変更:例として、コスト削減のためにレンズの素材を変更する場合があります。これには、光学性能(焦点距離や透過率)を維持しつつ、コストを削減することが目的とされます。変更後の素材で製造されたカメラは、耐久性試験や光学性能試験が実施され、その結果が設計変更認可文書に含まれます。
- センサーのアップグレード:顧客の要請により、画素数を向上させたセンサーへの変更が求められることがあります。この変更では、カメラの解像度や視認性能の向上が目的ですが、新しいセンサーが温度変化や振動に耐えられるかを確認するための試験結果が文書化され、顧客承認の対象となります。
- 筐体材質の変更:車載環境での使用条件に応じて、筐体素材をより軽量で耐久性の高いものに変更する場合があります。変更後の材質が耐熱試験や塩水噴霧試験に合格していることを示す試験結果が設計変更認可文書に含まれます。
強化ポイント
- 設計変更認可文書には、変更の背景(目的と理由)、具体的な変更内容、および変更後の試験結果が詳細に記載される必要があります。
- 顧客承認プロセスでは、変更後の製品が既存の基準を維持または超える性能を発揮することを確証するデータが不可欠です。
- 車載カメラのように安全性や信頼性が重要視される製品では、設計変更が最終製品の性能に及ぼす影響を慎重に評価する必要があります。
例えば、ADAS用カメラのレンズ設計変更では、顧客が変更後の光学性能(焦点距離や視野角)を厳密に確認し、認可を与えることが重要です。
この文書が適切に作成され、承認を得ることで、変更プロセスが製品全体の品質向上に寄与します。
3. 顧客の設計承認 (Customer Engineering Approval)
詳細説明:顧客の設計承認は、顧客が製品設計や性能試験を直接評価し、設計要件を満たしていると確認したことを示す文書です。
この承認プロセスでは、製品が顧客が期待する仕様や性能基準をクリアしていることを証明するために、様々な試験結果や解析結果が提出されます。
顧客が独自の試験を実施する場合や、提供された試験データを精査して承認を行う場合があり、承認の取得は製品が量産に進むための重要なステップとなります。
顧客の設計承認文書には、以下が含まれることが一般的です:
- 製品が設計基準を満たしていることを証明する試験データ。
- 試験条件や手順の詳細。
- 顧客が製品性能を検証した結果に基づく承認文書。
車載カメラの具体例:ADAS(先進運転支援システム)用の車載カメラにおいて、顧客設計承認が求められる場面を以下に示します:
- 動作温度範囲の試験結果の承認:車載カメラは、極端な温度環境での使用が想定されるため、動作温度範囲(例:-40℃~85℃)が設計要件を満たすことが重要です。この場合、カメラを温度試験装置に入れ、極端な低温および高温環境で正常に動作することを確認した試験データを顧客に提出します。顧客はこの試験結果を確認し、製品が基準を満たしていることを承認します。
- 振動耐性試験の承認:車載カメラは車両の振動にさらされるため、振動試験によって部品が破損せず、性能が維持されることを証明する必要があります。振動試験の結果を顧客に提出し、カメラが車載環境での使用に適していると承認されます。
- レンズの光学性能試験結果の承認:カメラの焦点距離や視野角などの光学性能が、ADASの要件を満たしていることを確認します。このデータには、カメラが設計した視野角(例:120°)で物体を正確に捉える性能が含まれます。顧客がそのデータを確認し、承認します。
- EMC(電磁適合性)試験結果の承認:車載カメラは、車両内の他の電子機器と干渉しないことが求められます。電磁波干渉(EMI)の試験結果を提出し、製品が規定された基準値を満たしていることを顧客に認めてもらいます。
強化ポイント
- 試験条件の透明性:顧客が承認を行う際、試験条件や手順が明確に記載されていることが求められます。例えば、動作温度試験では試験装置の仕様や試験時間を記載します。
- 顧客の視点でのデータ提供:車載カメラの最終用途(ADASや自動運転システムなど)を考慮し、設計要件が安全性や性能に与える影響をデータで説明することが重要です。
顧客の設計承認文書が適切に作成されることで、顧客との信頼関係が強化され、製品が市場に投入される際のリスクが大幅に軽減されます。
4. 設計FMEA (Design Failure Mode and Effects Analysis)
詳細説明:設計FMEA(設計における故障モードと影響の分析)は、設計段階で製品の潜在的な欠陥や故障モードを予測し、それらが顧客や製品に与える影響を分析するプロセスです。
この文書は、設計上のリスクを評価し、優先順位をつけて対応策を講じるための指針を提供します。設計FMEAは、故障を予防するための設計改善を促進し、製品の信頼性を向上させる重要な役割を果たします。
FMEAプロセスの主な要素:
- 潜在的な故障モードの特定:製品がどのように故障する可能性があるかを洗い出します。
- 故障の影響分析:故障が製品の機能や顧客に与える影響を評価します。
- 原因の分析:故障が発生する原因を特定し、設計のどの部分でリスクが高いかを判断します。
- 優先順位の設定:発生頻度、影響の深刻度、検出可能性の評価を基に、リスクの高い項目を優先して対策を立てます。
- 是正措置の計画:リスクを軽減するための具体的な改善案を提案します。
車載カメラの具体例:ADAS(先進運転支援システム)用の車載カメラを例に、設計FMEAの具体的な実施内容を以下に説明します:
- 潜在的な故障モード:防水設計の不備:車載カメラは外部環境にさらされるため、防水性が不足していると水が侵入し、内部回路が故障するリスクがあります。
- 影響分析: 防水性が不足すると、カメラの動作が停止し、ADAS機能が一時的に利用できなくなる可能性があります。これは重大な安全リスクを伴います。
- 原因の分析:シール材の劣化:防水性能の欠如の主な原因として、使用しているシール材が温度変化や紫外線によって劣化することが特定されました。
- 優先順位の設定:リスクの評価:防水性の不足は、安全性に直接影響するため、FMEAスコアリングシステム(発生頻度、影響度、検出可能性)では高い優先度が付けられます。
- 是正措置:シール材の改善
- 新しい耐熱性と耐紫外線性を備えたシール材を採用することが提案されました。
- 試験条件:50°Cから-20°Cの温度変化を繰り返す耐久試験を実施し、改良後のシール材の性能を検証。
- 結果と評価:改善されたシール材を用いることで、水侵入リスクが大幅に低減され、耐久性が向上。顧客からの防水性能要件もクリアしました。
その他の具体例
- 振動による部品の緩み:車載カメラの取り付け部品が振動により緩むリスクを特定。解決策として、取り付け方法を変更し、緩み防止加工を追加しました。
- 熱放散の不足:内部温度が上昇し、センサーが正確に動作しなくなるリスクを評価。熱放散用ヒートシンクを設計に追加し、熱管理性能を向上させました。
