「IATF16949 ISO9001 違い」と検索している方へ、この記事では両規格の特徴や違いについて詳しく解説します。
IATF16949は自動車産業に特化した品質マネジメント規格であり、ISO9001は幅広い業種で採用される品質管理の基盤となる国際規格です。この2つの規格は、品質向上を目的としながらも適用範囲や要件に大きな違いがあります。
この記事では、IATF16949の特徴、ISO9001との相違点、そして自動車業界での重要性についてわかりやすく説明しています。
品質管理のプロセスを理解したい方や、規格導入を検討している企業の方にとって役立つ内容となっていますので、ぜひご一読ください。
- IATF16949とISO9001の基本的な違い
- IATF16949が自動車産業に特化している理由
- ISO9001が多業種で活用される汎用性
- 両規格を導入する際の注意点と利点
- IATF 16949とは?初心者向けの基本解説と ISO9001との違い
- IATF 16949で求められる7つの原則
- IATF16949を実現するための基本要素
- IATF 16949の初心者向け5コアツールの解説
- IATF 16949初心者向け導入ステップ
- 初心者が陥りやすいポイントと回避策
IATF 16949とは?初心者向けの基本解説と ISO9001との違い
IATF 16949は、自動車産業向けに特化した品質マネジメントシステムの国際規格です。ISO 9001を基盤とし、自動車産業特有の要件を加えることで、製品やプロセスの品質向上を目指しています。
この規格の導入は、顧客満足度の向上、品質不良の削減、競争力の強化を促進する一方で、厳格な管理基準や初期投資の負担といった課題も伴います。
本記事では、IATF 16949の概要や対象業界、ISO 9001との関係、導入メリットとデメリット、認証取得の具体的な流れを詳しく解説し、品質マネジメントシステムの成功事例や実務での応用方法についても掘り下げます。
導入を検討する企業にとって、実践的な指針となる内容を提供します。
IATF 16949の概要と目的
IATF 16949は、自動車産業向けの品質マネジメントシステムの国際規格です。この規格は、製品やプロセスの品質を高めると同時に、顧客満足度を向上させることを目的としています。具体的には、設計や開発、製造、インストール、サービスにおける品質管理を体系的に実現するための基準を提供しています。
その中で特に重視されるのが、プロセスアプローチや継続的な改善、リスクベース思考です。これらは、組織が安定した品質を維持しながら、顧客の要求に応え、競争力を高めるために不可欠な要素とされています。これにより、自動車業界におけるグローバルな品質基準の統一が図られています。
また、この規格は単なる品質管理の枠を超え、顧客要求や法規制への適合、さらに環境や安全に配慮した管理体制を築くことも目的の一つとしています。
IATF 16949が適用される業界と対象
IATF 16949は主に自動車産業において適用される規格です。その対象は、自動車メーカーだけでなく、部品や材料を供給するサプライヤーにも広がっています。具体的には、車両部品、エンジン、電装品、さらにはソフトウェア開発を行う企業も対象となります。
この規格の適用範囲には、製造工程だけでなく、設計・開発や物流、さらには顧客へのサービス提供も含まれます。
IATF 16949が適用される業界と対象
IATF 16949は主に自動車産業に特化した規格で、その適用範囲は非常に広範囲に及びます。以下は、具体的な対象業界とその活動内容について詳しく説明します。
●自動車メーカー(OEM):自動車メーカー、いわゆるOEM(Original Equipment Manufacturer)は、IATF 16949の主要な対象です。これには、乗用車や商用車、バス、トラック、特殊車両を製造する企業が含まれます。OEMは、サプライヤーとの連携を通じて一貫した品質管理を実現する必要があり、この規格を導入することで顧客満足度の向上を目指します。
●自動車部品サプライヤー:部品サプライヤーは、自動車メーカーに部品やコンポーネントを提供する企業を指します。対象となる部品には、エンジン、トランスミッション、ブレーキシステム、サスペンション部品、タイヤ、シート、内装品などがあります。特に、安全部品や耐久性が求められる部品を供給する企業にとって、この規格の遵守は欠かせません。
●電装品・エレクトロニクス関連企業:近年の自動車産業では、電装品や電子システムが重要な役割を果たしています。センサー、カメラシステム、ECU(エンジンコントロールユニット)、バッテリーマネジメントシステム(BMS)などを製造する企業は、この規格を導入することで、信頼性の高い製品を市場に提供することができます。
●ソフトウェア開発企業:自動車のデジタル化が進む中で、ソフトウェア開発もIATF 16949の対象範囲に含まれます。自動運転技術、車載インフォテインメントシステム、車両制御システムなどのソフトウェアを開発する企業は、品質管理だけでなく、セキュリティや耐久性にも対応する必要があります。
●材料サプライヤー:自動車産業では、鋼材、アルミニウム、プラスチック、ゴム、複合材料などの供給も重要な要素です。これらの材料を供給する企業も規格の適用対象となり、一定の品質を確保するための管理体制が求められます。
●物流・サービス業者:IATF 16949は、製造プロセスだけでなく、物流やサービス業者にも適用されます。部品や完成車の輸送、倉庫管理、納品サービスを行う業者も品質管理体制を整えることで、顧客満足度の向上に寄与できます。
適用外のケース
IATF 16949は、自動車産業に直接関連しない業界には適用されません。例えば、一般的な製造業(食品、繊維など)やサービス業(旅行業、金融業など)は対象外です。
しかし、この規格で定められた品質管理のアプローチや考え方は、他業界でも品質向上の参考にすることが可能です。
IATF 16949は、自動車産業の全てのプロセスに統一された品質基準を提供し、製品の安全性と信頼性を確保することを目的としています。
自動車メーカーから部品サプライヤー、物流業者、さらにはソフトウェア開発企業まで、多岐にわたる対象企業がこの規格を導入することで、競争力を高めることができます。一方で、適用範囲を超えた業界でも、この規格を参考にして品質向上を図ることが可能です。
IATF 16949の歴史とISO 9001との関係
IATF 16949は、自動車産業に特化した品質マネジメントシステム規格で、その基盤となっているのはISO 9001です。この関係性は、IATF 16949を理解する上で非常に重要です。
ISO 9001を基盤にした規格設計
ISO 9001は、あらゆる業界に適用可能な汎用的な品質マネジメントシステム規格で、プロセスアプローチや継続的改善、顧客満足の向上を基本原則としています。
一方、IATF 16949は、ISO 9001の基本的なフレームワークをベースにしており、さらに自動車産業特有の要求事項を追加した規格です。このため、ISO 9001に準拠することが、IATF 16949の実施において不可欠な第一歩となります。
ISO 9001との共通点と追加要件
IATF 16949には、ISO 9001の要求事項が全て含まれています。例えば、プロセスアプローチや顧客満足度の向上、リスクベース思考などの原則は両規格で共通です。しかし、IATF 16949では、以下のような自動車産業特有の要求事項が追加されています。
- 製品安全管理: 製品安全責任者の任命と、設計段階からの安全対策。
- サプライヤー管理: サプライヤーの品質マネジメントシステム開発や監査。
- トレーサビリティ: 部品や材料の追跡可能性を保証し、不良発生時に迅速な原因追及を可能にする仕組み。
- 顧客固有の要求事項(CSR): 各自動車メーカーの特定の要件に対応するプロセス。
これらの追加要件により、自動車産業における高度な品質基準を満たすことが可能となります。
IATF 16949誕生の背景
ISO 9001のフレームワークが十分に有用である一方で、自動車産業は特有の課題を抱えていました。各地域やメーカーが独自の品質基準を採用していたため、サプライチェーン全体で品質管理の一貫性が欠けていたのです。
この問題を解消するために、1999年にISO/TS 16949が誕生しました。そして、2016年にはISO 9001:2015の改訂に伴い、ISOから独立した形でIATF 16949として再編されました。
以下は、IATF 16949とISO 9001の具体的な相違点を挙げた比較表です。自動車産業特有の要件がどのようにISO 9001をベースに発展しているかを具体例とともに示します。
項目 | ISO 9001 | IATF 16949 |
---|---|---|
対象業界 | 製造業、サービス業を含むあらゆる業界を対象。 | 自動車産業専用。OEM(自動車メーカー)や部品・材料サプライヤーに適用される。 |
基本コンセプト | プロセスアプローチとリスクベース思考を重視。 | ISO 9001の基盤に加え、自動車産業特有の課題(例:製品安全やトレーサビリティ)に対応する規定が追加。 |
サプライヤー管理 | サプライヤー評価やモニタリングを一般的な範囲で規定。 | サプライヤーの品質マネジメントシステム開発が求められる。ISO 9001認証取得を最低条件とし、IATF 16949準拠が最終目標とされる。 |
コンティンジェンシープラン | 必須ではないが、必要に応じて策定。 | 自然災害や設備故障などのリスクに対する計画を明示的に要求。生産停止が発生した際には、代替手段や復旧計画を迅速に実行する必要がある。 |
監査要件 | 内部監査を規定し、シンプルな審査が行われる。 | 製造プロセス監査、製品監査、シフト交代時の管理状況を含む多層的な審査が要求される。また、顧客要件に基づいた監査も義務付けられる。 |
品質記録の管理 | 重要な記録を保持し、品質管理に役立てることを推奨。 | PPAP(生産部品承認プロセス)やFMEA(故障モード影響分析)の記録を必須とし、顧客からの承認を得るまで詳細な記録を保持する必要がある。 |
製品安全 | 特定の安全要件は規定されていない。 | 製品安全に関する責任者の任命が義務化され、設計段階から安全性を確保するプロセスを導入。サプライチェーン全体で安全性を共有し、管理する必要がある。 |
トレーサビリティ | 要求される場合のみ対応可能。 | 製品のシリアル番号や製造ロット情報を追跡可能にすることが必須。これにより、不具合が発生した際の原因追跡と迅速なリコール対応が可能となる。 |
継続的改善 | 継続的な品質向上を促進する要求を規定。 | 不適合が発生した場合、迅速な是正措置と根本原因分析を行い、記録を残すことを義務化。顧客クレームの分析も継続的改善プロセスの一部として組み込まれる。 |
ポイント
- 対象業界の違い: ISO 9001は汎用規格であり、IATF 16949は自動車産業に特化していることを強調。
- 実例を通じた比較: 例えば「コンティンジェンシープラン」や「製品安全」に関する具体例を盛り込むことで、初心者でも理解しやすい内容に。
- プロセスの具体的な要求: FMEAやPPAPなどの自動車産業特有のプロセスを例示。
IATF 16949はISO 9001をベースに、自動車産業の厳しい要件に対応する形で進化した規格です。この表を通じて、ISO 9001とIATF 16949の違いが明確になり、それぞれの特徴や適用範囲を具体的に理解できます。
IATF 16949導入のメリットとデメリット
IATF 16949を導入することで、組織にはさまざまなメリットがあります。IATF 16949導入のメリットとデメリット
IATF 16949を導入することで得られる効果は多岐にわたりますが、同時にデメリットや注意点も存在します。以下に、具体的なメリットとデメリットを表形式で比較しながら説明します。
項目 | メリット | デメリット |
---|---|---|
顧客信頼の向上 | 国際的な品質基準を満たすことで、顧客からの信頼が向上し、新規ビジネスの獲得や既存顧客との関係強化が可能。 | 顧客要求を満たすために新しいプロセスや設備を導入する必要があり、初期投資が増加。 |
品質不良の削減 | 不良品やリコールの発生を未然に防ぐ仕組みを構築できるため、品質コストの削減に繋がる。 | 不良削減のためのプロセス改良やトレーニングに多大な時間と費用がかかる場合がある。 |
内部プロセスの効率化 | プロセスの標準化や継続的改善により、業務効率が向上し、結果として全体的な生産性が上がる。 | プロセス変更に伴う現場スタッフやマネジメントへの負担が一時的に増加する可能性がある。 |
サプライチェーンの強化 | サプライヤー管理の強化により、調達から製造までの全体的なプロセスが安定し、納期や品質に関するトラブルが減少する。 | サプライヤーにもIATF 16949準拠を求める場合があり、協力を得るのに時間がかかることがある。 |
競争力の向上 | 規格準拠により、グローバル市場での競争力が強化され、海外企業との取引や新規市場への参入がスムーズに進む。 | 導入コストの負担が中小企業にとって特に大きく、短期的には競争力が低下するリスクがある。 |
メリットの具体例