強化ポイント:設計FMEAを適切に実施することで、製品設計段階でリスクを未然に排除でき、量産後のクレームやリコールを防ぐ効果が期待できます。特に車載カメラのような安全性が求められる製品では、FMEAの徹底的な分析と改善が、製品品質と顧客満足度の向上に直結します。
参考記事:FMEA やり方を徹底解説!初心者にもわかる具体例付き手法
5. 工程フロー図 (Process Flow Diagram)
詳細説明:工程フロー図(Process Flow Diagram)は、製品の製造過程を段階的に図示し、各工程の順序や流れを明確にしたものです。この図は、製造プロセス全体の理解を深め、効率的かつ一貫性のある生産を保証するために使用されます。
工程フロー図は、製品品質を維持するための基盤であり、工程間のインターフェースや潜在的なボトルネックを特定するのに役立ちます。
主な要素:
- 工程の順序:製品がどのような手順で製造されるかを示します。
- プロセスの詳細:各工程で使用される設備、材料、作業方法が記載されます。
- 検査や試験のポイント:品質確認が行われる段階や試験内容が図示されます。
- 関連部門やリソース:どの部門がどの工程を担当するか、必要なリソースも示されます。
車載カメラの具体例:ADAS用車載カメラの製造プロセスを例に、工程フロー図の内容を強化します。
- 基板実装 (PCB Assembly)
- 工程の詳細: カメラの心臓部である基板に電子部品を実装。自動実装機(SMT)が使用され、温度制御されたリフロー工程で部品が固定されます。
- 品質確認: 実装後、基板の電気特性を検査し、誤配線や接触不良がないことを確認します。
- レンズ取り付け (Lens Assembly)
- 工程の詳細: 高精度な機械でレンズを取り付け、位置合わせを行います。焦点距離や視野角が設計通りであることが重要です。
- 品質確認: レンズの位置調整後、光学試験を行い、視野角や画質を確認します。
- 筐体組み立て (Housing Assembly)
- 工程の詳細: カメラモジュールを筐体に組み込みます。この工程では、防塵・防水性能を確保するために高精度なシール加工が施されます。
- 品質確認: 組み立て後、防塵試験を実施して異物混入を防ぎます。
- 防水試験 (Waterproof Testing)
- 工程の詳細: 組み立てが完了したカメラに対して防水性能を検証。IP67規格に基づき、水中に一定時間浸漬させる試験を行います。
- 品質確認: 試験後、内部への水の侵入がないかを確認します。漏水が確認された場合、工程改善が行われます。
- 最終検査 (Final Inspection)
- 工程の詳細: カメラのすべての機能を最終確認。解像度や色彩の正確性、動作温度範囲などが試験されます。
- 品質確認: 最終検査結果はデータベースに記録され、トレーサビリティを確保します。
工程フロー図の強化ポイント
- 視覚化: 各工程をシンプルなアイコンや色分けを用いて視覚的に表現し、誰でも理解しやすい形にします。
- リスク評価: 工程ごとに発生し得るリスク(例: 振動でのレンズズレ、防水不良)をフロー図内で明記。
- 改善点の特定: ボトルネックや冗長なプロセスを特定し、生産効率を向上させる提案を含めます。
工程フロー図の価値:工程フロー図は、製造過程全体の可視化により、効率的な生産管理を可能にします。車載カメラの場合、各工程がADASの精度や耐久性に直接影響を与えるため、このフロー図を活用して高品質な製品を効率的に市場へ届けることができます。
6. 工程FMEA (Process Failure Mode and Effects Analysis)
詳細説明:工程FMEA(Process Failure Mode and Effects Analysis)は、製造プロセス中に発生する可能性のある欠陥や失敗を事前に特定し、それらが製品や顧客に与える影響を評価するための分析手法です。
このプロセスでは、リスクの優先順位を決定し、リスクを低減または排除するための対策を計画します。
主なステップ:
- 潜在的な失敗モードの特定:製造工程でどのような不良や失敗が起こり得るかを洗い出します。
- 影響の分析:発生した失敗が製品性能や安全性にどのように影響するかを評価します。
- 発生頻度と検出可能性の評価:欠陥が発生する確率と、それを発見する可能性を数値化します。
- リスク優先度数 (RPN) の計算:発生頻度、影響の重大度、検出可能性を掛け合わせてリスクの大きさを算出します。
- 改善策の実施:高いRPNを持つ項目に対して、改善策を設計し、工程を最適化します。
車載カメラの具体例:ADAS用車載カメラの製造プロセスにおける工程FMEAの実例を以下に示します。
- 潜在的な失敗モード: レンズ取り付け時のズレ
- 影響: レンズの位置がズレると、焦点が合わなくなり、視野角が設計値を外れる可能性があります。これにより、ADAS機能(例: 車線認識、障害物検出)の精度が低下します。
- 対策: 高精度な治具の設計を推奨。治具に自動調整機能を追加し、取り付けの際にズレを防止します。
- 潜在的な失敗モード: ハウジングの密閉不良
- 影響: 防水性能が低下し、内部に水分が侵入。電気回路が短絡し、カメラが動作不良を起こす可能性があります。
- 対策: シーリング材の選定を見直し、製造後に気密検査を追加します。
- 潜在的な失敗モード: 回路基板の静電気ダメージ
- 影響: 静電気放電(ESD)が基板上の電子部品を破損させるリスクがあります。ADAS全体の動作に悪影響を及ぼします。
- 対策: 作業環境のESD対策(静電気防止手袋、アース接続)、および基板設計段階での保護回路を追加。
- 潜在的な失敗モード: 防水試験の漏れ検知不良
- 影響: 防水試験が不十分な場合、耐久性が不足し、長期使用でのトラブルにつながる可能性があります。
- 対策: 漏れ検知装置の精度を向上させ、試験データを自動記録するシステムを導入。
工程FMEAの強化ポイント
- 定量的評価の導入: 発生頻度、影響度、検出可能性を具体的な数値(1~10)で評価し、リスク優先度数(RPN)を計算することでリスクの大きさを定量的に示します。
- クロスファンクショナルチームの活用: 設計、製造、品質管理部門が協力して工程FMEAを実施することで、リスクを網羅的に特定します。
- フィードバックループの確立: 工程FMEAの結果を設計や製造プロセスに反映し、継続的な改善を図ります。
工程FMEAの価値:工程FMEAは、製品の信頼性を向上させるだけでなく、顧客からの信頼を得るためにも重要です。
車載カメラの例では、レンズの精度や防水性能の確保が、ADASの安全性や性能に直接的に寄与します。このような分析を通じて、顧客の要件を満たす製品を効率的に供給することが可能になります。
参考記事:FMEA やり方を徹底解説!初心者にもわかる具体例付き手法
7. コントロールプラン (Control Plan)
詳細説明:コントロールプランは、製品の品質を確保するために設計された試験や検査方法を一覧表として体系的にまとめた重要な文書です。
このプランでは、製品の各製造工程における品質管理アクティビティ(例: 寸法検査、材料試験、性能検証)が明確に規定されています。各項目には、測定基準、使用する装置、検査頻度、受け入れ基準、記録の保持方法が含まれます。
コントロールプランは、品質の一貫性を保つための指針として使用され、量産段階における不良品の発生を最小限に抑える目的があります。
主な構成要素:
- 製品特性: 管理が必要な特性(例: 寸法、材質、性能)。
- 工程パラメータ: 管理対象となる製造工程の条件。
- 検査方法: 測定手法や使用機器の指定。
- 検査頻度: 各検査を行うタイミング(例: バッチごと、日次、週次)。
- 基準値と許容範囲: 設計仕様に基づいた受け入れ基準。
車載カメラの具体例:ADAS用車載カメラのコントロールプランを以下の要素に基づいて強化します。
- レンズの光学特性の測定
- 試験内容: レンズの焦点距離、視野角、光透過率の測定。
- 使用装置: 高精度光学測定装置。
- 検査頻度: 各生産バッチごとに5つのサンプルを検査。
- 基準値と許容範囲: 焦点距離±0.1mm、視野角±2度、光透過率95%以上。
- 基板の実装状態検査
- 試験内容: 基板上のチップ実装の正確性と配線の短絡検査。
- 使用装置: 自動光学検査装置(AOI)。
- 検査頻度: すべての製造ロットで初回5基板を検査。
- 基準値と許容範囲: 配線間隔のズレ±0.01mm以内。
- 防水性能試験
- 試験内容: 筐体の防水性確認。IP67準拠の試験で、水没後に機能障害がないことを確認。
- 使用装置: 防水試験チャンバー。
- 検査頻度: 1,000個ごとにランダムで10個のサンプルを検査。
- 基準値と許容範囲: 水侵入なし、動作確認テスト合格。
- カメラの動作試験
- 試験内容: 動作温度範囲(-40℃~85℃)での性能確認。
- 使用装置: 環境試験チャンバー。
- 検査頻度: 各生産バッチごとにランダムで3台を選定。
- 基準値と許容範囲: すべての温度条件下での正常動作。
- 画像品質評価
- 試験内容: カメラが撮影する画像の解像度や色彩の再現性を確認。
- 使用装置: カメラ性能評価装置。
- 検査頻度: 生産初期に全数検査、その後はランダム検査。
- 基準値と許容範囲: 解像度1080p以上、色差△Eが許容範囲内。
コントロールプランの意義:コントロールプランは、製造プロセス全体で一貫した品質を維持するための基盤です。車載カメラの例では、光学特性や防水性能といった重要な特性を適切に管理することで、ADASの信頼性が大幅に向上します。
また、顧客要件を確実に満たし、リコールやクレームのリスクを減らすことが可能です。コントロールプランを活用することで、製造現場でのトラブルを未然に防ぎ、高品質な製品を安定して供給する仕組みが整います。
8. 測定システム解析 (Measurement System Analysis Studies – MSA)
詳細説明:測定システム解析(MSA)は、製品の品質を評価する際に使用される測定器具や測定プロセスの精度、信頼性、安定性を分析するための重要な手法です。これには主に「繰り返し性」と「再現性」の評価が含まれます。
- 繰り返し性: 同一条件下で同一測定者が繰り返し測定した際の一貫性。
- 再現性: 異なる測定者や測定条件での測定結果の一貫性。
MSAでは、測定装置の性能だけでなく、測定プロセス全体の信頼性を評価します。これにより、測定結果が設計基準や許容範囲を正確に反映していることを確認できます。
車載カメラの具体例:ADAS(先進運転支援システム)に使用される車載カメラの測定システム解析では、以下のような検証が行われます。
- 焦点距離の測定
- 試験内容: 測定装置がカメラの焦点距離(例: 25mm±0.1mm)を正確に測定できるかを検証します。
- 評価項目: 繰り返し性(同一装置、同一オペレーター)、再現性(異なるオペレーター間)。
- 手法: 測定装置で10個のサンプルを複数のオペレーターが測定。結果のばらつきを統計的に解析。
- 基準値: 測定ばらつきが全許容範囲の10%以下であること。
- 画角(視野角)の測定
- 試験内容: カメラが指定された視野角(例: 120度±2度)を適切に測定できるかを確認。
- 評価項目: 測定装置の正確性と測定者間の一貫性。
- 使用装置: 専用の光学試験装置を用い、異なる試験条件で測定を実施。
- 結果分析: 測定データの分散を分析し、視野角の測定精度を評価。
- 画像解像度の測定
- 試験内容: 測定装置がカメラの解像度(例: 1920×1080ピクセル)を正確に測定できるか。
- 評価項目: 測定機器の再現性が製品仕様の精度に合致しているかどうか。
- 測定手法: 画像キャプチャ装置で複数の試験サンプルを測定。画像分析ソフトウェアで結果を比較。
- 基準値: 解像度測定結果の変動が許容範囲内であること。
- 温度変化下での測定精度
- 試験内容: 測定装置が異なる温度条件(例: -40℃~85℃)で同じ精度を維持できるかを検証。
- 評価項目: 温度による測定ばらつきの影響を評価。
- 試験手法: 温度試験チャンバーを用いて、異なる温度環境下で測定データを取得し、ばらつきを比較。
- 基準値: 環境条件による測定誤差が設計仕様に影響を与えないこと。
MSAの意義:車載カメラにおけるMSAの徹底は、以下の利点をもたらします:
- 品質向上: 正確で信頼性の高い測定結果に基づき、製品品質を保証。
- コスト削減: 測定誤差による手直しや不良品の発生を抑制。
- 顧客満足: 顧客要件を確実に満たす製品の安定供給を実現。
MSAは単なる測定装置の検証にとどまらず、測定プロセス全体を統合的に管理し、製造プロセスの信頼性を高める重要な役割を果たします。
参考記事:IATF16949とISO9001の違いをまとめた初心者・中級者向け解説
9. 寸法検査結果 (Dimensional Results)
詳細説明:寸法検査結果は、製品の重要な寸法が設計図書や仕様書に合致しているかを確認するための検査データです。
これにより、設計基準通りに製品が製造されているかを検証します。寸法検査では、製品のすべての重要寸法(クリティカルディメンション)が対象となり、これらは顧客の要求事項を満たすために正確に管理される必要があります。
検査は、サンプル製品を用いて行われ、各寸法の測定結果が許容範囲内であることを確認します。測定に使用する機器や測定環境が適切であることも重要です。
また車両との接合部は重要管理寸法に位置付けられ、Cpkが1.33以上が要求されます。
(Cpkに関する参考記事:Cpk計算式を基礎から解説!工程能力指数の全知識)
車載カメラの具体例:ADAS(先進運転支援システム)用車載カメラにおける寸法検査結果の例として、以下の項目が挙げられます。
- 筐体寸法の測定