1. 顧客信頼の向上:大手自動車メーカーとの取引条件で「IATF 16949の認証取得」が必須となっている場合があります。この認証を取得することで、新規の受注やプロジェクト参入の可能性が広がります。
2. 品質不良の削減:FMEA(故障モード影響分析)などを活用して設計段階でリスクを特定し、対策を講じることで、不良品の発生を抑制できます。結果として、顧客からのクレームやリコール対応が減少します。
3. 内部プロセスの効率化:プロセスフローや制御計画の整備によって、各部門間のコミュニケーションが円滑になり、業務の効率性が向上します。これにより、生産リードタイムの短縮やコスト削減が実現します。
デメリットの具体例
1. 導入コストの増加:IATF 16949の導入には、コンサルタント費用、トレーニング費用、システム導入費用、そして監査費用など、多くの初期投資が必要です。特に、中小企業ではこれらの費用負担が大きく、導入に向けた予算の確保が課題となる場合が多いです。さらに、長期的な認証維持にもコストがかかるため、事前に十分な計画を立てる必要があります。
2. プロセス変更の負担:新しいプロセスや手順を導入する際、従業員の抵抗や混乱が生じる場合があります。現場スタッフにとっては新しい手順やルールの理解に時間がかかり、生産性の一時的な低下が見られることがあります。また、トレーニング不足やコミュニケーションの欠如が原因で、誤解や誤操作が発生するリスクも高まります。これを防ぐには、徹底したトレーニングと意識向上活動が不可欠です。
3. 管理負担の増加:IATF 16949では、品質マネジメントシステムの継続的な改善と認証維持が求められます。そのため、日々の運用において記録の作成やデータ管理、内部監査の実施などが必要となり、管理負担が増加します。特に、小規模な組織では、専任の担当者がいない場合に現場スタッフの負担が大きくなることがあります。これにより、本来の業務に集中する時間が減少し、短期的には効率が低下する可能性も考えられます。
4. サプライヤーへの影響:IATF 16949を導入することで、自社だけでなく取引先であるサプライヤーにも一定の品質管理基準を求める必要があります。特に、小規模なサプライヤーにとってはこれが負担となり、取引先との協力体制に影響を及ぼす場合があります。場合によっては、サプライヤーの変更を余儀なくされることもあり、これがコスト増加や供給リスクに繋がる可能性があります。
5. 柔軟性の低下:IATF 16949の厳格なルールと手順に従う必要があるため、業務上の柔軟性が低下する場合があります。特に、急な仕様変更や顧客からの特別な要求に対して、すぐに対応できないことがある点が課題です。このため、顧客ニーズに迅速に応える柔軟性と、規格の遵守を両立させる工夫が求められます。
IATF 16949の導入は、短期的な負担やコストを伴うものの、長期的には大きなメリットをもたらします。特に、自動車産業における競争力強化や顧客満足度の向上が期待できるため、多くの企業がこの規格を採用しています。一方で、導入に伴うリソースや初期投資の負担を正確に見積もり、計画的に進めることが成功の鍵です。
IATF 16949認証取得の流れ
IATF 16949の認証取得は、主に以下の手順で進められます。
- 準備と計画
組織の現状を分析し、必要な改善点を特定します。また、認証取得のためのプロジェクトチームを編成し、計画を立案します。 - 文書化とシステム構築
規格に基づいた品質マネジメントシステムを構築し、その文書化を進めます。これには、手順書や業務フローの作成が含まれます。 - 内部監査と改善
構築したシステムを試運用し、内部監査を実施します。その結果を元に、不適合箇所を修正し、システムを最適化します。 - 第三者審査
認証機関による審査が行われます。ここでは、システムの有効性や適合性が評価されます。 - 認証取得と維持
審査を通過すると、認証が発行されます。その後も定期的な更新審査を受け、システムを継続的に維持・改善することが求められます。
この流れを通じて、組織は国際的な品質基準を満たし、競争力を高めることができます。
IATF 16949で求められる7つの原則
IATF 16949は、自動車産業向けの品質マネジメントシステム規格で、競争力のある製品を提供するための体系的なアプローチを提供します。
その中心となる7つの原則は、顧客重視、プロセスアプローチ、継続的改善、リスクベース思考、リーダーシップ、エビデンスに基づく意思決定、そしてサプライチェーンの有効な管理です。
これらの原則は、カメラ設計の具体例を通じて、どのように製品の品質と信頼性を高めるかを実践的に説明できます。
本記事では、IATF 16949の各原則がカメラ設計にどのように適用され、顧客満足度向上や競争力強化に寄与するかを具体例を交えて解説します。
さらに、リスクや課題への対応策も含め、IATF 16949を導入する企業にとって有益な情報を提供します。
顧客重視と顧客満足の向上
顧客重視はIATF 16949の基本原則の一つであり、顧客の期待や要件を的確に理解し、それに応える製品やサービスを提供することを目的としています。顧客満足度を向上させるためには、定期的な顧客フィードバックの収集とその分析が不可欠です。
具体例(カメラ設計の場合)
自動車向けカメラの設計において、顧客の声を反映することが重要です。例えば、ある自動車メーカーが「ナイトビジョン性能を向上させたい」という要求を出した場合、設計チームは次のような具体的な対応を行います:
- 顧客の期待を定義
ナイトビジョン性能の具体的な要件を詳細に確認します(例:最低光量0.1ルクスで鮮明な画像を撮影可能にする、赤外線対応の必要性など)。 - フィードバックの活用
過去に提供したカメラ製品に対する顧客フィードバックを収集し、問題点(例:暗所でのノイズの多さ、遅延)を改善案に組み込みます。 - 試作段階での実地テスト
設計段階で試作品を作成し、顧客が指定する実環境(例:夜間の高速道路やトンネル内)でテストを実施。結果をもとにさらなる調整を行います。 - 品質の安定性を確保
製品の品質を維持するため、カメラレンズやセンサーの部品を慎重に選定し、製造工程での不良品発生率を最小化する仕組みを導入します。
顧客クレームへの迅速な対応
例えば、顧客から「一定の条件下でカメラ映像がぼやける」というクレームが寄せられた場合、即座に調査チームを編成し、問題の原因を特定します。たとえば、温度変化によるレンズの曇りが原因だった場合には、耐候性を向上させるコーティングを追加する設計変更を行い、早急に改善した製品を提供します。
バランスの取れたアプローチの重要性
顧客の要求に偏りすぎると、設計や製造コストが高騰し、最終的に収益性を損なうリスクがあります。例えば、すべての顧客が異なるスペックを要求した場合、それに全て応えることは現実的ではありません。そのため、顧客の要件を標準化し、共通の仕様で効率的に対応する方法を採用します。
顧客重視の姿勢は信頼関係の構築に繋がりますが、それを実現するには現実的かつ持続可能な方法を採用することが重要です。特に、自動車向けカメラのような技術的要素が強い製品では、顧客の期待に応えると同時に、組織のリソースを効率的に活用する戦略が求められます。
プロセスアプローチの重要性
プロセスアプローチの重要性(カメラ設計における具体例を含む)
プロセスアプローチとは、組織内の全ての活動をプロセスとして捉え、それらを効果的に管理する方法です。これにより、各プロセス間の連携が強化され、全体的な効率と品質が向上します。
カメラ設計における具体例
自動車用カメラの設計において、プロセスアプローチを適用することで、開発から製造までの一貫性が確保されます。以下に具体的な活用例を示します:
- 設計プロセスとテストプロセスの連携
カメラ設計の初期段階で、夜間視認性や防水性能などの要求仕様を明確にし、それを製造・テストプロセスと連携させます。例えば、試作段階で防水テストを行い、その結果を設計にフィードバックすることで、改良を迅速に進めることができます。 - 部品選定プロセスの標準化
カメラモジュールに使用するレンズやセンサーなどの部品選定プロセスを標準化し、サプライヤー管理プロセスとも連携させます。これにより、高品質な部品を安定的に調達でき、不良率の低減が期待されます。 - 製造プロセスと品質管理プロセスの統合
製造ラインでの自動検査装置を導入し、カメラの解像度や焦点調整の精度をリアルタイムで検査する仕組みを構築します。このデータを品質管理プロセスに反映することで、不具合の根本原因を特定し、プロセス改善に活用します。
プロセスのパフォーマンス指標の設定
例えば、カメラの初期不良率を1%以下に抑えるという目標を設定し、これを達成するためのプロセス指標(部品検査通過率、製造ラインの停止頻度など)を明確にします。これらの指標をモニタリングすることで、問題が発生した際に迅速な対応が可能になります。
プロセスアプローチを効果的に導入するための取り組み
- 従業員教育
カメラ設計・製造に関わる全ての従業員に、プロセス間の関係性や重要性を理解してもらう教育プログラムを提供します。 - プロセスの可視化
設計から製造、出荷までの全プロセスをフローチャートやデジタルツールで可視化し、関係者が全体像を共有できる仕組みを導入します。
プロセスアプローチを導入することで、カメラ設計から製造までの各段階が効率的かつ一貫して管理され、品質の向上とコスト削減が期待できます。一方で、従業員教育やプロセスの見える化などの初期投資も必要であるため、綿密な計画と実行が重要です。
継続的改善の推進
継続的改善は、IATF 16949の中核的な考え方であり、製品やプロセスの品質を向上させ、顧客の信頼を得るために重要です。特にカメラ設計では、高度な技術と精密性が求められるため、継続的な改善が競争力の強化に直結します。
具体例:カメラ設計での継続的改善の取り組み
- レンズ設計の最適化 カメラの画質を向上させるため、レンズの設計を見直す取り組みが挙げられます。例えば、光学シミュレーションツールを活用して、光の収差や歪みを分析・最小化することで、高精度なレンズ設計を実現します。この改善により、夜間や逆光でも鮮明な画像が得られるようになります。
- センサー技術の更新 カメラの性能はセンサー技術に大きく依存します。従来のCMOSセンサーを改良し、暗所撮影性能を向上させるために、裏面照射型センサー(BSIセンサー)の採用を進める事例があります。これにより、低照度環境でもノイズが少なく、明るい映像を提供できます。
- AI技術の統合 継続的改善の一環として、カメラ設計にAI技術を統合する試みも進んでいます。例えば、車載カメラでAIを活用して物体認識性能を向上させることで、安全運転支援システム(ADAS)の精度を高めることが可能です。この取り組みは、設計段階からソフトウェアとハードウェアの両方を最適化するアプローチが求められます。
- 筐体設計の軽量化と耐久性向上 カメラの持ち運びや車載利用を想定して、軽量化と耐久性向上の改善が求められます。具体的には、筐体材料に高強度プラスチックやマグネシウム合金を採用し、衝撃や振動に強い設計を実現します。この改善は、設計プロセスでCAE(コンピュータ支援工学)を活用することで精度を向上させます。
- 組み立て工程の効率化 製造ラインでの改善も重要です。たとえば、レンズユニットとセンサーユニットの位置合わせを高精度で行うために、自動化装置を導入する事例があります。この技術により、微小なずれを防ぎ、製品の品質を安定させることが可能になります。
カメラ設計におけるデータの活用
継続的改善を進める上で、データの活用が鍵となります。製造プロセスや市場からのフィードバックを分析することで、設計改善の方向性を特定します。
- フィードバック収集:顧客やユーザーからのレビューを定量化し、改良すべきポイントを特定します。
- 品質データの分析:例えば、出荷前テストで検出された不良データを分析し、不良率が高い箇所を重点的に改善します。
- 市場動向の監視:競合製品の性能や機能を調査し、それを上回る新しい機能を設計に組み込む努力を行います。
カメラ設計における継続的改善のメリット
- 競争力の強化:高品質で革新的なカメラ製品を提供することで市場シェアを拡大できます。
- コスト削減:製造工程の改善により不良率を低減し、コストを削減できます。
- 顧客満足度の向上:顧客のニーズに応える製品設計が可能になり、リピート購入やブランド忠誠度を高められます。
注意点と課題
カメラ設計の改善には高度な技術と専門知識が求められるため、リソースとコストの投入が必要です。また、新しい技術を導入する際には、従業員へのトレーニングや時間の確保が不可欠です。
カメラ設計での継続的改善は、競争の激しい市場での成功に不可欠です。技術革新と品質向上を両立させることで、顧客の期待を超える製品を提供できるでしょう。
リスクベース思考の導入
リスクベース思考は、組織が不確実性を予測し、潜在的な問題を事前に回避するための重要な考え方です。
これにより、製品の品質と信頼性を安定的に確保し、顧客満足度の向上や競争力の強化を図ることができます。特にカメラ設計においては、技術的なリスクや市場ニーズの変化に対応するための計画が欠かせません。
具体例:カメラ設計におけるリスクベース思考の活用
- センサーの供給リスク カメラ設計では、高性能なイメージセンサーの安定供給が製品品質を左右します。リスクベース思考を活用することで、センサー供給が途絶えるリスクを事前に評価し、複数の信頼性の高いサプライヤーを確保する方針を策定できます。例えば、供給元の生産状況や経済的安定性をモニタリングすることで、リスクの早期発見が可能です。