- 対象寸法: カメラ筐体の外形寸法(例: 高さ20mm、幅15mm、奥行き10mm ± 0.1mm)。
- 測定方法: デジタルノギスまたはCNC測定機を用いて、筐体の全サンプルを測定。
- 結果報告: 測定結果が設計図で指定された許容範囲内であることをレポート。
- レンズ取り付け位置の精度検査
- 対象寸法: レンズと筐体の取り付け位置の中心軸の偏差(例: ±0.05mm)。
- 測定方法: 3D光学測定器で位置関係を高精度に測定。
- 結果報告: レンズが光軸に対して適切に配置されていることを証明。
- PCB(プリント基板)の寸法確認
- 対象寸法: PCBの固定穴の位置、基板の厚さ、長辺と短辺の寸法。
- 測定方法: レーザー測定装置を使用し、基板の全体寸法と穴の位置を測定。
- 結果報告: 基板が正確に筐体に収まるよう設計寸法に合致しているかを記録。
- 防水シール材の寸法確認
- 対象寸法: 防水シール材の厚みや接合部分の幅(例: 厚み2.5mm ± 0.2mm)。
- 測定方法: 高精度プロファイル測定器で測定し、圧縮後の寸法を確認。
- 結果報告: シール材が筐体の設計要件を満たし、防水性能に寄与することを確認。
- 接続ポートの寸法検査
- 対象寸法: USB-Cや車載用CANポートの形状寸法、端子間のピッチ(例: ±0.01mmの精度)。
- 測定方法: 高倍率の測定顕微鏡を用いて接続ポートの精度を測定。
- 結果報告: 規格に合った寸法で、外部システムと正確に接続できることを保証。
寸法検査結果の意義寸法検査は、車載カメラの品質を保証するための重要なステップです。正確な寸法検査により、以下のメリットが得られます。
- 製品互換性の確保: 他の部品やシステムとの適切なフィットを保証。
- 品質問題の早期発見: 寸法不良を早期に検出し、不具合の拡大を防止。
- 信頼性の向上: 顧客要求を確実に満たす製品の提供が可能。
車載カメラのように厳密な品質管理が求められる製品では、寸法検査結果を正確に記録し、PPAP資料として提出することが、信頼性の高い製品供給を実現する基盤となります。
10. 材料記録および性能テスト結果
詳細説明:材料記録および性能テスト結果は、製品が指定された材料規格や性能基準を満たしていることを示すための文書です。
この記録には、製品に使用される材料の物理的、化学的特性の詳細や、製品の機能を検証するための試験結果が含まれます。
性能テストは、製品が設計通りの動作を実現できるかを確認する重要なプロセスです。テストは通常、顧客と合意した試験基準に基づいて実施され、その結果は承認のために提出されます。
この文書により、製品が量産時も同じ性能を維持できることを証明します。
車載カメラの具体例:ADAS(先進運転支援システム)用車載カメラにおける材料記録および性能テスト結果の例は以下の通りです:
- 材料試験結果
- 耐熱性試験:車載カメラの筐体に使用されるプラスチックが高温(125℃)でも形状や強度を維持できることを検証します。
- 試験方法: 熱負荷下での長時間耐久試験を実施。
- 結果報告: 材料が規定の熱歪み基準(±0.05mm以内)を満たしていることを確認。
- UV耐性試験:車載カメラのレンズ素材が長時間の紫外線曝露に耐え、光学性能が劣化しないことを確認します。
- 試験方法: 紫外線ランプで1000時間曝露し、透過率の変化を測定。
- 結果報告: 透過率が98%以上を維持していることを示します。
- 耐熱性試験:車載カメラの筐体に使用されるプラスチックが高温(125℃)でも形状や強度を維持できることを検証します。
- 性能テスト結果
- 光学性能試験:カメラレンズの解像度や視野角が設計値通りであるかを検証します。
- 試験方法: 実験室でターゲット画像を撮影し、解像度チャートで評価。
- 結果報告: 設計値(例:解像度1080p、視野角120°)が正確に達成されていることを確認。
- 防水試験:カメラ筐体がIP68規格を満たしていることを確認するための試験です。
- 試験方法: 水深1.5mで30分間の浸水試験を実施。
- 結果報告: 試験後、カメラ内部に水が侵入していないことを記録。
- 耐振動試験:車両運転中の振動がカメラに悪影響を与えないことを確認します。
- 試験方法: 振動台で1時間、周波数20Hz~2000Hzの振動を与える。
- 結果報告: レンズや基板にズレや破損がないことを確認。
- 光学性能試験:カメラレンズの解像度や視野角が設計値通りであるかを検証します。
- 化学的試験結果
- 材料成分分析:カメラ筐体やレンズの材料が有害物質(例:RoHS規制物質)を含んでいないことを確認します。
- 試験方法: ICP-MSやGC-MS分析装置を使用し、材料の成分を精密測定。
- 結果報告: 規定された成分濃度範囲を遵守していることを証明。
- 材料成分分析:カメラ筐体やレンズの材料が有害物質(例:RoHS規制物質)を含んでいないことを確認します。
- 耐環境性試験
- 温度サイクル試験
- 目的: カメラが極端な温度変化(-40℃~85℃)に耐えられることを確認する。
- 結果報告: 筐体や基板にひび割れがなく、性能が維持されていることを記録。
- 温度サイクル試験
意義とメリット
- 顧客の信頼を確保: 製品が顧客要求を満たしていることを科学的データで証明。
- 品質の一貫性を保証: 製造プロセス全体での品質保持に寄与。
- 不良削減とコスト最適化: 初期段階で潜在的な問題を発見し、大規模なリコールを防止。
これらの記録は、PPAPの承認に不可欠であり、高品質な車載カメラ製造の基盤を形成します。
11. 初期工程調査 (Initial Process Studies)
詳細説明:初期工程調査は、製品の製造工程が安定しており、品質基準を満たしていることを確認するためのプロセスです。これは主に工程能力指数(CpkやPpk)を計算して、製造工程が規定の範囲内で一貫した結果を出せることを示します。
Cpk(工程能力指数)は、製品特性が仕様の上限値(USL)と下限値(LSL)の間に収まり、その中心に近い分布を保っているかを評価します。
基準値として、通常1.33以上が要求され、これは99.73%以上の製品が仕様範囲内に収まることを意味します。特に安全性が重視される自動車部品では、この調査は欠かせない工程です。
車載カメラの具体例:ADAS用車載カメラにおける初期工程調査の具体例を以下に挙げます:
- レンズ組み立て工程の安定性確認
- 目的: レンズが正確な焦点距離で取り付けられ、カメラの視認性能を最大限発揮することを保証する。
- 実施内容: レンズ取り付け工程でサンプルをランダムに選び、焦点距離の測定結果を収集。
- Cpk計算:
- 規定値: 焦点距離 50±0.1mm
- サンプルの測定結果: 平均49.98mm、標準偏差0.02mm
- 計算結果: Cpk=1.67(基準値1.33を大幅に上回り、工程の安定性を確認)。
- 筐体の耐水性検査工程
- 目的: 防水仕様(例:IP68)を満たすことを保証する。
- 実施内容: 100個のカメラ筐体をランダムに選び、防水試験を実施。合格基準は内部水分侵入が0%であること。
- Ppk計算: 試験後の結果をもとに防水仕様の分布を分析。結果としてPpk=1.45が得られ、工程が安定していることを示す。
- 基板実装工程の不良率確認
- 目的: 電子基板上のはんだ付け品質が安定していることを証明する。
- 実施内容: 生産中のサンプルから、はんだ接合部の耐久性を引張試験で測定。
- 結果: サンプル中の不合格率0.5%以下を達成し、基準を満たしていることを確認。
- 光学性能テストの工程能力確認
- 目的: 視野角や解像度などの光学性能が設計通りであることを保証する。
- 実施内容: 視野角(設計値:120±1°)を測定し、工程能力指数を計算。
- Cpk計算結果: 視野角のCpk=1.50で、設計基準を十分に満たすことを示す。
意義とメリット
- 工程の信頼性を証明: 初期段階で製造工程が安定していることを証明し、顧客からの信頼を確保。
- 不良リスクの最小化: 工程内の潜在的な不良要因を早期に特定し、量産開始前に改善。
- コスト削減: 安定した工程により、不良率やリワークコストを削減。
初期工程調査は、車載カメラ製造のような精密製品の品質保証において非常に重要な役割を果たします。このプロセスを徹底することで、高い顧客満足度と市場競争力を維持することが可能です。
12. 試験所の資格の証明書 (Qualified Laboratory Documentation)
詳細説明:試験所の資格の証明書は、製品の試験や検査を実施する試験所が、顧客の要求に適合した適切な資格を保持していることを証明するための文書です。この証明書は、試験所の信頼性や試験結果の正確性を保証する役割を果たします。
一般的に、ISO/IEC 17025に準拠した認証が重要視され、国家レベルの認定や顧客の要件を満たすことが必須となります。
この証明書を提供することで、製品の検査データが客観的かつ信頼できるものであることを顧客に示し、承認プロセスの透明性を高めることができます。
車載カメラの具体例:車載カメラ(ADAS用)における試験所の資格証明書の具体例を以下に説明します。
- 防水試験の資格証明
- 試験内容: カメラ筐体の防水性能を試験。IP68規格を満たすことが要件。
- 試験所: ISO/IEC 17025認証を取得した試験所で試験実施。
- 資格証明書の内容: 試験所がIP68規格に準拠した検査プロセスを持ち、適切に校正された装置を使用して試験を行ったことを示す文書。
- 光学性能試験の資格証明
- 試験内容: 車載カメラの視野角、解像度、光透過率などの光学特性を検証。
- 試験所: ISO/IEC 17025認定の光学試験所で、特殊な検査機器(コリメータや分光計など)を使用して検証。
- 資格証明書の内容: 試験所が最新の光学測定技術に精通し、正確性と再現性を担保した環境で検査を実施したことを記載。
- 耐久試験の資格証明
- 試験内容: 振動、温度変化(-40℃~85℃)、湿度など、車載カメラが過酷な環境で性能を維持できるかを評価。
- 試験所: 国家認定を受けた環境試験施設での試験。
- 資格証明書の内容: 試験所が振動試験機、環境試験機を使用し、ISO規格に準拠した試験を実施したことを証明。
意義とメリット
- データの信頼性向上: ISO/IEC 17025認定試験所による試験は、国際的に信頼される品質基準に準拠していることを証明します。
- 顧客要求への対応: 試験所の資格証明書を提出することで、顧客が求める厳格な品質管理要件を満たしていることを明確化できます。
- 国際市場での競争力強化: 国際規格への準拠は、異なる国や地域の顧客に対応する際の競争力を高めます。
車載カメラのように安全性が重視される部品において、試験所の資格の証明書は、製品が顧客の期待に応え、国際基準を満たしていることを裏付ける重要な文書です。
この文書を通じて、品質への取り組みを顧客に伝え、承認プロセスをスムーズに進めることが可能となります。
参考:試験サイト 沖エンジニアリング ISO/IEC 17025認証
https://www.oeg.co.jp/ninshou/jab.html#emc
※ISO/IEC 17025認証サイトはHPなどに掲載されていますので、試験前に必ず確認するようにしてください
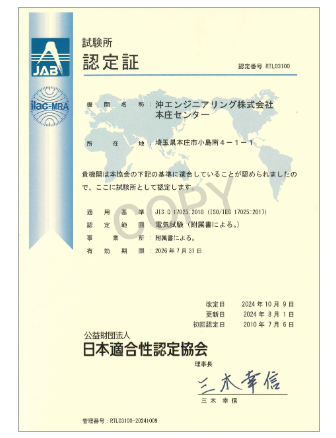
13. 外観承認レポート (Appearance Approval Report – AAR)
詳細説明:外観承認レポート(AAR)は、製品の外観が顧客の定める基準を満たしていることを証明するための文書です。
特に、自動車業界では外観が重要視される部品やシステムに適用され、車両全体の美観やブランドイメージに影響を与える要素が評価の対象となります。
評価は、製品の色合い、表面仕上げ、質感、形状の均一性などを含む詳細な外観特性に基づいて行われます。
AARは、製造された部品が設計や試作段階で合意された外観基準を維持していることを確認し、顧客の満足度を確保するための重要な工程の一つです。
車載カメラの具体例:ADAS用車載カメラにおける外観承認レポートの具体例を以下に示します。
- 筐体の色合いの一致
- 要件: カメラの筐体(外部ケース)の色が、車内インテリアや外装と一致していること。たとえば、車内のブラックトリムと完全に調和するマットブラックの仕上げが求められる場合があります。
- 評価方法: 標準化されたカラーマッチング照明環境下で、カラーチャートを用いて評価。結果をAARに記載。
- 表面仕上げの均一性
- 要件: 筐体の表面が滑らかで、均一な質感を持っていること。傷や変色がないことも確認対象。
- 評価方法: 目視検査と顕微鏡を用いた詳細な確認。AARには、検査基準、使用したツール、合格基準を含めて記載。
- 形状の一貫性
- 要件: カメラ筐体が設計通りの寸法と形状で製造されていること。外観要件として、エッジの滑らかさや成形時のバリがないことも含まれる。
- 評価方法: 三次元スキャナで形状を測定し、設計データと比較。結果をAARとして提出。
- 光沢と反射特性
- 要件: 筐体の光沢度が設計通りであること。特に、カメラの視野に影響を与えない反射特性を確保する必要がある。
- 評価方法: 光沢計や反射測定機器を使用して数値化。AARには測定値と基準値の比較結果を記載。
- 組み立て後の外観
- 要件: カメラを車両に取り付けた際の見栄えが、車両全体のデザインと調和していること。
- 評価方法: 車両に仮組みを行い、複数の角度から確認。顧客とともに実車レビューを実施し、その結果をAARに含める。
意義とメリット
- ブランドイメージの向上: 外観が一致していることで、車両全体の美観が保たれ、ブランド価値が向上します。
- 顧客満足度の向上: 外観における基準を満たすことで、顧客からのクレームを防ぎ、満足度を向上させます。