- 製品の過熱リスク カメラの小型化に伴い、プロセッサやセンサーが発熱しやすくなる問題が挙げられます。このリスクを軽減するため、設計段階で熱管理システム(例:ヒートシンクや熱伝導素材)の適切な配置を検討し、試作品での温度シミュレーションを実施します。これにより、製品の故障率を低減できます。
- 撮影環境のリスク カメラが使用される環境に応じたリスク評価も重要です。例えば、防水性や耐衝撃性が求められる環境では、設計段階で防水シールや強化ガラスの導入を検討する必要があります。市場のニーズを予測し、リスクを最小限に抑えることで、競争優位性を確保できます。
- ソフトウェアのセキュリティリスク カメラのネットワーク接続機能が普及する中で、サイバー攻撃のリスクも増加しています。このリスクを軽減するため、ファームウェアに最新の暗号化技術を組み込み、不正アクセスの可能性を最小化する設計を行います。また、ソフトウェアアップデートを定期的に提供する仕組みを構築することで、リスクに迅速に対応できます。
- サプライチェーンのリスク 部品供給の遅延や品質不良が製品の納期に影響を与えるリスクがあります。これを回避するため、主要な部品に対して定期的な品質監査を実施し、緊急時のバックアッププランを策定します。さらに、供給契約にリスク分担条項を盛り込むことで、リスクの軽減が可能です。
リスク特定と評価の方法
- FMEA(故障モード影響分析)の活用 カメラ設計において、FMEAを用いてリスクの発生確率や影響度を分析します。例えば、オートフォーカス機能における故障リスクを特定し、部品の選定や組み立て工程での改良に役立てます。
- データ収集と分析 過去の製品データや市場フィードバックを基に、リスク要因を定量的に評価します。たとえば、以前に発生した不具合を参考に、設計の改良点を明確化します。
カメラ設計におけるリスクベース思考のメリット
- 品質の安定性向上:事前にリスクを特定し対応することで、不具合の発生を防ぎます。
- 市場ニーズへの迅速な対応:環境や技術の変化に応じた製品開発が可能です。
- コスト削減:リスクを早期に発見し、トラブル解消に伴うコストを最小限に抑えられます。
課題と注意点
リスクベース思考を効果的に導入するには、時間とコストが必要です。また、全従業員にリスク管理の重要性を理解させる教育が不可欠です。特に、カメラ設計においては技術的な専門知識を持つ人材の確保も重要です。
カメラ設計におけるリスクベース思考は、製品の信頼性を高めるだけでなく、顧客からの信頼獲得や市場での競争優位性を確保するための強力なツールです。設計段階からリスクを適切に管理することで、長期的な成功につなげることが可能です。
リーダーシップの役割と責任
リーダーシップは、IATF 16949の効果的な導入と運用において不可欠な要素です。特にカメラ設計においては、トップマネジメントが全体の方向性を示し、プロジェクトを成功に導く役割を果たします。品質管理システムの維持と改善を主導するリーダーシップは、組織の統一性を確保し、目標達成を可能にします。
カメラ設計におけるリーダーシップの具体例
- 製品ビジョンの共有
トップマネジメントが「高品質なイメージセンサーを搭載し、競争力のある価格帯で市場に提供する」という明確なビジョンを策定し、それをチーム全体に共有します。このビジョンが組織全体で共有されることで、設計から製造、品質管理まで一貫した方針で取り組むことが可能となります。 - リソースの適切な割り当て
経営層が設計プロジェクトに必要なリソース(例えば、高性能な設計ソフトウェアや試作機材、専門技術を持つ人材)を提供することで、開発チームは効率的かつ高品質な製品を設計できます。例えば、熱管理設計用の最新シミュレーションソフトウェアを導入し、設計ミスを減らす支援を行います。 - 現場の声を反映する体制
カメラ設計の現場では、エンジニアやデザイナーが日々の業務で直面する課題を把握することが重要です。リーダーシップが現場の声を積極的に吸い上げ、例えば「新しい撮影モードを搭載するために必要な技術的課題」を議題に挙げ、早期解決を図ることで、設計チームの士気を高めることができます。 - 品質目標の設定と推進
トップマネジメントが「不良率を1%以下に抑える」といった具体的な品質目標を設定し、その達成に向けた戦略を立案します。この戦略には、製造工程での厳格な品質検査や設計段階でのリスク評価が含まれます。例えば、プロトタイプの段階で製品テストを強化し、潜在的な問題を早期に発見する体制を整えます。 - 部門間の連携強化
設計部門、製造部門、品質管理部門間の連携を強化するために、定期的な会議を設け、全員が最新のプロジェクト進捗と課題を共有できる仕組みを導入します。たとえば、新しいカメラモデルのレンズ構造に関する課題を共有し、製造現場での改善案を早急に反映させる体制を築きます。
リーダーシップが不足した場合の影響
- 方向性の欠如
トップマネジメントが具体的なビジョンや目標を示さない場合、設計プロジェクトが迷走し、結果として製品の品質低下や納期遅延に繋がるリスクがあります。 - モチベーションの低下
従業員が自分たちの努力が認められていないと感じると、改善提案や効率的な取り組みが減少する恐れがあります。 - 品質目標の未達成
リーダーシップが弱いと、品質管理体制が形骸化し、不良品の増加や顧客クレームの発生に繋がります。
リーダーシップ強化の方法
- 教育とトレーニングの提供
経営層自身がリーダーシップスキルや品質管理の知識を学び、実践することで、組織全体への良い影響を与えることができます。 - オープンなコミュニケーション
定期的な対話の場を設け、全員が組織目標に向かって協力できる環境を整えます。
カメラ設計の成功には、トップマネジメントの強いリーダーシップが欠かせません。設計の方向性を明確にし、必要なリソースを提供し、全員の声を反映させることで、組織全体の力を結集して高品質な製品を市場に届けることが可能です。
エビデンスに基づく意思決定の促進
データやエビデンスに基づく意思決定は、IATF 16949で求められる品質管理の中核をなす要素です。これにより、直感的な判断ではなく、客観的な情報に基づく合理的な意思決定が可能となり、リスク軽減や品質向上が実現します。
カメラ設計における具体例
- 顧客フィードバックの分析
市場に投入したカメラについて、顧客からのクレームや評価をデータベース化します。例えば、「低照度環境での画質が不十分」というクレームが頻出した場合、その情報をもとにセンサー設計の見直しを行い、新しいアルゴリズムを導入して画質を改善する計画を立てます。 - 製品テストデータの活用
カメラのシャッタースピードやフォーカス速度に関する試験データを収集し、分析します。このデータを用いて、特定の条件下で性能が低下する原因を特定し、ファームウェアの最適化や部品設計の変更を検討します。 - 製造工程のパフォーマンスモニタリング
カメラの組み立てプロセスにおけるエラー発生率や生産時間を継続的にモニタリングします。例えば、特定のラインで組み立てに時間がかかることが判明した場合、その工程を分解してボトルネックを特定し、改善することで生産効率を向上させます。 - 市場データの予測分析
カメラ市場のトレンドデータを分析し、将来の需要を予測します。例えば、「スマートフォン用高解像度レンズ」の需要が増加していることがわかれば、それに応じた設計や製造計画を早期に立てることで市場競争力を高めることが可能です。 - 環境試験データの活用
カメラを厳しい環境条件(高温多湿、低温、振動など)でテストし、そのデータを設計に反映します。例えば、レンズの曇りを防ぐためのコーティング材料の変更や、筐体のシール性を向上させる設計変更を実施することで、耐久性を向上させます。
エビデンス活用の利点
- 迅速な問題解決
客観的なデータを基に原因を特定できるため、問題解決がスピーディーに行えます。例えば、不具合が発生した場合、データに基づき迅速に設計変更が可能です。 - リスク軽減
市場投入前に十分なデータ分析を行うことで、品質トラブルを未然に防ぐことができます。これにより、リコールや顧客満足度の低下を回避できます。 - 資源の最適化
データを活用して必要な変更を最小限に抑えることで、リソースの効率的な利用が可能です。
エビデンス活用の課題と対策
- データ収集と分析の負担
適切なシステムがなければデータ収集に時間がかかります。これを解決するため、クラウドベースのデータ管理システムやAI分析ツールを導入します。 - スキル不足
分析スキルを持つ人材が不足している場合、従業員向けのデータ分析トレーニングプログラムを実施します。 - データの信頼性
不正確なデータが意思決定に影響を与える可能性があります。そのため、データ入力の精度を向上させるチェックプロセスを導入します。
カメラ設計におけるエビデンスに基づく意思決定は、製品の品質と競争力を高めるうえで非常に重要です。設計、製造、そして市場投入後まで一貫してデータを活用することで、顧客満足度の向上と効率的な運営が実現します。
サプライチェーンの有効な管理
IATF 16949では、サプライチェーンの管理が品質維持と製品の競争力向上の要として強調されています。信頼性の高いサプライヤーとの連携を強化し、製品品質を安定させることが重要です。
カメラ設計における具体例
- 光学部品の品質評価
カメラ設計では、レンズやセンサーなどの光学部品が製品の性能に直結します。サプライヤーから納入される部品については、定期的な品質評価を実施します。例えば、レンズの透過率や歪みの有無、センサーの感度やノイズレベルを評価し、基準を満たさない場合は改善指導を行います。 - サプライヤーの技術力向上支援
特殊な光学素材や微細加工技術を必要とする場合、サプライヤーがそれらに対応できる技術を持たない可能性があります。その際、技術トレーニングやプロセスの改善提案を行い、サプライヤーの技術力向上を支援します。これにより、双方が持続的な成長を実現できます。 - 緊急時の代替サプライヤー確保
主要なサプライヤーからの供給が途絶した場合、プロジェクト全体が遅延するリスクがあります。例えば、センサー供給が止まった場合に備え、性能や仕様が同等の部品を提供できるサプライヤーを事前にリストアップし、調達プロセスを準備しておきます。 - 供給リードタイムの最適化
サプライチェーン管理においては、部品の供給リードタイムを短縮することが求められます。カメラ設計では、新製品開発が進む中でのリードタイム短縮が市場投入時期に大きな影響を与えます。例えば、サプライヤーと共同で在庫のリアルタイム管理を行い、必要部品を迅速に調達可能な体制を構築します。 - 輸送中の品質維持
高精度なレンズやセンサーは輸送時に損傷しやすいため、梱包や輸送条件の管理が重要です。特に、湿度や衝撃が製品に影響を与える可能性がある場合、適切な緩衝材を使用し、温湿度センサー付きの輸送パッケージを採用することで、品質を確保します。
サプライチェーン管理の利点
- 製品品質の安定
厳格なサプライヤー評価と管理により、品質基準を満たす部品を一貫して供給できます。 - コスト削減
サプライチェーン全体を最適化することで、余剰在庫や輸送コストを削減できます。 - リスクの軽減
緊急時に備えた代替サプライヤーの確保により、供給途絶のリスクを低減します。
課題と対策
- 監査コストの増加
サプライヤー監査にはリソースが必要です。対策として、リスクが高いサプライヤーに監査を集中させ、効率を高めます。 - コミュニケーション不足
設計要件や品質基準が正確に伝わらない場合、トラブルが発生します。定期的な技術レビューや仕様確認ミーティングを通じて、この課題に対応します。
サプライチェーン管理は、カメラ設計において高品質な製品を市場に提供するための基盤となります。信頼性と効率性を追求しながら、継続的に改善を行うことが求められます。
IATF16949を実現するための基本要素
品質管理は、顧客満足と競争力向上の基盤であり、IATF 16949規格の実践はその最善策の一つです。
本記事では、品質方針の策定から、具体的な目標設定、リソースの整備、プロセス運用、データ活用、従業員教育、そして品質管理ツールの適用まで、組織が高品質な製品を提供するための体系的なアプローチを詳しく解説します。
特に、カメラ設計に焦点を当て、PPAPやFMEA、SPCなどのコアツールをどのように適用し、顧客要求を満たす製品を生み出すかを具体例を交えて紹介します。
この記事を通じて、品質管理の重要性と実践的な方法を理解し、持続的な成長を目指すヒントを提供します。
品質方針と目標の設定
品質方針と目標の設定は、組織全体で統一した品質管理の基盤を形成し、持続可能な成長を支えるための重要な活動です。品質方針は組織の使命や価値観を明確に反映し、全従業員に共有されるべきです。一方で、品質目標は具体的かつ測定可能である必要があります。
品質方針の具体例
例えば、製造業では以下のような品質方針を設定できます:
- 「高品質な製品を安定して提供し、顧客の期待を超える満足を追求する」
- 「環境に配慮した持続可能な生産を通じて、社会的責任を果たす」
これらの方針は、組織のビジョンや戦略に基づいて策定され、従業員全員が理解し行動に移せる内容でなければなりません。具体的には、日常業務の中で品質方針がどのように反映されているかを、従業員が実感できる形に落とし込むことが求められます。