- トラブル防止: 生産初期段階で外観不良を特定し、後のトラブルやコスト増加を回避できます。
外観承認レポート(AAR)は、車載カメラの外観品質を保証し、車両デザインと調和させるための重要な要素です。
これを適切に実施することで、製品の完成度を高めるだけでなく、顧客の信頼を獲得する基盤を築くことができます。
14. 製造サンプル (Sample Production Parts)
詳細説明:製造サンプルとは、実際の製造工程で作られた部品や製品を指し、これを顧客に提出して品質や機能を確認してもらいます。
製造サンプルは、量産を開始する前に顧客の承認を得るために重要な役割を果たします。このプロセスでは、サンプルが製品の設計、仕様、機能要件を満たしているかを検証します。
提出するサンプル数や検査内容は、顧客の要求や製品の重要性に応じて決定されます。
また、製造サンプルは、製造プロセスが安定していることを示し、量産時にも同じ品質を維持できるかを確認するための指標となります。
車載カメラの具体例:ADAS用車載カメラにおける製造サンプルの具体的な取り扱い方法を以下に示します。
- 製造ラインでのサンプル作成
- 詳細: カメラ筐体、レンズ、基板などを設計通りに組み立て、製造プロセスに従って完成品を作成します。これには、精密な位置決めが必要なレンズ取り付けや防水試験を含むプロセスが含まれます。
- 目的: 実際の製造環境で作られたサンプルが、設計仕様通りであることを保証する。
- 顧客組み立てラインでの検証
- 詳細: 完成したカメラサンプルを顧客の車両組み立てラインに供給し、適合性をテストします。カメラの取り付けがスムーズであること、接続端子が車両の電子システムと適合していること、動作確認が行われます。
- 目的: 車両組み立て中に問題が発生しないことを確認し、実装可能性を評価する。
- 機能試験
- 詳細: 製造サンプルを使用して、カメラの解像度、視野角、焦点距離、夜間撮影性能などを検証します。また、ADASシステムとの連携テストも実施し、障害物検知や車線逸脱警報機能が正しく動作するかを確認します。
- 目的: 車両に組み込まれた際のカメラの性能を顧客が実際に評価する。
- 環境耐性テスト
- 詳細: 製造サンプルを使い、温度、湿度、振動、衝撃などの耐久性試験を実施します。これにより、車載カメラが極端な条件でも正常に動作することを証明します。
- 目的: カメラが車両の運用環境に適応できることを保証する。
- 不具合フィードバック
- 詳細: 顧客が製造サンプルを使用する際に発生した不具合について、詳細なフィードバックを提供。例えば、取り付け時のズレや電子接続の不具合などが報告される場合があります。これらの問題を解決するための改善が行われます。
- 目的: 最終量産に向けた品質向上と顧客満足の達成。
意義とメリット
- 量産前の品質保証: 製造サンプルの提出により、量産時に発生し得る問題を事前に特定し解決できます。
- 顧客信頼の構築: 実際の製造プロセスで作られたサンプルを通じて、製品が顧客の期待に応える品質を持っていることを示します。
- 改善の機会提供: 製造サンプルの評価を通じて、プロセスや製品の改善ポイントを発見し、量産体制の完成度を高めます。
製造サンプルの提出は、量産に移行するための重要なステップです。車載カメラにおいては、ADASシステムの機能や環境耐性が確認され、車両組み立て時の適合性が評価されます。
これにより、高品質な製品が顧客に提供され、長期的な信頼関係が構築される基盤となります。
15. マスターサンプル (Master Sample)
詳細説明:マスターサンプルとは、PPAP承認プロセス中に製造された製品を基準として保管するためのサンプルです。
このサンプルは、量産時において製品の基準を明確にし、一貫した品質を保証する役割を果たします。特に、製造工程の変更やトラブル発生時に、元の基準との比較を可能にする重要な資料となります。
保管するマスターサンプルは、製品設計、製造プロセス、測定結果が顧客承認を受けた時点のものと一致しています。
また、これらのサンプルは顧客やサプライヤーの工場で保管され、定期的な品質監査やトラブルシューティング時に利用されます。
車載カメラの具体例
- 製造時の基準カメラの選定
- 詳細: ADAS用車載カメラのマスターサンプルは、PPAP承認時に製造された製品から選定されます。このカメラは、解像度、視野角、耐久性、防水性能など、顧客が求めるすべての仕様を満たしている製品です。
- 目的: 量産時における基準となるカメラを確定し、品質のばらつきを防ぐ。
- マスターサンプルの保管
- 詳細: マスターサンプルは、保管条件に適合する専用の環境で保管されます。これには、温度や湿度の管理が含まれ、カメラの性能が劣化しないように配慮されます。
- 目的: 長期にわたって基準製品を維持し、品質比較の基準として活用する。
- トラブル時の比較検証
- 詳細: 量産中に発生した不具合が、設計や製造プロセスの変更によるものかを検証するため、マスターサンプルと比較します。例えば、カメラの焦点距離がズレた場合、マスターサンプルの測定結果と比較して原因を特定します。
- 目的: トラブル解決を迅速に行い、品質の安定性を確保する。
- 品質監査への使用
- 詳細: 顧客が定期的に実施する品質監査で、マスターサンプルが基準として利用されます。製造ラインで作られたカメラとマスターサンプルを比較し、品質が一貫していることを確認します。
- 目的: 顧客への品質保証と信頼関係の維持。
- 製造工程変更時の基準
- 詳細: 新しい製造工程や材料が導入された場合、これらの変更がマスターサンプルの性能と一致していることを確認します。例えば、筐体材質の変更後も、防水性能が基準値内であるかを検証します。
- 目的: 変更後の製品が基準と同等の品質を維持することを保証する。
意義とメリット
- 品質基準の明確化: マスターサンプルは、製品の基準を明確にし、量産時のばらつきを抑えるための重要なツールです。
- トラブルシューティング: 不具合発生時に基準サンプルと比較することで、原因特定を迅速化できます。
- 顧客信頼の維持: 顧客が求める品質基準を長期的に維持するため、マスターサンプルは重要な役割を果たします。
車載カメラにおけるマスターサンプルは、焦点距離、視野角、防水性能などのすべての仕様が基準を満たしていることを確認するために使用されます。
これにより、量産時の品質を一貫して保証し、トラブル発生時には迅速な問題解決を可能にします。
PPAPプロセスにおけるマスターサンプルは、製品品質の維持と顧客満足度向上の柱となる重要な要素です。
16. 検査具 (Checking Aids)
詳細説明:検査具は、製品の品質検査や測定に使用される専用の治工具、テンプレート、ジグなどを指します。これらは検査具リストや図面、写真などで詳細に管理され、製品の検査における正確性と一貫性を保証します。