品質目標の具体例
品質目標は、具体的で測定可能な形式で設定されるべきです。以下に具体例を挙げます:
- 顧客満足度向上
「顧客満足度を90%以上に維持する」
この目標を達成するためには、定期的な顧客アンケートの実施や、フィードバックを分析する仕組みを整える必要があります。例えば、不良品に対する迅速な対応や、顧客が製品に抱える不満点を解消するための改善活動が効果的です。 - 不良品率の削減
「不良品率を1%未満に抑える」
この目標では、生産ラインの定期的なメンテナンスや、製造工程でのリアルタイムモニタリングを導入することで、問題発生を未然に防ぐことができます。例えば、機械のセンサーを活用して製品の精度を常にチェックする仕組みが挙げられます。 - 納期遵守率の向上
「納期遵守率を98%以上に維持する」
具体的には、製造スケジュールの見直しや、サプライチェーンの効率化を通じて、納期の遅延を最小限に抑えることが目標達成につながります。例えば、部品供給の遅延リスクを予測し、緊急時の対応策を事前に計画しておくことが効果的です。 - 環境目標
「製造工程でのCO2排出量を5%削減する」
これには、エネルギー効率の高い設備の導入や、リサイクル可能な材料の活用が含まれます。例えば、生産工程での廃棄物を減らすために、余剰材料を再利用する仕組みを整備します。
注意点と改善のポイント
- 現実的な目標設定
現実離れした目標は従業員のモチベーションを低下させる可能性があります。例えば、「1カ月で不良品をゼロにする」ような過剰な目標は、現場に過度な負担を与えるだけでなく、達成が難しい場合があります。 - 定期的なレビュー
設定した目標が適切であるかどうかを定期的に見直すことが重要です。市場の変化や顧客の要求が変化した場合、目標を柔軟に調整する必要があります。 - 従業員の関与
品質目標の達成には従業員の協力が不可欠です。そのため、現場の意見を取り入れ、目標が現実的で達成可能なものであるようにすることが求められます。
品質方針と目標の設定は、組織の方向性を明確に示し、全従業員を同じ目標に向けて動かすための強力なツールです。適切な設定と実行により、顧客満足度の向上や業績改善が期待できます。
必要なリソースとインフラの整備
品質管理を成功させるためには、必要なリソースとインフラを適切に整備することが不可欠です。これには、人材、設備、技術、情報システムなど、製品やサービスの品質向上に直結する要素が含まれます。リソースが十分に確保されていると、プロセスの効率化や製品品質の向上が実現しやすくなります。
設備投資の具体例
例えば、自動車部品の製造工場では、新しいCNC(コンピュータ数値制御)機械を導入することによって、加工精度が向上し、不良品率を大幅に削減できます。また、スマートセンサーを使用した設備では、稼働状況をリアルタイムでモニタリングできるため、故障の予兆を検知して事前に対処することが可能です。これにより、生産ラインの停止を最小限に抑え、納期遅延のリスクを軽減します。
人材リソースの整備
人材も重要なリソースの一部です。例えば、新しい設備を導入した際に、操作方法を熟知したオペレーターが不足していると、その効果を十分に発揮できません。そのため、専門的なスキルを持つ人材を採用するだけでなく、既存従業員へのトレーニングも欠かせません。具体的には、設備メーカーから提供される研修プログラムを活用したり、eラーニングで効率的に知識を習得する方法があります。
作業環境の整備
作業環境の整備もまた重要です。例えば、製造現場での騒音や温度管理が不十分だと、従業員の集中力が低下し、不良品の増加や安全事故の発生につながる可能性があります。このような課題を解決するために、防音設備を設置したり、適切な空調システムを導入することで、安全で快適な環境を提供することが求められます。
情報システムの活用
近年では、情報システムの整備が品質管理の鍵を握るケースが増えています。例えば、ERP(企業資源計画)システムを導入することで、在庫管理や製造工程の進捗を一元的に把握でき、リソースの無駄を減らすことができます。また、品質管理専用のソフトウェアを使用することで、不良品の発生原因を迅速に特定し、データに基づいた改善策を実施することが可能です。
コストと投資対効果のバランス
一方で、リソースやインフラの整備には多額のコストがかかる場合があります。そのため、投資対効果(ROI)を十分に検討することが必要です。例えば、高額な設備を購入する前に、リースや中古設備の活用を検討することも一つの選択肢です。また、インフラの整備状況を定期的に点検し、過剰なリソースを見直すことでコストを削減できます。
必要なリソースとインフラの整備は、品質管理の基盤を強化するための重要なステップです。ただし、コスト管理を怠ると負担が増加する可能性があるため、計画的かつ効率的な整備を進めることが求められます。
プロセスの計画と運用
プロセスの計画と運用は、カメラ設計や製造プロセスの品質を支える重要な基盤です。特に、カメラの製造では高精度な工程管理が求められるため、プロセスを効果的に計画し、運用することが成功の鍵となります。
カメラプロセス計画の具体例
- レンズ製造工程の計画
高解像度カメラのレンズは、わずかな形状誤差が性能に大きく影響します。そのため、以下のような計画を行います:- 素材選定:光学ガラスの種類を事前に評価し、適切な素材を確保します。
- 精密加工:レンズの曲率や厚みをミクロン単位で設定し、製造設備に反映させます。
- 検査工程の設置:加工後のレンズを全数検査し、歪みや欠陥をチェックします。
- センサー実装工程の計画
CMOSセンサーをカメラ本体に組み込む際には、清浄な環境と精密な位置合わせが不可欠です:- クリーンルームの設置:塵や微粒子が製品に影響しないよう、特別な環境を整えます。
- ロボットによる位置決め:センサーとレンズの光軸が正確に一致するよう、自動化技術を活用します。
プロセス運用の具体例
- リアルタイム監視と調整
製造中の工程をモニタリングし、異常が発生した場合にすぐに対応します:- 温度管理:レンズやセンサーの接着工程では温度が製品に影響するため、センサーでモニタリング。
- トレーサビリティの確保:各製品に固有のIDを付与し、製造履歴を追跡可能にします。
- 製品テストの徹底
組み立て後のカメラモジュールが基準を満たしているか確認します:- 光学テスト:画像の歪みやピント精度をチェックする専用装置を使用。
- 耐久テスト:極端な温度や湿度条件での動作確認を行い、製品信頼性を検証。
柔軟な対応とリスク管理
- 代替サプライヤーの確保
特定のレンズ素材が供給不足になった場合、代替素材を使用する計画を立てておくことで製造の中断を防ぎます。- 例:特定ガラス素材の不足時に、性能が近い別素材を事前に検証し、リスト化。
- プロセス改善の継続
製造中のデータを分析し、効率性や品質を向上させる取り組みを進めます:- 不良品率の削減:製品検査で検出された不良の原因を特定し、設備設定を最適化。
- 新技術の導入:AIを活用して画像検査を自動化し、人的ミスを削減。
カメラのプロセス計画と運用は、高品質な製品を安定して提供するための土台です。工程を事前に計画し、柔軟な運用体制を整えることで、競争力のあるカメラを市場に送り出すことが可能になります。
データに基づく意思決定
データに基づく意思決定は、品質管理やプロセス改善において欠かせない要素です。カメラ製造業界では、データを活用することで、精密かつ効率的な製品設計や製造プロセスの改善が可能となります。
カメラ製造におけるデータ活用の具体例
- レンズ製造工程での不良率データの活用
例として、レンズの研磨工程で不良率が5%に達している場合、このデータを分析することで、問題の原因を特定できます。例えば、研磨装置の動作パラメータが不安定であれば、機械のキャリブレーションを見直すことで、不良率を2%以下に抑えることが可能です。 - 画像センサーの性能評価データ
CMOSセンサーのテストデータを基に、画質やノイズレベルを分析することで、特定のセンサーが規定を満たしていない場合に、設計変更や製造条件の調整を行います。これにより、高解像度画像を安定的に提供できる製品開発が可能です。 - 組み立て工程の歩留まりデータの追跡
組み立て工程でのデータを収集し、製品の完成率(歩留まり)が80%以下の場合、どのステージで問題が発生しているかを特定します。例えば、ネジの締め付けトルクがばらついている場合には、自動化されたトルク管理システムを導入し、歩留まりを95%以上に向上させることができます。
データを活用した顧客フィードバック分析
- 顧客満足度調査の活用
カメラの購入後に顧客が記入するアンケートを分析することで、特定のモデルのズーム機能に不満が集中している場合、ズーム操作に関する設計改善が可能です。これにより、新モデルでの顧客満足度を15%向上させる結果が得られた事例もあります。 - クレームデータのパターン分析
製品保証期間内のクレームデータを分析し、特定のロットにおいてシャッターボタンの故障が多発している場合、製造工程での検査を強化することで、再発を防ぐことができます。
効果的なデータ管理と意思決定のための取り組み
- リアルタイムデータ収集の導入
製造ラインにIoTセンサーを設置し、温度や湿度、振動などのデータをリアルタイムで収集します。これにより、環境条件が製品品質に与える影響を即座に判断し、条件を最適化できます。 - AIによるデータ分析
AIツールを活用して、大量の画像検査データを短時間で分析し、不良品を迅速に特定します。これにより、人間の検査よりも効率的かつ精度の高い品質管理が実現します。
課題と注意点
データ活用には適切な収集方法と分析スキルが必要です。
信頼性の低いデータに基づく判断は誤解を生む可能性があるため、ツールやシステムの選定が重要です。これにより、カメラ製造における品質と効率をさらに向上させることができます。
従業員教育と能力開発
従業員教育と能力開発は、組織の競争力を維持し、品質目標を達成するための重要な基盤です。適切な教育を通じて、従業員が求められる知識やスキルを身につけることで、プロセスの効率化や製品の品質向上が期待できます。
カメラ製造における教育と能力開発の具体例
- 新しい検査システムのトレーニング
例えば、カメラの画像センサーを検査するためのAI搭載の新しい検査システムを導入した場合、現場作業員向けに操作方法とデータの解釈方法を学ぶトレーニングを実施します。このトレーニングにより、不良品の検出精度が向上し、結果的に顧客満足度の向上に寄与します。 - レンズ研磨技術の向上研修
レンズ製造の精度を向上させるために、熟練技術者を講師として研磨技術に関する実地研修を実施します。これにより、従業員のスキルが向上し、製品の光学性能が安定します。 - 品質管理に関する資格取得の支援
品質管理担当者が「品質管理検定(QC検定)」や「ISO 9001内部監査員」の資格を取得するための講座を提供し、受験費用を負担します。資格取得により、品質管理体制が強化され、認証維持にも貢献します。
継続的なスキルアップの取り組み
- オンライン学習プラットフォームの活用
最新技術や業界のトレンドに対応するために、従業員がいつでも学べるオンライン学習システムを導入します。例えば、カメラのAI画像処理技術に関するコースを用意し、エンジニアが自主的に学べる環境を整えます。 - 問題解決能力を鍛えるワークショップ
製造現場で頻発する問題をテーマにしたグループディスカッションやケーススタディを通じて、従業員が自ら解決策を考える能力を育成します。この活動により、現場での柔軟な対応力が高まります。
教育と業務のバランスを取る方法
- スケジュール管理の工夫
トレーニングを業務時間外ではなく、業務時間内に計画的に組み込むことで、従業員の負担を軽減します。例えば、生産スケジュールの低い時期に集中して研修を実施する方法が効果的です。 - 実務と連動した教育
現場での作業を通じて学ぶ「OJT(オン・ザ・ジョブ・トレーニング)」を積極的に採用します。例えば、カメラの組み立て工程で新しいスキルを習得しながら、即戦力として活躍できる仕組みを構築します。
注意点と課題
教育にリソースを集中しすぎると、短期的には通常業務に支障をきたす可能性があります。これを防ぐために、教育計画を事前に調整し、業務への影響を最小限に抑える工夫が必要です。また、教育成果を定量的に評価し、その効果を定期的にレビューすることも重要です。
従業員教育と能力開発は、短期的な成果だけでなく、長期的な組織の成長に直結する取り組みです。適切な計画と実行によって、より強固な品質体制と競争力を実現できます。
IATF 16949の初心者向け5コアツールの解説
IATF 16949は、製造業における品質管理と効率向上を目指す国際規格であり、その導入には5つのコアツールの理解が欠かせません。
この記事では、PPAP(生産部品承認プロセス)、FMEA(故障モード影響分析)、SPC(統計的プロセス管理)、APQP(先行製品品質計画)、MSA(測定システム分析)について、初心者にもわかりやすく解説します。
各ツールがどのように相互に関連し、実際の現場でどのように活用されるか、具体的な事例を交えながら解説することで、カメラ設計をはじめとする実務への適用方法を学べます。
品質基準を確立し、プロセスの効率化を図りたい方に役立つ内容です。
PPAP(生産部品承認プロセス)とは?