また、検査具は製造ラインで使用されるため、精度維持のための定期的な校正や保守が求められます。さらに、これらの検査具がPPAPプロセスの一部として承認を受けることで、検査プロセス全体の信頼性を確保します。
車載カメラの具体例
- 光軸検査治具の設計と管理
- 詳細: 車載カメラでは、レンズの光軸が正確に設定されていることがADAS機能の精度を確保するために重要です。光軸検査治具は、レンズの中心軸が基準と一致しているかを確認するために設計されます。治具には、カメラを固定するクランプと基準軸を示すレーザーまたはマーカーが備わっています。
- 目的: 検査具の使用により、量産時でも一貫した光軸の調整が可能になります。
- 筐体寸法検査用テンプレート
- 詳細: カメラ筐体の寸法が設計図面に基づいて正確であるかを確認するため、専用のテンプレートが使用されます。例えば、カメラの取り付け面の平坦性やネジ穴の位置をチェックするための専用ゲージが利用されます。
- 目的: 寸法誤差を防ぎ、車両への適合性を確保します。
- 校正とメンテナンス記録
- 詳細: 検査具は定期的に校正され、その結果が記録として保存されます。例えば、光軸検査治具のレーザー発信器の位置が基準からズレていないかを確認し、必要に応じて調整を行います。
- 目的: 校正記録の管理により、検査具の精度と信頼性を長期間維持します。
- 環境試験用治具
- 詳細: 車載カメラが耐環境性能を満たすことを確認するために、耐熱、耐寒、振動試験用の専用治具が使用されます。例えば、防水試験では、カメラを固定し、一定の水圧で試験するための専用設備が使用されます。
- 目的: 実使用環境での性能を保証するための検査プロセスを支援します。
- 検査具の変更履歴管理
- 詳細: 検査具が変更、修理、または改造された場合、その履歴が記録されます。例えば、レンズ光軸検査治具のクランプ部分を改良した場合、その変更内容と理由、実施日を記録します。
- 目的: 変更による品質への影響を防ぎ、追跡可能性を確保します。
意義とメリット
- 一貫した品質検査: 検査具を適切に管理し、定期的に校正することで、検査の精度と信頼性を確保します。
- トラブル防止: 設計変更や治具の不具合に迅速に対応し、不良品の発生を最小限に抑えます。
- コスト削減: 検査具を効率的に利用することで、品質トラブルや再検査に伴うコストを削減します。
車載カメラの検査具は、光軸調整や筐体寸法確認、防水性能試験など多岐にわたる検査に不可欠なツールです。これらの検査具の精度と管理が、製品の品質保証を支える基盤となります。
PPAPプロセスにおける検査具の適切な管理と記録は、品質トラブルの防止と顧客信頼の維持に直結します。
17. 顧客固有要求事項 (Customer-Specific Requirements)
詳細説明:顧客固有要求事項は、特定の顧客が製品やプロセスに対して独自に設定した要件を満たすために必要な書類や仕様を指します。これらの要求事項は、PPAPの標準資料に含まれない場合がありますが、顧客が品質、設計、供給において重視する事項を反映したものです。
具体的な書類として、包装仕様書、輸送テスト結果、製造ラインの詳細なレイアウト図などが含まれます。顧客固有要求事項を正確に把握し対応することは、顧客との信頼関係を構築し、製品承認プロセスを円滑に進める上で重要です。
車載カメラの具体例
- 包装仕様書の要求
- 詳細: 車載カメラは非常に繊細な部品であるため、輸送中の振動や衝撃から守る専用の包装が必要です。顧客固有の要求として、特定の発泡材や仕切りを使用した包装仕様書が求められることがあります。
- 例: ADAS用カメラを保護するために、高密度のフォーム材と個別仕切りを採用した包装仕様書が顧客から指定されます。この包装仕様書には、カメラの収納位置、輸送中の衝撃試験結果、再利用可能な梱包材の使用についての指示が含まれます。
- 輸送テスト結果の提出
- 詳細: 製品が顧客の施設まで安全に輸送されることを保証するために、輸送中の振動や衝撃に耐える性能を確認するテスト結果が求められます。
- 例: 車載カメラを模擬輸送条件(道路の凹凸や長距離輸送)で振動テストを実施し、包装材が十分にカメラを保護していることを証明します。この結果をレポートとして顧客に提出します。
- 製造ラインの詳細レイアウト図
- 詳細: 顧客が製造工程の透明性を確保するために、製造ラインのレイアウト図や設備配置図を要求する場合があります。
- 例: カメラの製造工程を示すレイアウト図には、レンズ取り付け、光学特性測定、防水テストの各ステーションの配置が含まれます。顧客はこれをもとに生産能力や品質管理体制を評価します。
- トレーサビリティシステム
- 詳細: 製品のトレーサビリティを確保するために、各カメラに個別のシリアル番号を付与し、製造から出荷までのデータを追跡可能にすることが求められる場合があります。
- 例: 車載カメラにレーザー刻印されたシリアル番号と、製造日、テスト結果、使用された部品ロット番号をデータベースに記録し、顧客がいつでも参照できるようにします。
- 環境試験要求
- 詳細: 特定の顧客は、製品が厳しい環境条件に耐えられることを証明する追加試験を求めることがあります。
- 例: カメラの使用地域が極寒地である場合、-50℃の低温環境下での動作確認試験を実施し、その結果を顧客に提出します。
意義とメリット
- 顧客満足度の向上: 特定の要求を満たすことで、顧客の信頼を獲得し、長期的な取引関係を構築できます。
- トラブル回避: 顧客の期待を超える対応を行うことで、納品後のクレームやトラブルを防ぐことができます。
- 競争優位性の確立: 顧客固有の要求に柔軟に対応することで、競合他社との差別化が可能になります。
顧客固有要求事項は、標準的なPPAP項目の枠を超えた独自の要件であり、車載カメラのような高性能部品において特に重要です。
これらの要求事項を詳細に理解し、適切な対応を行うことは、顧客満足度の向上だけでなく、自社の信頼性や市場での競争力を高めることにつながります。
18. 部品提出保証書 (Part Submission Warrant – PSW)
詳細説明:部品提出保証書 (PSW) は、製造した部品が顧客の要求仕様およびPPAPのすべての項目を満たしていることを証明する文書です。
この書類には、製品の詳細、製造条件、試験結果などの要約情報が含まれています。また、顧客への正式な提出の一部として、承認を得るための最終確認書類となります。
PSWは、製品の品質、適合性、生産プロセスの管理が保証されていることを示します。PPAPプロセスにおける最終的な合意書ともいえる重要な役割を果たします。
車載カメラの具体例
- 製品の基本情報
- PSWには、ADAS用車載カメラの製品名称、部品番号、設計図番号が記載されます。これにより、顧客は提出された文書がどの部品に対応しているかを一目で確認できます。
- 具体例: 車載カメラ「ADASCam-2025」の部品番号「CAM-00123」と設計図番号「DR-45678」が記載されます。
- 製造条件の記載