PPAP(生産部品承認プロセス)は、自動車業界だけでなく、カメラ設計や製造の分野でも品質と信頼性を確保するために重要なプロセスです。以下は、カメラ設計におけるPPAPの具体的な流れと各ステップの内容です。
1. 要件の確認
カメラ設計におけるPPAPプロセスは、顧客の要求事項を詳細に確認することから始まります。
- 例: 顧客が望むカメラの解像度、フレームレート、レンズ焦点距離、使用環境条件(高温多湿や低温環境での使用など)を把握。
- 必要に応じて、仕様書を顧客と共有し、相互に合意する。
2. 設計文書の準備
設計仕様が固まったら、設計文書を作成します。これには、設計図面やCADデータ、部品表(BOM)が含まれます。
- 具体例:
- レンズの光学特性を示す設計図
- センサーのピクセル数や感度範囲の仕様書
- シャッターメカニズムの動作原理図
3. 試作品の製造と評価
試作品を製造し、顧客の要件を満たしているかどうかをテストします。この段階では、設計段階の問題を特定し、必要に応じて修正を行います。
- 例:
- 試作したカメラを低照度条件でテストし、画像ノイズを確認する。
- 動作温度範囲内でのセンサーの応答性を評価。
4. プロセス設計と文書化
量産を想定したプロセスフロー図や、工程ごとのリスクを分析したFMEAを作成します。
- 具体例:
- レンズ組立ラインのプロセスフロー図を作成し、リスクとして「異物混入」や「接着不良」を特定。
- PCB(プリント基板)のはんだ付け工程での品質リスクをFMEAで評価。
5. 試験データの提出
製品が設計仕様を満たしていることを示すための試験データを提出します。これには、物理的特性試験、性能試験、環境試験の結果が含まれます。
- 例:
- レンズの耐衝撃試験データ(落下テスト後の光学性能評価)。
- センサーの高温・低温サイクル試験データ。
6. サンプル部品の提出
試作品や初期生産ロットのサンプルを顧客に提出します。これにより、顧客が設計や製造の一貫性を確認します。
- 例: 顧客が要求する10台分のカメラサンプルを製造し、各サンプルについてテスト結果を添付して提出。
7. 顧客承認
顧客が提出された文書とサンプルを確認し、承認を行います。承認が得られた後、量産が正式に開始されます。
- 注意点:
- 顧客からの承認プロセスが遅延すると、量産開始が後ろ倒しになる可能性があるため、スケジュール管理が重要です。
カメラ設計におけるPPAPの重要性
PPAPプロセスは、カメラ設計において以下の効果を発揮します:
- 品質の一貫性: 顧客が期待する性能を維持したカメラを安定的に供給可能。
- トラブルの未然防止: 量産開始後の不良品リスクを最小化。
- 信頼性の向上: 顧客からの信頼を獲得し、長期的な取引関係を築く。
注意点
PPAPの各ステップは非常に詳細な準備が必要であり、時間とコストがかかる可能性があります。そのため、チーム全体で効率的に取り組む仕組みを整えることが成功の鍵となります。
FMEA(故障モード影響分析)の基本
FMEA(故障モード影響分析)は、製品やプロセスの潜在的な故障を事前に特定し、その影響と原因を分析する手法です。この分析により、問題が発生する前に対策を講じることが可能となります。
例えば、新製品を設計する際には、FMEAを活用して、製品が使用中にどのような故障が起こり得るかを洗い出し、そのリスクを評価します。そして、優先順位をつけてリスクを軽減するための具体的な措置を講じます。
FMEAの実施には時間とリソースが必要ですが、適切に運用すれば、顧客満足度の向上やリコールの防止につながります。
詳細は「FMEA やり方を徹底解説!初心者にもわかる具体例付き手法」の記事を参照してください。
SPC(統計的プロセス管理)の役割
SPC(統計的プロセス管理)は、製造工程の変動を監視・管理する統計的手法です。ここでは、Cpk(工程能力指数)の計算方法とQC7つ道具の具体的な数値例を挙げ、カメラ製造における適用例を詳しく説明します。
Cpk(工程能力指数)の計算方法
Cpkは、プロセスが顧客要求をどの程度満たしているかを評価する指標です。以下の式で計算されます: $$Cpk = \text{min} \left( \frac{\text{USL} – \mu}{3\sigma}, \frac{\mu – \text{LSL}}{3\sigma} \right)$$
- USL: 上限規格値(Upper Specification Limit)
- LSL: 下限規格値(Lower Specification Limit)
- μ: 平均値
- σ: 標準偏差
具体例:カメラレンズの直径測定
- 要求仕様: 直径10.00 ± 0.05 mm(USL = 10.05, LSL = 9.95)
- 測定結果:
- 平均値は以下であったとする $$(\mu): 10.01 mm$$
- 標準偏差は以下であったとする $$(\sigma): 0.015 mm$$
計算手順
- 上限側のCpk計算: $$\frac{\text{USL} – \mu}{3\sigma}= \frac{10.05 – 10.01}{3 \times 0.015} = \frac{0.04}{0.045} \approx 0.89$$
- 下限側のCpk計算: $$\frac{\mu – \text{LSL}}{3\sigma}= \frac{10.01 – 9.95}{3 \times 0.015} = \frac{0.06}{0.045} \approx 1.33$$
- Cpkの最小値を採用: $$Cpk=min(0.89,1.33)=0.89$$
結果の解釈:Cpk = 0.89:顧客要求を完全には満たしておらず、プロセスの改善が必要です。
QC7つ道具の具体例
1. チェックシート
- 内容: レンズ表面の傷に関する不良記録
- データ例:
- 1日目: 傷12件
- 2日目: 傷9件
- 3日目: 傷15件
- 改善目標: 1日あたりの傷を5件以下に削減。

2. 管理図
- 対象: レンズの厚み
- データ例:
- サンプルサイズ: 25個
- 平均値 $$(\bar{X}): 9.98 mm$$
- 管理限界:
- 上限 (UCL): 10.07 mm
- 下限 (LCL): 9.91 mm
- 結果: 全てのサンプルがUCL、LCL以内であり、余裕もあるため安定している
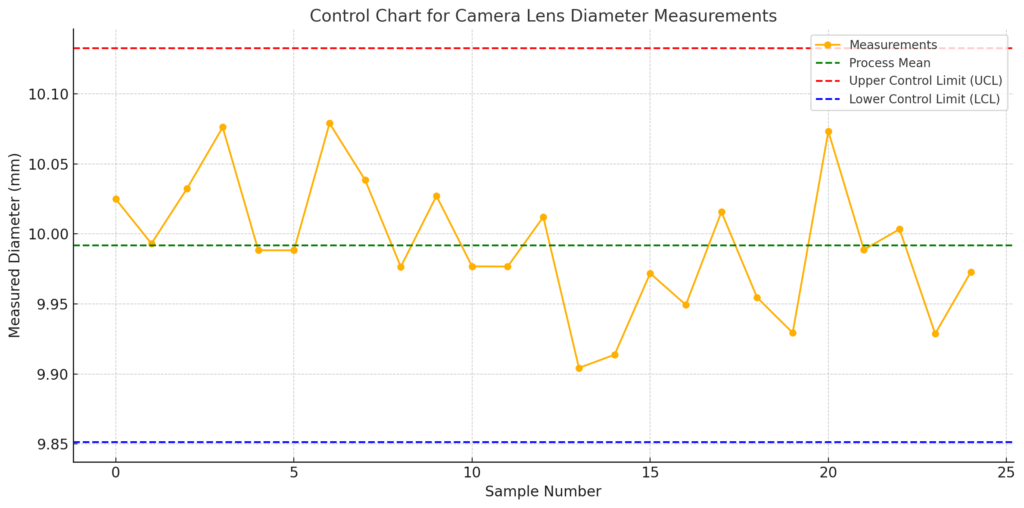
3. パレート図
- 内容: 不良原因の割合
- 表面傷: 45%
- 寸法不良: 30%
- コーティング欠陥: 25%
- 対策: 表面傷対策を優先。
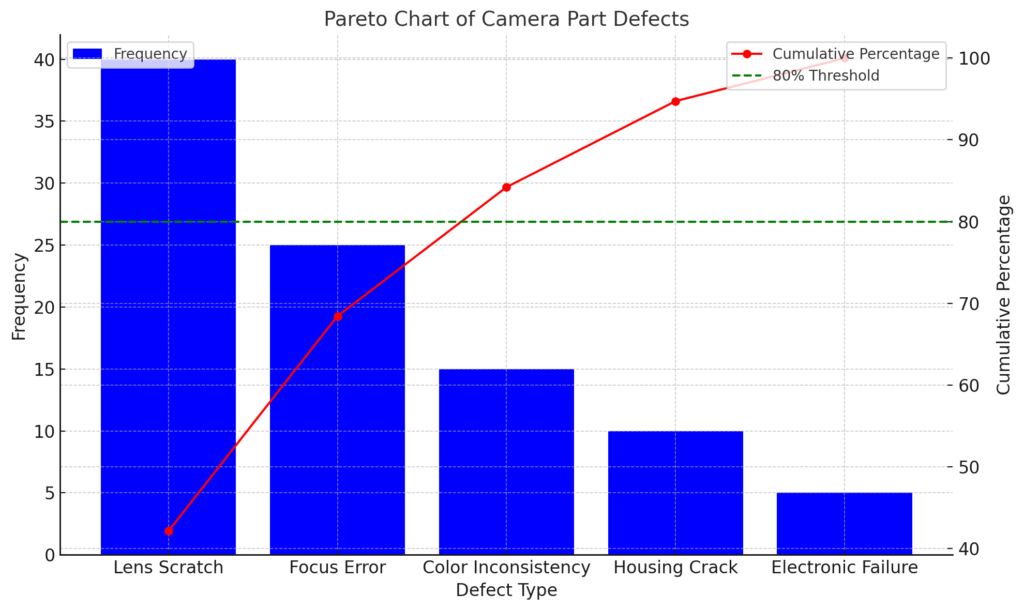
4. 特性要因図(魚骨図)
- 問題: レンズの表面傷
- 要因:
- 人: 作業者の技術不足
- 機械: 研磨装置の劣化
- 環境: クリーンルーム内の粉塵
- 対策: 作業者研修と装置の定期メンテナンスを実施。
5. ヒストグラム
- 対象: レンズの直径
- データ例:
- 平均値: 10.01 mm
- 範囲: 10:00 mm ~ 10.04 mm
- 分布: 正規分布を示すが、USLに近いデータが多いため調整が必要。
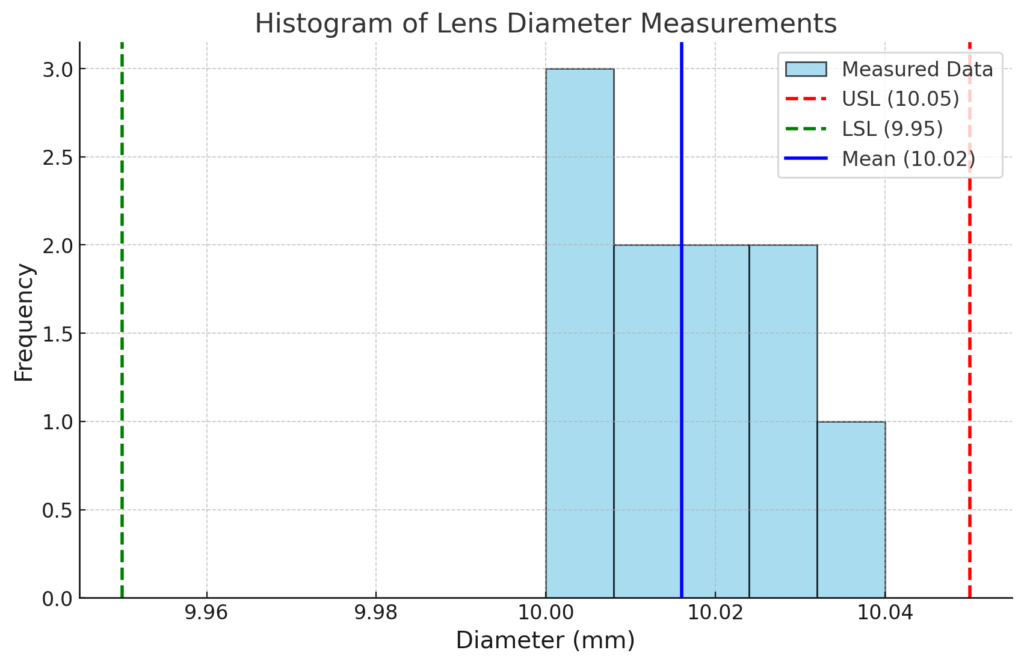
6. 散布図
- 分析内容: コーティング厚みと光透過率の関係
- 相関係数: 0.85(高い相関あり)
- 改善案: コーティング厚みを均一化することで光透過率を向上。
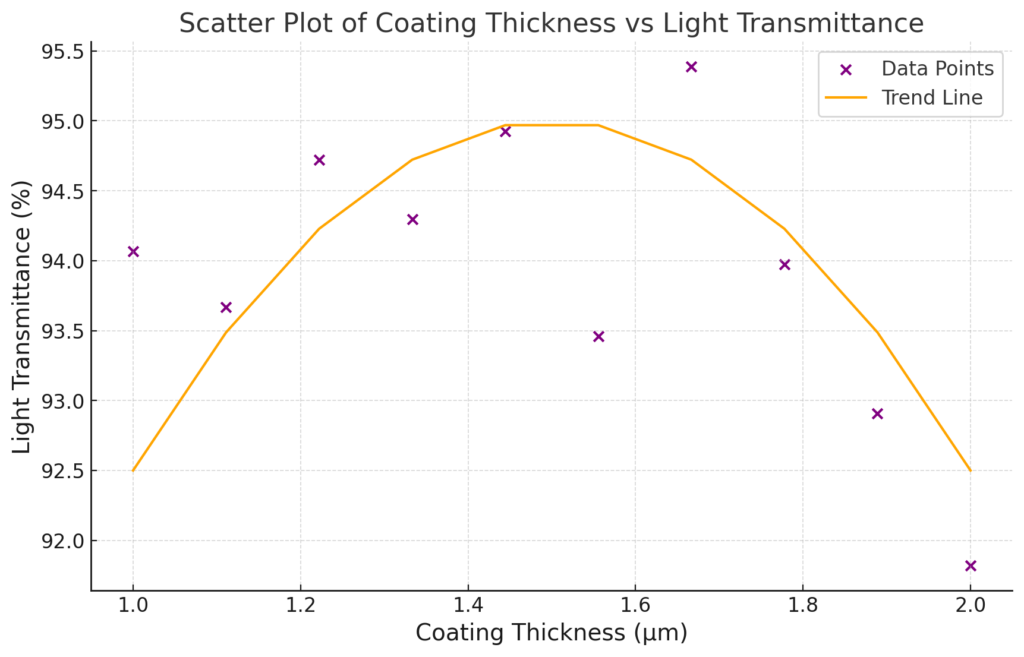
7. 層別
- 対象: 製造ライン別の不良率
- ラインA: 不良率1.5%
- ラインB: 不良率3.2%
- 対策: ラインBの作業手順と設備を再評価。
APQP(先行製品品質計画)の概要
以下は、カメラ設計におけるAPQP(先行製品品質計画)の具体的な手順を解説します。カメラの品質を確保しつつ、顧客要件を満たすためのプロセスを体系的に進める方法を示しています。
APQPの具体的な手順(カメラ設計の場合)
1. 計画と定義のフェーズ
このフェーズでは、顧客の要件や期待を明確化し、プロジェクトの基本方針を定めます。
- 顧客要件の確認
例:カメラの解像度、レンズの焦点距離、シャッター速度、耐久性といった仕様を詳細に確認。 - 設計目標の設定
顧客要件に基づき、「高解像度レンズの設計」「コンパクトで耐久性の高いボディ」など具体的な目標を設定。 - リソースの割り当て
設計者、試作品製作チーム、品質管理担当者などをプロジェクトチームに編成。
2. 製品設計と開発のフェーズ
設計プロセスを進め、製品の仕様を詳細化します。
- 設計レビュー
CADツールを用いてカメラ構造の初期設計を作成し、各部品の仕様と機能を確認。 - 試作品の製作
例:初期段階でレンズの曲率や材料の選択が適切かを確認するための試作品を製作。 - FMEA(故障モード影響分析)の実施
例:レンズの素材や製造工程に潜むリスクを特定し、不良率削減の対策を計画。
3. プロセス設計と開発のフェーズ
量産を想定した製造プロセスを設計します。
- プロセスフローの作成
レンズ研磨、組み立て、テスト工程を含むフロー図を作成し、各段階で必要なリソースを割り当て。 - SPC(統計的プロセス管理)の導入
レンズの厚みや研磨精度をモニタリングするための管理図を作成。 - 試作ラインの設置と検証
例:製造ラインをテストし、カメラボディとレンズの組み立て精度を確認。
4. 製品およびプロセスの検証フェーズ
設計とプロセスが顧客要件を満たしているか確認します。
- 量産試作品の評価
例:完成した試作品の性能テスト(解像度、耐久性、使用感)を行い、顧客要件を満たしているかを確認。 - Cpk(工程能力指数)の測定
例:レンズの寸法公差や組み立て精度が統計的に管理されているかを評価。 - 顧客承認の取得
顧客に試作品を提供し、承認を得るプロセス。
5. 量産準備とローンチ
量産に向けた準備を行い、市場への投入を開始します。
- 量産ラインの最適化
試作ラインで得られたデータを活用し、量産ラインを調整。 - 最終製品テスト
例:製造されたカメラの全数検査を行い、不良品が市場に流出しないよう管理。 - 量産開始
市場ニーズに応じた適切なタイミングで量産開始。
このように、APQPをカメラ設計プロセスに適用することで、顧客満足度の向上と開発効率の最適化が期待できます。
MSA(測定システム分析)の重要性
MSA(測定システム分析)は、製品の品質を正確に評価するためのデータの信頼性を確保する手法です。不適切な測定システムでは、得られるデータが誤った結果を導き、製造プロセスや製品品質の改善が困難になることがあります。そのため、測定システムの精度や信頼性を定期的に検証することが求められます。
以下では、MSAの5つの主要な検証ツールを具体例と数値を用いて説明します。
MSAの5つの検証ツールと具体例
1. 偏り(Bias)
測定システムの平均測定値と基準値(真値)との間の差を評価します。
例:
- カメラセンサーの解像度を評価する機器で、実際の解像度が 1200 dpi である場合、測定器が 1250 dpi を示したとします。
- 偏り = 測定値 (1250 dpi) – 真値 (1200 dpi) = +50 dpi
この結果から、測定システムが一貫して真値より 4.17% 高く表示する偏りがあると判断できます。
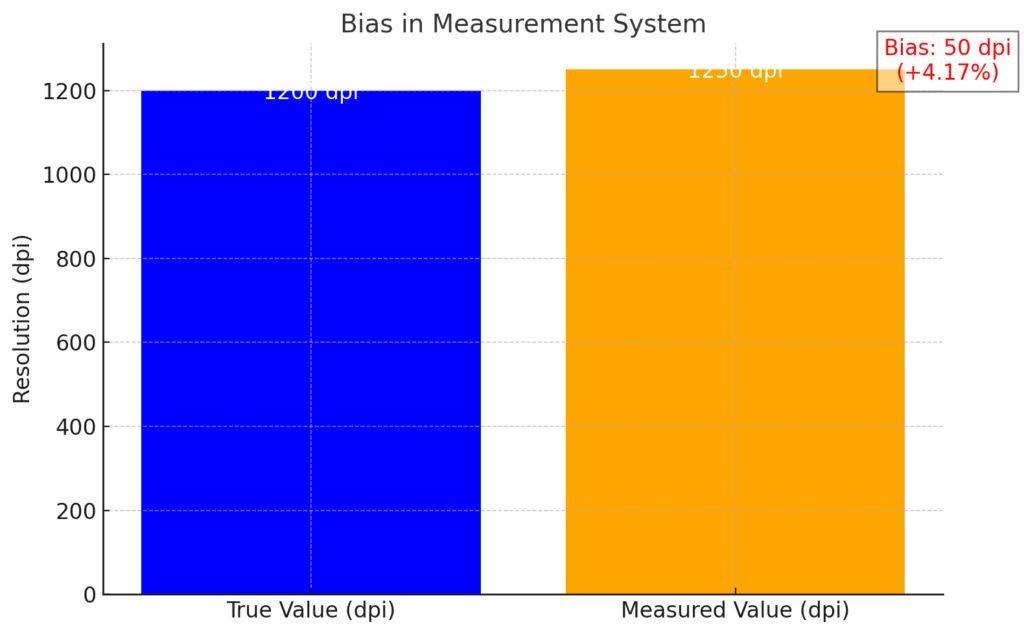
2. 安定性(Stability)
測定システムが時間の経過とともに一貫性を保てるかを評価します。
例:
- レンズ透過率を測定する装置で、1週間にわたり10回測定を行った場合、以下のような結果が得られたとします:
- 測定値: 91.2%、91.0%、91.3%、91.5%、91.2%、90.8%、91.4%、91.3%、91.1%、91.2%
- 標準偏差: 0.22%
この値が仕様範囲(±1%以内)に収まる場合、測定システムは「安定している」と言えます。
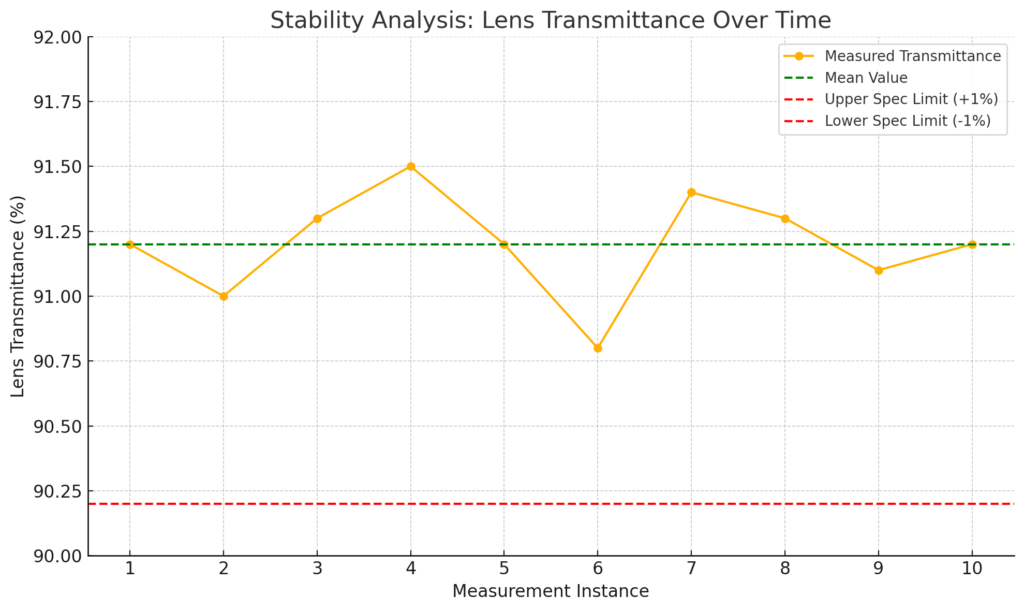
3. 直線性(Linearity)
測定範囲全体で測定の精度が一貫しているかを確認します。
例:
- シャッター速度を 0.1秒から1秒 の範囲で測定し、以下の結果を得た場合:
- 実際の速度: 0.1秒, 0.5秒, 1秒
- 測定値: 0.12秒, 0.48秒, 0.96秒
- 測定値の誤差はそれぞれ +0.02秒, -0.02秒, -0.04秒 であり、範囲内で一貫性が確認されます。
この場合、直線性が良好であると評価できます。
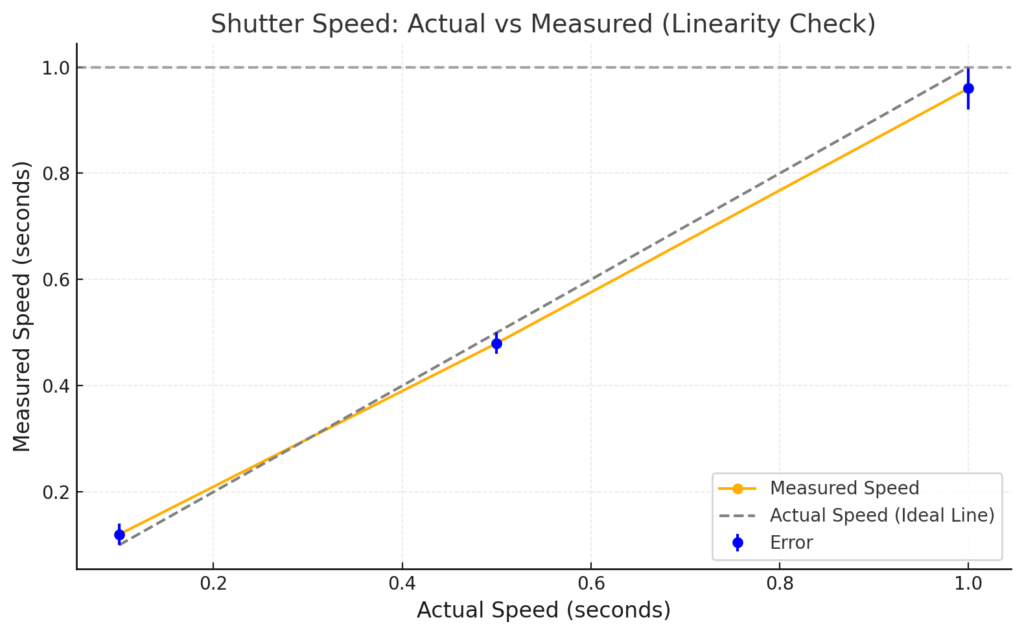
4. 繰り返し性(Repeatability)
同じ測定者が同じ条件で繰り返し測定した場合の測定値のばらつきを評価します。
例:
- 同一のカメラモジュールで焦点距離を 5回測定 した結果:
- 測定値: 35.1mm, 35.0mm, 35.2mm, 35.1mm, 35.0mm
- 標準偏差: 0.07mm
このばらつきが仕様の範囲内である場合、繰り返し性が確保されています。
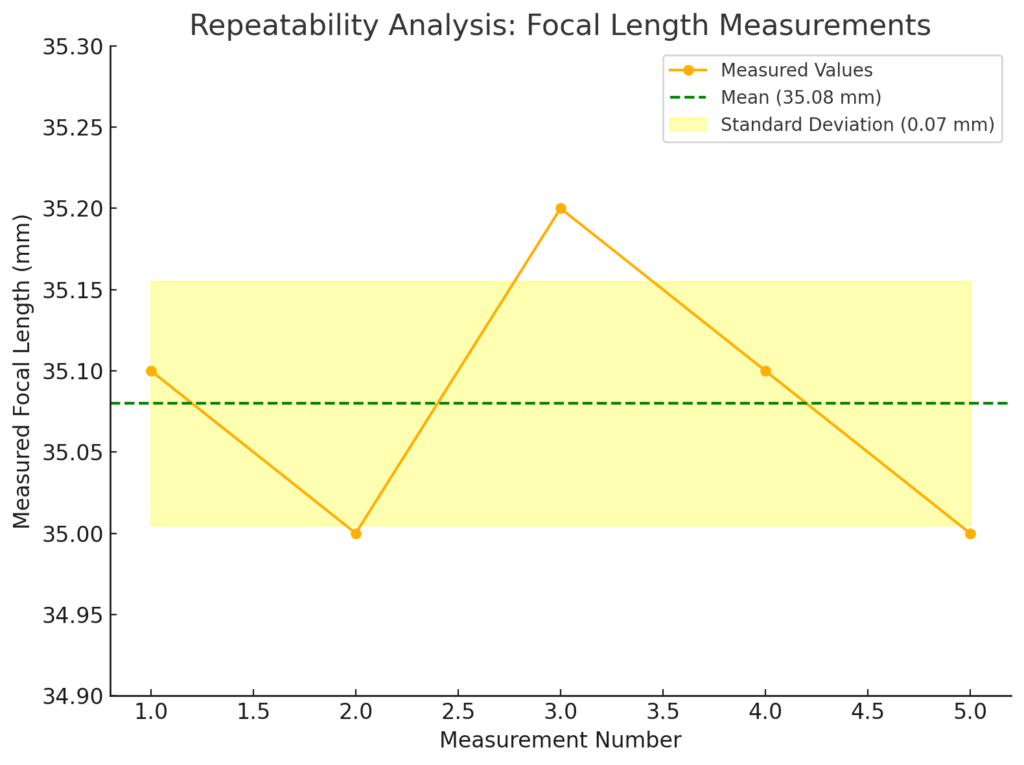
5. 再現性(Reproducibility)
異なる測定者が同じ条件で測定した場合の測定値のばらつきを評価します。
例:
- 3人の技術者がレンズの歪みを測定し、以下の結果を得たとします:
- 技術者A: 2.1%、2.2%、2.3%
- 技術者B: 2.0%、2.1%、2.2%
- 技術者C: 2.2%、2.3%、2.4%
- 全体の平均値: 2.2%
- 最大ばらつき(再現性の誤差): ±0.2%
この範囲が許容値内であれば、再現性があると判断されます。
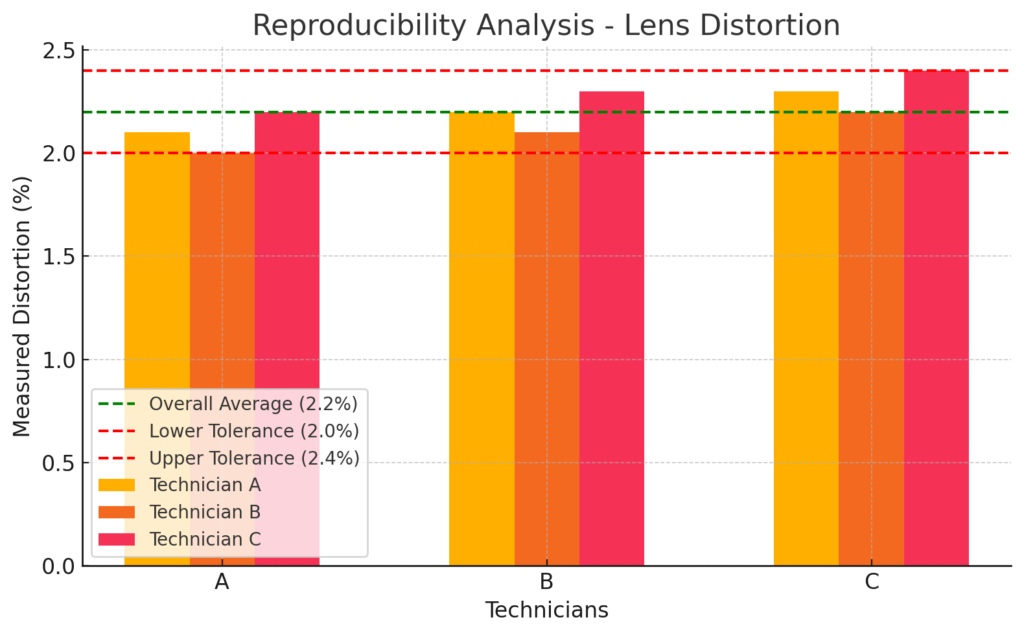
Gauge R&R(繰り返し性と再現性分析)の概要
Gauge R&R(Gage Repeatability and Reproducibility)は、MSA(測定システム分析)の一環として、測定システムの信頼性を定量的に評価するための手法です。測定システムが正確であるかどうかを判断するには、繰り返し性(Repeatability)と再現性(Reproducibility)の評価が欠かせません。
Gauge R&Rの目的とMSAとの関連
MSAは、測定システムの全体的な性能を評価する枠組みであり、その中でGauge R&Rは以下を特に重視します:
- 繰り返し性:同一の測定者が同一条件下で繰り返し測定した場合のばらつき。
- 再現性:異なる測定者や条件で測定した場合のばらつき。
これらの評価を通じて、測定システム全体の信頼性が確認され、得られたデータが品質改善やプロセス管理に有効活用できるかどうかが判定されます。
Gauge R&Rの具体的な手順
- 試料の選定
測定する対象物(例:10個のカメラセンサー)を異なる製造ロットから選び、ばらつきのサンプルを確保。 - 測定者の割り当て
3人の技術者を測定担当者として選定し、各試料を3回ずつ測定。 - データ収集
各測定者が取得した全ての測定値を記録。 - 結果の計算
データを統計的に分析し、全体のばらつきに占める繰り返し性と再現性の割合を算出。
数値例
以下のようなデータを基にGauge R&Rの結果を計算します:
- 繰り返し性のばらつき:25%
- 再現性のばらつき:15%
- Gauge R&Rの割合(繰り返し性と再現性を合わせた値):40%
これが総ばらつき(測定対象物と測定システムの合計)の30%以下であれば、測定システムは「良好」と評価されます。
カメラ設計における具体例
例として、カメラセンサーのピクセル精度を測定する場合を考えます:
- 試料:異なる製造ロットから取得した10個のセンサー。
- 測定者:技術者A、B、Cの3人。
- 測定項目:ピクセルの誤差率(%)。
- 測定結果:
- 技術者A:0.1%、0.2%、0.1%、…
- 技術者B:0.2%、0.3%、0.2%、…
- 技術者C:0.1%、0.2%、0.1%、…
- 結果:
- 繰り返し性のばらつき:0.05%
- 再現性のばらつき:0.07%
- 合計ばらつき(Gauge R&R):0.12%
この値が全体ばらつきの10%以下であれば、測定システムは非常に信頼性が高いと評価されます。
Gauge R&Rは、測定システムの精度と信頼性を定量的に評価するための基本的なツールです。MSAの一環として実施することで、データの正確性を保証し、プロセス改善や品質向上の基盤を構築できます。カメラ設計のような精密な分野では特に重要であり、顧客要件を満たす製品開発に大きく貢献します。