- 製品がどの製造条件下で作られたかを明記します。これは生産ライン、使用した治具、加工プロセスの詳細を含みます。
- 具体例: 車載カメラが工場のライン3で、特定のレンズ組み立て治具を使用し、1,000ルクスの照明下で組み立てられたと記載します。
- 品質保証の確認
- 寸法、材料、性能などがすべて設計要件に適合していることを示します。この情報は、他のPPAP資料(寸法検査結果、性能テスト結果など)を要約した形で記載されます。
- 具体例: カメラの総重量(200g ± 5g)、材料構成(筐体: アルミニウム、レンズ: 高強度プラスチック)がPSWに記載され、要求仕様を満たしていることが確認されます。
- 試験結果の要約
- これまでに行われた耐久試験、防水試験、振動試験などの結果がPSWに簡潔にまとめられます。
- 具体例: 「カメラは-40℃~85℃の動作環境下で動作確認済み。IP68の防水規格に準拠」などの試験結果が記載されます。
- 承認責任者の署名
- PSWには、製造責任者や品質保証責任者の署名が必要です。これにより、提出された製品が自社内で適切に評価され、責任を持って保証されていることを示します。
- 具体例: 工場の品質責任者が「John Doe」として署名し、顧客との信頼を確立します。
意義とメリット
- 顧客との合意形成: PSWは、製品の品質と適合性に対する顧客との最終的な合意を確立します。
- トレーサビリティの向上: PSWには製造条件や試験結果が記載されるため、問題発生時の原因追及が容易になります。
- 信頼性の証明: この書類を通じて、製品が顧客の期待を満たしていることを保証できます。
部品提出保証書 (PSW) は、PPAPプロセスを締めくくる重要な書類です。特に車載カメラのような高精度製品では、PSWを通じて全体的な品質と性能を保証し、顧客の信頼を獲得することができます。
すべての要件を正確に記載し、顧客に提出することで、円滑な製品承認プロセスを実現します。
PPAPの18項目を車載カメラで実践する重要性
ADASのような安全性が求められる技術では、これらの項目すべてが品質保証の基盤となります。それぞれの項目を適切に準備することで、製品の信頼性を高め、顧客の期待に応えることができます。
各項目を的確に理解し、対応することが、成功するPPAP承認プロセスの鍵です。
PPAPの工程と審査プロセスをスムーズに進める方法
PPAP (Production Part Approval Process) の工程は、設計承認から最終製品審査までの一連のステップを含みます。このプロセスをスムーズに進めるためには、以下のような体系的なアプローチと事前準備が必要です。
PPAP工程のステップ
- 設計承認 (Design Approval):製品設計が顧客の要求を満たしていることを確認します。
- 車載カメラの例: ADAS用カメラの設計図が視野角、焦点距離、解像度などの性能要件を満たしているかを承認。
- 試作とテスト (Prototyping and Testing):試作段階で部品やプロセスの検証を行い、設計通りの性能が得られることを確認します。
- 車載カメラの例: 防水性能(IP68)や耐振動性能を評価する試験を実施し、その結果を顧客に共有。
- 製造準備 (Production Readiness):工程フロー図や工程FMEA、コントロールプランを作成し、製造プロセスが安定していることを示します。
- 車載カメラの例: レンズの組み付け工程や基板の実装工程を詳細に記載した工程フロー図を準備。
- 量産試作 (Pilot Production):実際の生産設備を用いて少量生産を行い、製造能力を確認します。
- 車載カメラの例: 量産設備で製造したカメラの品質が設計要件を満たしているかを確認。
- 最終審査 (Final Approval):PPAPの18項目を顧客に提出し、すべての要件が満たされていることを確認します。
- 車載カメラの例: PSW (部品提出保証書) に総重量や材料構成を記載し、顧客に提出。
審査プロセスをスムーズに進める方法
- 事前準備の徹底:PPAP文書を早期に完成させ、試作段階で得られた結果を正確に反映します。
- ポイント: 試験結果、設計FMEA、工程FMEAを事前に見直し、不備がないことを確認。
- 顧客との定期的なコミュニケーション:進捗状況を定期的に顧客に報告し、仕様や要件の変更があれば迅速に対応します。
- 車載カメラの例: 顧客が求める特定の耐久試験(例: 1,000時間の動作テスト)について事前に合意。
- 文書の整備と見やすさ:提出文書は整理され、分かりやすく記載されていることが重要です。
- アクション: 工程フロー図は製造プロセスを可視化し、簡潔な注釈を付けることで説明が容易になります。
- チーム間の連携強化:製造、品質、設計の各チームが連携し、全員がPPAPの進行状況を把握している状態を維持します。
- 車載カメラの例: 製造チームが生産設備の能力を評価し、品質チームが測定システム解析(MSA)の結果を提供。
- 顧客審査でのプレゼンテーション力:顧客審査では、製品とプロセスの信頼性を視覚的に示すことが重要です。
- 具体例: 防水試験や振動試験の映像を用意し、顧客に実証する。
成功するための秘訣
- 早期提出とフィードバックの活用:試作段階でのテスト結果を早期に提出し、顧客からのフィードバックを反映します。
- 例: カメラの取り付け位置や動作特性に関する顧客の意見を製品設計に反映。
- 計画と管理の徹底:プロジェクト管理ツールを活用し、各工程の進捗をモニタリングします。
- アプローチ: ガントチャートで納期を明確にし、遅延リスクを最小化。
PPAPの工程と審査プロセスをスムーズに進めるためには、事前準備、顧客との連携、そして綿密な計画が不可欠です。車載カメラの製造においては、設計から審査までの各段階で品質を保証するための取り組みが、顧客からの信頼を築き、ビジネスの成功につながります。
PPAP製造で品質と信頼性を高めるための要点
本記事のまとめを以下に列記します。
- PPAPは製造品質を保証する国際的なプロセスである
- 顧客の要求を満たすことがPPAP製造の基本である
- 設計、製造、品質管理を統合的に検証する手法である
- IATF16949規格の枠組みで採用される品質基準である
- 試作から量産までの品質確認がPPAP製造の目的である
- 車載カメラのような精密部品で特に重要性が高い
- 工程FMEAで潜在的なリスクを特定し改善する
- 測定システム解析で検査の信頼性を高める
- 顧客固有要求に対応する柔軟なプロセスが求められる
- 初期工程調査で製造プロセスの安定性を確認する
- 部品提出保証書(PSW)は顧客承認の要である
- マスターサンプルは品質基準を示す重要な指標である
- 視覚的な資料で顧客審査を円滑に進める工夫が必要である
- 製造サンプルは品質と機能を実証する鍵となる
- 顧客とのコミュニケーションが成功の基盤である
コメント