IATF 16949初心者向け導入ステップ
IATF 16949の導入において、現状分析とギャップアセスメントは出発点となる重要なプロセスです。
これにより、組織が現在の業務プロセスや品質管理体制を見直し、規格要求との差異を特定することが可能です。
例えば、カメラ設計の現行プロセスや品質基準を評価し、不足している部分や改善が必要な領域を洗い出します。
一方で、品質マネジメントシステム(QMS)の構築は、IATF 16949を効果的に運用するための基盤です。
これには品質目標の設定やプロセスの標準化、リスク管理の強化などが含まれます。さらに、認証取得の準備では適切な文書整備やトレーニングが不可欠です。
この記事では、導入に必要な各プロセスを具体例を交えて解説し、成功に導くためのポイントを明らかにします。
現状分析とギャップアセスメント
現状分析とギャップアセスメントは、IATF 16949の導入を成功させるために欠かせない第一歩です。このプロセスでは、組織の現行の業務プロセスや品質管理体制を評価し、IATF 16949の要求事項との差異を特定します。以下では、カメラ設計における具体例を交えながら説明します。
現状分析の具体例:カメラ設計プロセスの評価
カメラ設計部門においては、以下の要素を分析することが一般的です:
- 現行の設計フロー
例:新製品開発のプロセスが市場要求に基づいて設計目標を定め、その後、試作品の製造までが効率的に進行しているか確認します。 - 品質管理手順
例:レンズの解像度や耐久性の測定が統一された基準で行われているか、使用する測定装置の校正が適切かを確認します。 - リスク管理体制
例:新しいセンサー技術を導入した場合の不良率や顧客クレームの可能性を事前に評価し、リスク軽減策を講じているかをチェックします。
ギャップアセスメントの具体例:IATF 16949との差異特定
現状分析で得られた情報を基に、IATF 16949の要求事項とのギャップを特定します。カメラ設計における具体例は次の通りです:
- 不足している設計レビューの記録
現状では、設計レビューが非公式な会議で行われており、文書化されていない場合があります。これにより、後続の工程で問題が発生しても原因追跡が難しくなります。 - 不十分な顧客要件のトレース
例:顧客が求める防水性能が設計仕様に正しく反映されていないため、量産後のクレームにつながるリスクがある。 - 試作品テストの標準化不足
現状では、試作品の耐久テストが設計チーム内で統一された基準で実施されていないことが判明しました。これにより、品質のばらつきが生じる可能性があります。
包括的な評価の重要性
現状分析とギャップアセスメントは、設計部門だけでなく、製造、品質管理、調達部門など全社的に行う必要があります。一部の部署だけを分析すると、全体の統一性が損なわれ、IATF 16949の導入後に問題が生じる可能性があります。
- 全社的な視点の具体例
設計部門が新しいカメラモジュールを開発する際に、製造部門との連携が不足していると、量産工程での不良率が高まるリスクがあります。このため、設計と製造のプロセス間のギャップを特定し、改善策を講じる必要があります。
ギャップ解消に向けた次のステップ
ギャップアセスメントの結果を基に、以下のような具体的な改善アクションを立案します:
- 標準化の推進
設計レビューや試作品テストに統一基準を導入し、全てのプロセスを標準化。 - リソースの強化
新しい測定機器の導入や、設計者への追加トレーニングを実施。 - 継続的なモニタリング
改善の進捗をモニタリングし、定期的にギャップアセスメントを再実施する。
現状分析とギャップアセスメントは、IATF 16949を成功裏に導入するための基盤です。特に、カメラ設計においては、設計フローや品質基準、顧客要件との一致を徹底的に確認することで、効率的かつ高品質な製品開発が可能になります。
品質マネジメントシステムの構築
品質マネジメントシステム(QMS)の構築は、IATF 16949を効果的に導入するための最重要プロセスです。QMSは、品質基準を組織全体で統一し、標準化するための仕組みであり、品質目標の達成を支援する基盤となります。以下では、具体例を交えて詳細に説明します。
品質マネジメントとは
製品やサービスが顧客の期待や要求を満たすように、組織全体で計画的かつ体系的に品質を管理・改善するための考え方や手法の総称です。その目的は、顧客満足度を向上させ、組織の信頼性と競争力を高めることにあります。
品質マネジメントは、単に製品の不良を防ぐだけでなく、プロセスや仕組みそのものを最適化することで、継続的に品質を向上させる役割を果たします。この取り組みは、製造業だけでなく、サービス業やIT業界など幅広い分野で重要視されています。
品質マネジメントの基本要素
- 計画(Plan)
- 顧客の要求を明確にし、品質目標を設定。
- 例: カメラメーカーが「解像度1200dpiを達成」「年間不良率1%未満」を目標とする。
- 実行(Do)
- 計画した内容を基に、製造やサービス提供を実施。
- 例: 設計段階での試作品テストや製造ラインの調整を行う。
- 確認(Check)
- 実施した内容を評価し、目標達成状況を確認。
- 例: 顧客アンケートを実施し、製品の満足度を分析。
- 改善(Act)
- 確認結果を基に、必要な改善を行う。
- 例: 顧客から寄せられたフィードバックを設計や製造プロセスに反映する。
品質マネジメントシステム構築の基本ステップ
- 品質方針と目標の設定
- 具体例: カメラメーカーが「顧客満足度95%以上」「不良品率1%未満」を目標とする場合、これを全社的に共有します。
- プロセスの設計と標準化
- 製品の設計から生産、出荷、顧客サポートまでの各プロセスをフローチャートで明確化。
- 具体例: カメラ設計では、試作品のテスト工程を「初期性能試験」「長期耐久試験」「環境ストレス試験」といったステージに分割し、詳細な手順を文書化します。
- 役割分担の明確化
- 各部署や従業員が担うべき役割を明示。
- 具体例: 設計チームがレンズ性能の評価を行い、品質管理部門がその評価結果を基にプロセスの適合性を確認する仕組みを構築。
- 手順書と記録の整備
- 製造手順や品質チェックリストを標準化し、文書化。
- 具体例: レンズの光学性能を検査する際の基準や測定手順を、マニュアル化して共有。
- リスク評価と対策
- 製造や設計で発生するリスクを特定し、FMEAなどのツールを使用して対応策を講じる。
- 具体例: 新型センサーの初期不良率が予想以上に高い場合、予備テスト段階での評価項目を拡充し、量産前に改良を加える。
システム構築における注意点
- 組織規模に応じた設計
- 具体例: 中小企業のカメラメーカーでは、全てのプロセスを過剰に文書化するのではなく、重要なポイントだけを簡潔にまとめたシステムを採用。
- シンプルかつ実行可能な設計
- 過剰に複雑なシステムは現場での運用が困難になります。
- 具体例: 設計変更時に使用する承認フローを、電子フォームで簡単に提出・承認できるシステムにする。
- 継続的な改善
- システムは構築して終わりではなく、定期的なレビューと改善が必要です。
- 具体例: 毎月の品質ミーティングで、カメラセンサーの生産不良率や顧客からのクレーム件数を基に改善計画を策定。
品質マネジメントシステムの導入後のメリット
- 品質の一貫性
- 標準化された手順により、製品品質が安定。
- 具体例: 全てのレンズが均一な透過率を維持することで、撮影結果が安定。
- 顧客満足度の向上
- 不良品率の低減や迅速な顧客対応により、信頼が向上。
- 具体例: 修理依頼が減少し、新規顧客の紹介が増加。
- コスト削減
- プロセスの効率化と不良品削減により、製造コストが削減。
- 具体例: レンズの再加工率を10%から2%に削減することで、コストを20%削減。
実施例:カメラ設計におけるQMS構築プロジェクト
- 現状分析
- 設計プロセスにおいて、設計変更が頻発し、顧客要件を満たさないケースが多発していた。
- 改善策
- 新たな設計フローを導入し、顧客要件を設計仕様に正確に反映。
- 試作品テストでの欠陥発見率を20%向上させる目標を設定。
- 結果
- 製品開発期間が10%短縮され、顧客からのクレームが30%減少。
品質マネジメントシステムの構築は、IATF 16949の導入成功の鍵を握ります。特にカメラ設計のような高度な技術が求められる分野では、QMSの標準化がプロセス効率や製品品質の向上に直結します。システム構築の初期段階から全社的な取り組みを進めることで、持続的な成長と顧客満足度の向上を実現できます。
文書化と記録の整備
IATF 16949では、適切な文書化と記録の整備が求められます。これにより、品質管理のプロセスが一貫して実行されていることを証明し、後の監査にも対応できます。
具体的には、プロセス手順書、コントロールプラン、記録管理のためのテンプレートなどを作成します。また、これらの文書が従業員にとって使いやすく、理解しやすい形式であることが重要です。
文書化の際は、頻繁に更新が必要な部分と固定的な情報を明確に分けることで、維持管理が容易になります。また、文書を電子化することで検索性を向上させ、効率的な運用が可能となります。
トレーニングと意識向上活動
トレーニングと意識向上活動は、IATF 16949を成功裏に導入するために欠かせないステップです。従業員が新しい品質管理体制を理解し、自分たちの役割を明確に認識することが求められます。
例えば、新しいプロセスの操作方法や問題発生時の対応手順についてのトレーニングを実施します。また、意識向上のために、品質管理の重要性を伝える社内セミナーやキャンペーンを行うことも効果的です。
注意点として、トレーニングは一度で完了するものではなく、定期的に実施して知識を更新する必要があります。また、全員が参加できるよう、スケジュール調整や柔軟な開催形式を検討することも大切です。
認証取得のプロセスと注意点
認証取得のプロセスは、IATF 16949の最終ステップであり、重要な節目となります。このプロセスでは、第三者機関による審査を受け、基準を満たしていることが確認されます。
一般的には、事前審査、本審査、フォローアップ審査という段階を経て認証が発行されます。この間に、審査官から指摘を受けた点は迅速に是正し、基準への適合性を高めることが必要です。
注意すべき点は、審査の準備段階からしっかり計画を立てることです。必要な文書や記録が整備されていない場合、審査の進行が遅れる可能性があります。また、認証取得後も継続的な改善活動が求められるため、一度の取得で満足せず、維持管理に注力することが重要です。
初心者が陥りやすいポイントと回避策
IATF 16949の導入や運用において、初心者が陥りやすい課題を理解し、効果的に対策を講じることは、品質管理システムの成功に不可欠です。
本記事では、過剰な文書化や監査への準備不足、顧客要求事項の誤解、サプライヤー管理の失敗といった一般的な問題を取り上げ、その具体的な回避策を解説します。
また、継続的改善を推進するための実践的な方法も詳述し、これらを通じて組織全体の品質と効率を高めるためのヒントを提供します。
初心者から経験者まで、IATF 16949の運用を成功に導くための知識と実践法を共有します。
過剰な文書化のリスクと適切な管理方法
過剰な文書化は、品質管理システムの導入において避けるべき課題の一つです。文書が多すぎると、従業員が必要な情報を見つけにくくなり、効率を損なう可能性があります。また、不要な文書の維持管理にコストと時間がかかる点もデメリットです。
適切な管理方法として、必要最低限の文書化を目指し、業務フローに直接関係する重要な手順や記録に焦点を当てることが挙げられます。例えば、プロセスフロー図や主要なチェックリストを簡潔にまとめることで、従業員が情報を素早く確認できるようになります。
さらに、定期的に文書を見直し、古くなった内容や重複している情報を削除することも有効です。このようにして、文書化が目的ではなく、実用性を重視した運用が可能となります。
監査への準備不足の回避方法
監査への準備不足は、IATF 16949の認証取得や維持において大きなリスクとなります。不備が見つかると、指摘事項への対応が求められ、審査が遅延する可能性があります。
回避するためには、日常的な業務の中で監査を意識した運用を行うことが重要です。例えば、全ての記録を適切に保管し、求められた際にすぐに提示できるようにしておくことが有効です。また、内部監査を定期的に実施し、外部監査前に潜在的な問題を洗い出して改善することも役立ちます。
さらに、監査準備チームを組織し、全体の進捗管理を徹底することで、スムーズな監査対応が可能となります。
顧客要求事項の誤解を防ぐ方法
顧客要求事項を誤解することは、品質や納期のトラブルを引き起こす可能性があります。このようなリスクを防ぐには、初期段階での詳細な確認が重要です。
まず、顧客から提供された仕様書や契約内容を徹底的に精査し、不明点があれば必ず確認することが求められます。また、顧客とのミーティングを設け、要求事項を具体的に議論することで、相互理解を深めることができます。
さらに、顧客の要求事項を社内で共有する際には、簡潔でわかりやすい形式で文書化し、全員が理解できるよう工夫します。このプロセスを徹底することで、誤解やトラブルのリスクを最小限に抑えることが可能です。
サプライヤー管理の重要性と失敗例
サプライヤー管理は、IATF 16949の中で重要な要素です。不十分な管理は、不良品の増加や納期遅延といった問題を引き起こす可能性があります。例えば、過去にはサプライヤーの能力を過信し、必要な品質基準を満たさない部品が納入され、顧客クレームに繋がった事例もあります。
このような失敗を防ぐためには、サプライヤーの選定や評価を慎重に行い、定期的にパフォーマンスをモニタリングすることが重要です。また、品質基準や納期に関する明確な契約条件を設定し、これを遵守させる仕組みを導入することも効果的です。
さらに、サプライヤーとの緊密なコミュニケーションを維持し、潜在的なリスクを事前に特定して対応することで、問題発生を未然に防ぐことができます。
継続的改善を進めるための具体的な方法
継続的改善は、IATF 16949の基本原則の一つであり、品質向上と効率化を実現するための鍵となります。これを実現するためには、定期的なプロセス評価とデータ分析が重要です。
例えば、月次の品質会議を開催し、不良品率や顧客満足度のデータを共有しながら改善策を議論します。また、従業員からの改善提案を募る仕組みを設けることで、現場の知識を活用した効果的な改善が期待できます。
さらに、改善活動の成果を定量的に評価し、成功事例を社内で共有することで、他部門への波及効果を生むことができます。このような具体的な取り組みにより、継続的な改善が組織文化として根付くようになります。
IATF16949とISO9001の違いを理解するためのポイント
本記事のまとめを以下に列記します。
- IATF16949は自動車産業に特化しているが、ISO9001は汎用的な品質マネジメントシステムである
- ISO9001はあらゆる業界に適用可能だが、IATF16949は自動車メーカーや部品サプライヤーを対象としている
- IATF16949はISO9001を基盤にしつつ、自動車業界特有の要件を追加している
- ISO9001は顧客満足や継続的改善を重視するが、IATF16949は製品安全やトレーサビリティも重点に置いている
- IATF16949ではサプライヤー管理が厳格で、サプライヤーのISO9001準拠が必須条件となる
- 製品安全責任者の任命がIATF16949で義務付けられているが、ISO9001にはない
- ISO9001は製造業以外にもサービス業や非営利組織に適用できる
- IATF16949では顧客固有の要求事項(CSR)に対応するプロセスが求められる
- トレーサビリティがIATF16949の必須要件であり、製品の追跡が可能である必要がある
- ISO9001は一般的なリスク管理を重視するが、IATF16949は製造停止リスクへの具体的対応を求める
- 内部監査の範囲がIATF16949の方が広く、製造プロセスやシフト交代時の管理まで含まれる
- IATF16949ではPPAPやFMEAなど自動車業界特有のツールが必須とされる
- ISO9001は品質記録の推奨に留まるが、IATF16949では詳細な記録が義務付けられる
- IATF16949はISO9001よりも製品安全と顧客要求への厳密な適合を強調している
- IATF16949はISO9001に比べ、規格の維持におけるリソースとコストの負担が大きい
コメント